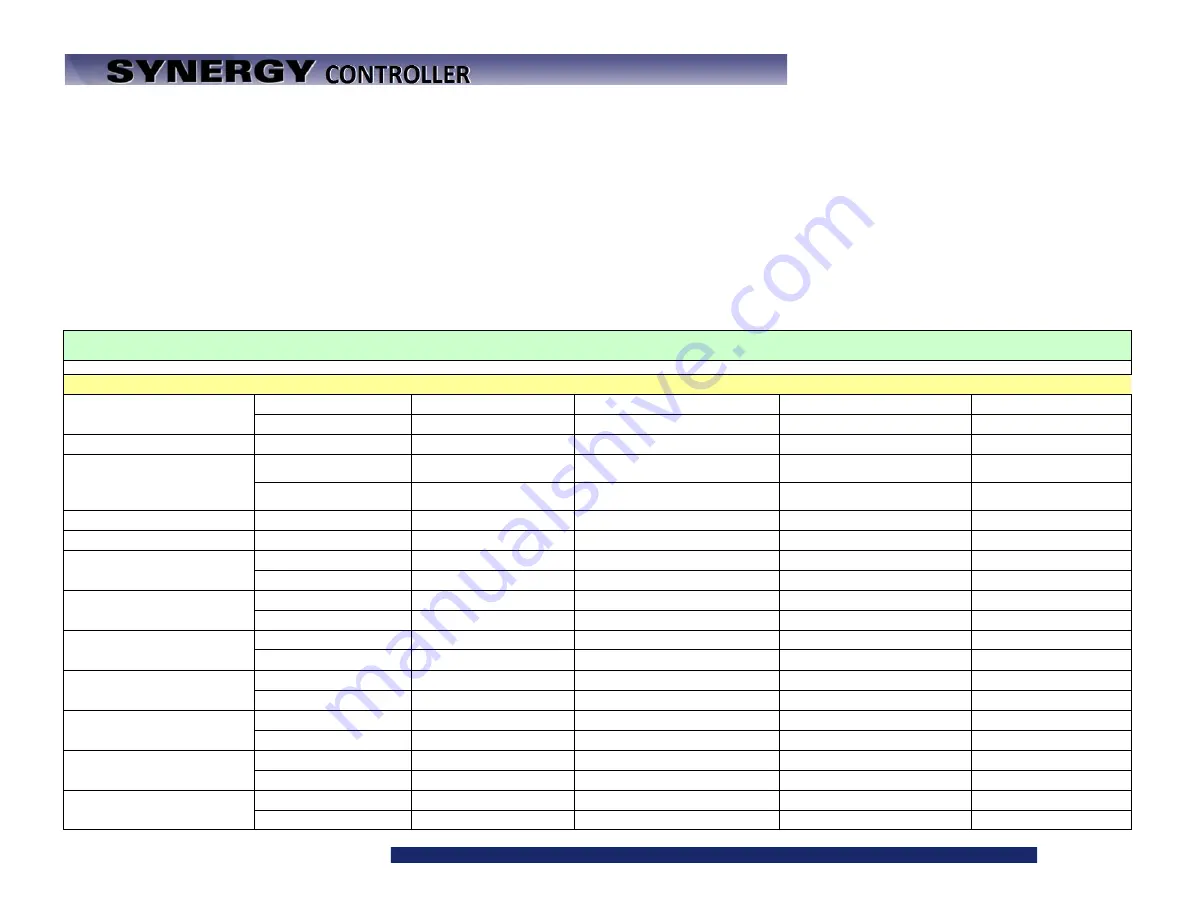
Synergy Controller Technical Manual, Revision H
Page 229
Page 229
17.2 Synergy Controller Command Set
SYNERGY COMMUNICATION COMMAND SET
Tidal Engineering Corporation © 2001-2015
File: SYNERGY COMMUNICATION COMMANDS VERSION 4.0.0.xls
Date: 28 August 2015
Notes:
1. Many commands support a RANGE, MIN and MAX queries which return the High and Low range allowed for the command. Ex: ? CAL1 RANGE returns -50.000,50.000
2. The Asterisk "*" is used in the Synergy Controller command set as a place holder for the channel number. * is the channel number = 1,2, 3 or 4
3. The Number Sign "#" is used in the Synergy Controller command set as a place holder for an index. Ex. HIGH#_GAIN where # is the High Resolution Input 1 - 6
Description
Command Usages
Command Syntax
Range,
Units
Command
Example
Response Example
Control Commands
Ch * Setpoint
SP* Set
= SP* X.X
Range = R*L to R*H or OFF
= SP1 100.7
OK
SP* Query
? SP*
? SP1
100.7
Ch * Actual
C* Query
? C*
Range =R*L to R*H or OFF
? C1
25.0
Ch * Sensor Select
CH*Sensor Set
= CH*SENSOR ARG1
ARG1 - ID of the Sensor. 100 -
999.
