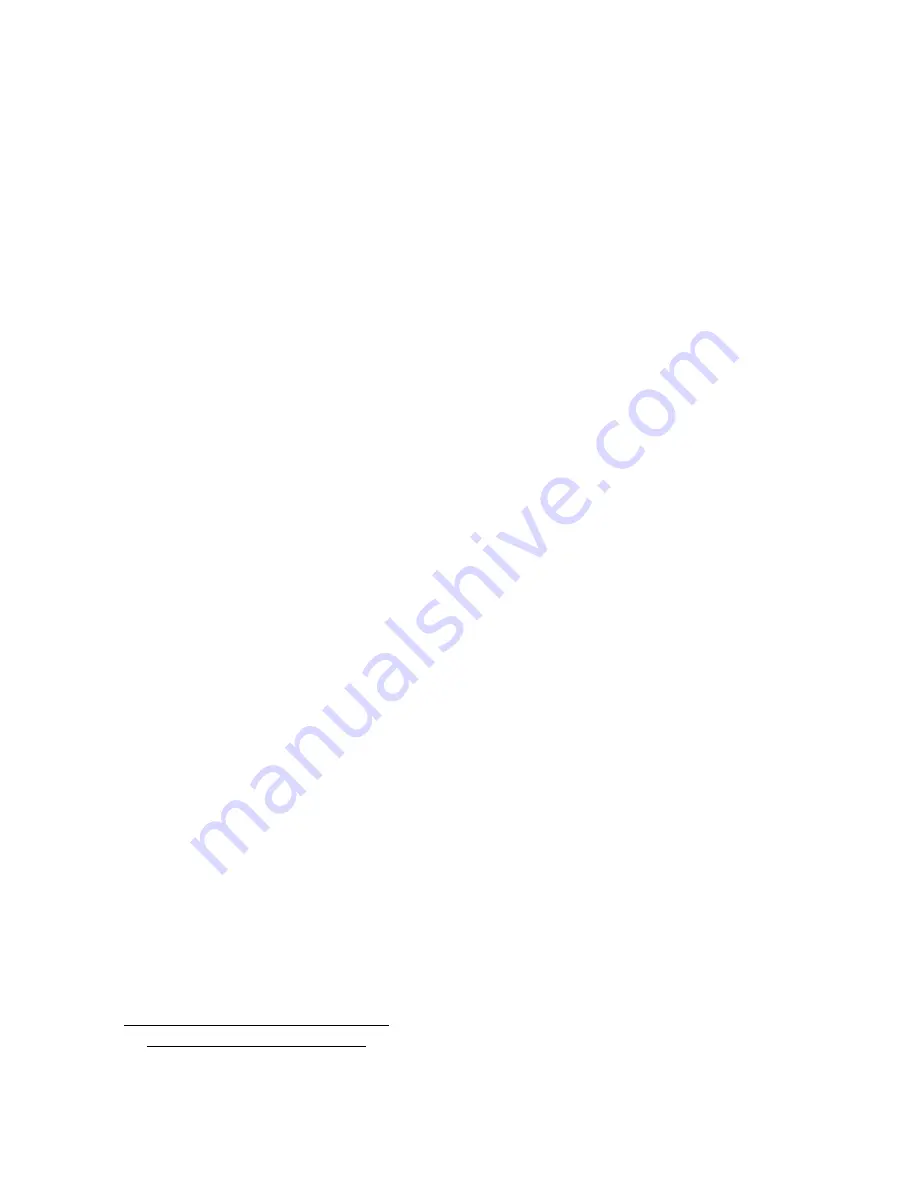
THRUSH AIRCRAFT, INC – MODEL S2R-R1340
AIRCRAFT MAINTENANCE MANUAL
F. Repair of tail gear sub-assembly is
limited to reconditioning of parts such
as replacing bearings and bushings,
smoothing out minor nicks and
scratches, repainting chipped or
peeled areas and replacement of
component parts.
TAIL GEAR WHEEL AND TIRE
REMOVAL AND DISASSEMBLY
Ref. figure 6-8
To remove and disassemble tailwheel &
tire, proceed as follows.
A. Using a suitable Jack. Jack and
secure tail of aircraft at tailwheel
trunnion jackpoint.
B. Deflate tire by depressing the
schrader valve stem plunger until air
can no longer be heard escaping
from the tire.
C. Remove schrader valve core.
D. Remove cotter pin and through bolt
castellated nut. Remove the through
bolt, cut the safety wire to collar nut
and remove the wheel and axle.
Unscrew the collar nut and remove
the axel from the wheel.
E. From each side of wheel; carefully
remove snap ring, felt grease seal
retainer, felt grease seal, grease seal
ring and cone bearing. Store the
cone bearings. Label the bearings
for reinstallation into position from
which it was removed.
F. With the tire completely deflated,
removing the wheel through-bolts will
separate the wheel halves. Pull the
wheel halves from the tire by
removing the wheel half opposite the
valve stem first. Mark wheel halves
to note relationship to each other for
reassembly.
INSPECTION OF TAIL LANDING
GEAR WHEEL ASSEMBLY
A. Visually check all parts for cracks,
corrosion, distortion, defects and
excessive wear.
B. Inspect felt grease seals. Replace if
surface is hard or contaminated, or
shows evidence of excessive wear.
Lightly saturate grease seal felts with
SAE 10wt. Oil (3-in-ONE oil) (do not
soak).
C. Inspect tire for cuts, anomalies,
internal damage and deterioration.
D. Inspect inner tube for cuts, wrinkles,
anomalies and deterioration. Do not
use a used inner tube with a new
tire. Tubes grow in service, taking a
permanent set of about 25% larger
than original size. This makes a used
tube too large to use in a new tire,
which could cause a wrinkle and
lead to tube failure.
E. Inspect wheel bearing grease for
contamination and solidification at
each periodic inspection. Repack
bearings with MIL-G-81322
(Aeroshell 22) or equivalent grease.
Note: Do not exceed 500 wheel
miles or on annual inspection
whichever comes first between
repacking intervals.
F. Clean and inspect bearing cups and
cones. Note: Do not spin dry
bearings or handle bearing
components with bare hands. The
bearing cup should not be removed
except when replacement is
necessary due to scratches, nicks,
pitting, spalling, corrosion, brinelling,
or evidence of overheating. Note: If
bearing cup is replaced, its
companion bearing cone must also
be replaced.
G. Bearing cup removal: Heat wheel
half in an oven not exceeding 212°F
for 15 minutes. Remove wheel half
from heat source and immediately
remove bearing cup by carefully
tapping out evenly from the inside
6-16
Effective:
01/01/08