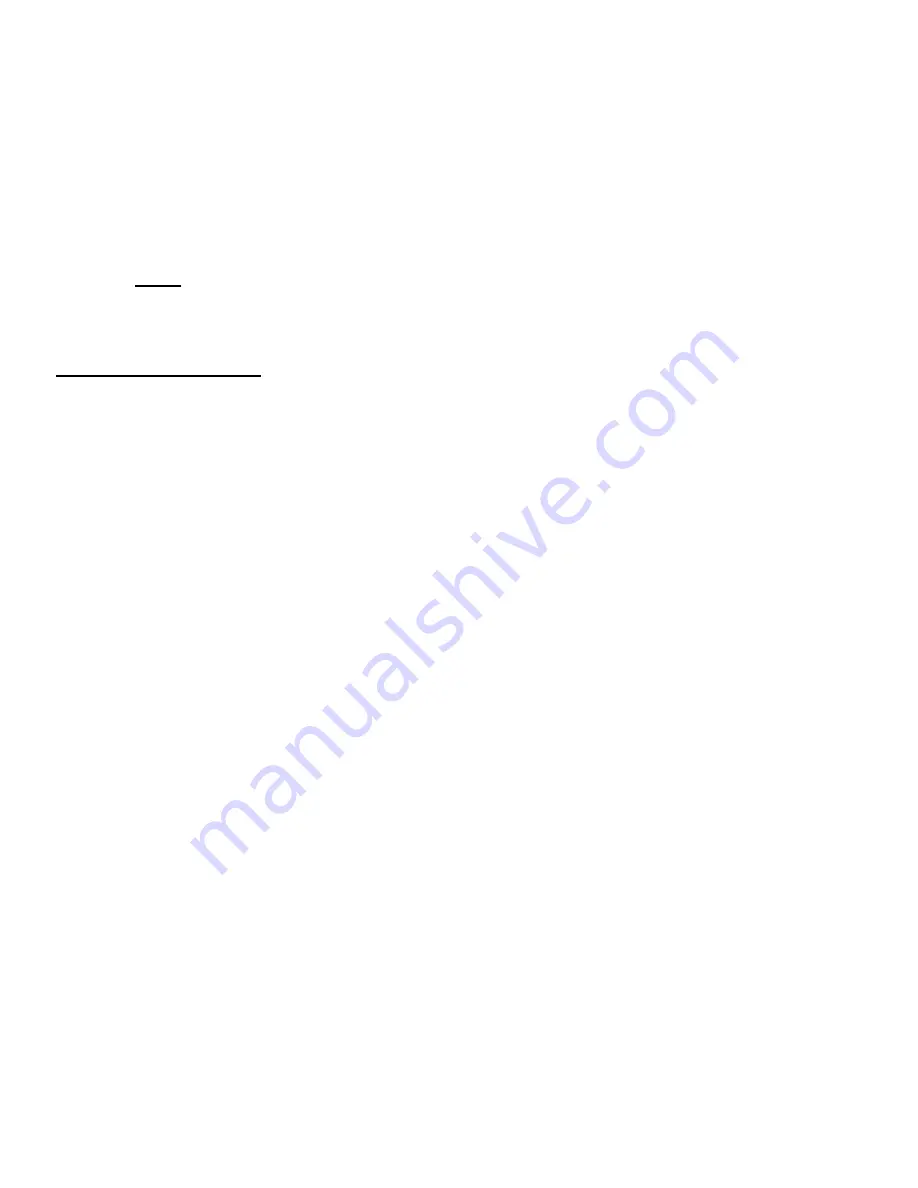
Page 4
Other parts of the
STAR-BRAKE
serve to control and
coordinate the action of the braking current, to form a
complete braking system. These are described in the
balance of this section.
8.2 Detail Description
8.2.1
Sensing
This is the part of the system that determines when
braking is required. It consists of circuitry which detects
when the motor is
ON
by sensing the current flowing
through the internal interlock to the starter contactor.
When this current is removed (starter contactor is
disengaged) the brake is activated.
Note: leakage current in the magnetic starter control loop
when the starter is disengaged may be interpreted by the
sensor as a motor run condition, not allowing the brake to
pull in.
8.2.2
Interlock
Once an "OFF" condition is determined by the sensor, the
interlock is opened. This prevents the motor from being
re-started while the braking function is in progress. The
interlock will not be re-established until braking has been
completed.
8.2.3
Logic and Timing
This section initiates the flow of DC power after the
braking contactor has been closed; removes the DC
power and opens the braking contactor at the end of
braking; and re-closes the interlock as the last item in the
braking cycle, restoring control to the motor starter.
8.2.4
DC Power and Control
Under control of the Timing section, this block has the
function of setting up the path for the flow of DC current to
the motor, and for rectifying power from the AC input
supply for DC braking.
Rectification is done by means of a "Controlled Rectifier,"
or SCR. This device conducts for a controllable part of
each AC power line cycle. By setting the phase angle
allowed for conduction via the Torque pot, the amount of
DC current produced for braking can be controlled.
The Controlled Rectifier is not turned ON until after the
braking contactor has closed. It is turned OFF before this
contactor is allowed to open. In this way, the contactor is
never called on to switch under load, and the contacts
therefore experience no wear or arcing - even though they
are carrying DC. This is why it is imperative that the
braking cycle be allowed to run to completion in the
normal way.
9. IF YOU HAVE A PROBLEM
9.1 Preliminary Checks
Check for possible damage in shipping, if so, notify the
freight carrier.
No adjustments are provided or required other than those
described in Section 7.
Should a system fail to perform properly, be sure to check
the wiring first. Also, be certain that the power line voltage
is present and correct. (For instance, there should be
equal voltages between any two leads of a three phase
power line, and these should be in the correct nominal
range for the
STAR-BRAKE.)
If the system has previously been operating properly, it is
also a good idea to check the fuses, and that the
adjustments of the three controls, TIME, TORQUE and
OVERLOAD have not been tampered with. Note: 230 volt
units operated from 208 volts will produce somewhat
lower torque. Consult the factory if this is a problem.
If there is a problem on initial installation, or if the brake
should fail to function properly, the following checks
should be made:
9.2 Motor Will Not Start
1. Verify that there is normal line voltage across Termi-
nals L1, L2, L3. Note: 230 volt units operated from a
208 volt line may not allow the starter to engage. (208
volt Models are available.)
2. Verify that the START and STOP switches are wired
properly. AC control voltage should be present across
START switch. When the switch is pressed you
should read ZERO volts. When the START button
and the STOP button are pressed simultaneously, you
should read AC control voltage across the STOP
switch.
3. Make sure that the overload has not tripped. In case
the overload has tripped, wait 3 to 7 minutes and then
push the reset button located on the top of the over-
load. NOTE: Frequent starting and stopping, (espe-
cially with high inertia motor loads) can cause nui-
sance tripping of the overloads and fuses.
4. Make sure that the overload adjustment has not been
tampered with.