= CH1SENSOR 110
OK
CH* Sensor Query
? CH*SENSOR
See the user manual for numeric
codes.
? CH1SENSOR
110
Ch * Cooling Output
1LO Query
? *LO
0 - 100 %
? 1LO
0.0
Ch * Heating Output
1HI Query
? *HI
0 - 100 %
? 1HI
100.0
Ch * Heat Prop. Band
PB*H Set
= PB*H ARG1
0 to 50 C 0 to 90 F
= PB1H 10
OK
PB*H Query
? PB*H
0 to 50 C 0 to 90 F
? PB1H
10.00
Ch * Heat Reset
RS*H Set
= RS*H ARG1
0 - 09.999 Repeats / Minute
= RS1H .02
OK
RS*H Query
? RS*H
0 - 09.999 Repeats / Minute
? RS1H
0.020
Ch * Heat Rate
RT*H Set
= RT*H ARG1
0 - 09.999 Minutes
= RT1H
OK
RT*H Query
? RT*H
0 - 09.999 Minutes
? RT1H
1.000
Ch * Heat Cycle Time
CT*H Set
= CT*H ARG1
1 - 60 Seconds
= CT1H 5
OK
CT*H Query
? CT*H
1 - 60 Seconds
? CT1H
5.00
Ch * Heat Rate Band
RB*H Set
= RB*H ARG1
0 - 7 Seconds
= RB1H 4
OK
RB*H Query
? RB*H
0 - 7 Seconds
? RB1H
4.000
Ch * Dead Band
DB* Set
= DB* ARG1
-25 to 25 C -45 to 45 F
= DB1 5
OK
DB* Query
? DB*
-25 to 25 C -45 to 45 F
? DB1
5.00
Ch * Cool Prop Band
PB*C Set
= PB*C ARG1
0 to 50 C 0 to 90 F
= PB1C 10
OK
PB*C Query
? PB*C
0 to 50 C 0 to 90 F
? PB1C
10.00
Summary of Contents for Synergy Compact
Page 14: ...Synergy Controller Technical Manual Revision H Page 14 2 0 SPECIFICATIONS 2 1 Data Sheet...
Page 71: ...Synergy Controller Technical Manual Revision H Page 71...
Page 106: ...Synergy Controller Technical Manual Revision H Page 106...
Page 123: ...Synergy Controller Technical Manual Revision H Page 123...
Page 141: ...Synergy Controller Technical Manual Revision H Page 141 TE1151 6 Triac Output Board Schematic...
Page 142: ...Synergy Controller Technical Manual Revision H Page 142 TE1708 6 Relay Board Schematic...
Page 188: ...Synergy Controller Technical Manual Revision H Page 188...
Page 274: ...Synergy Controller Technical Manual Revision H Page 274 Synergy Controller Step Syntax...
Page 294: ...Synergy Controller Technical Manual Revision H Page 294...
Page 312: ...Synergy Controller Technical Manual Revision H Page 312...
Page 345: ...Synergy Controller Technical Manual Revision H Page 345...
Page 346: ...Synergy Controller Technical Manual Revision H Page 346...