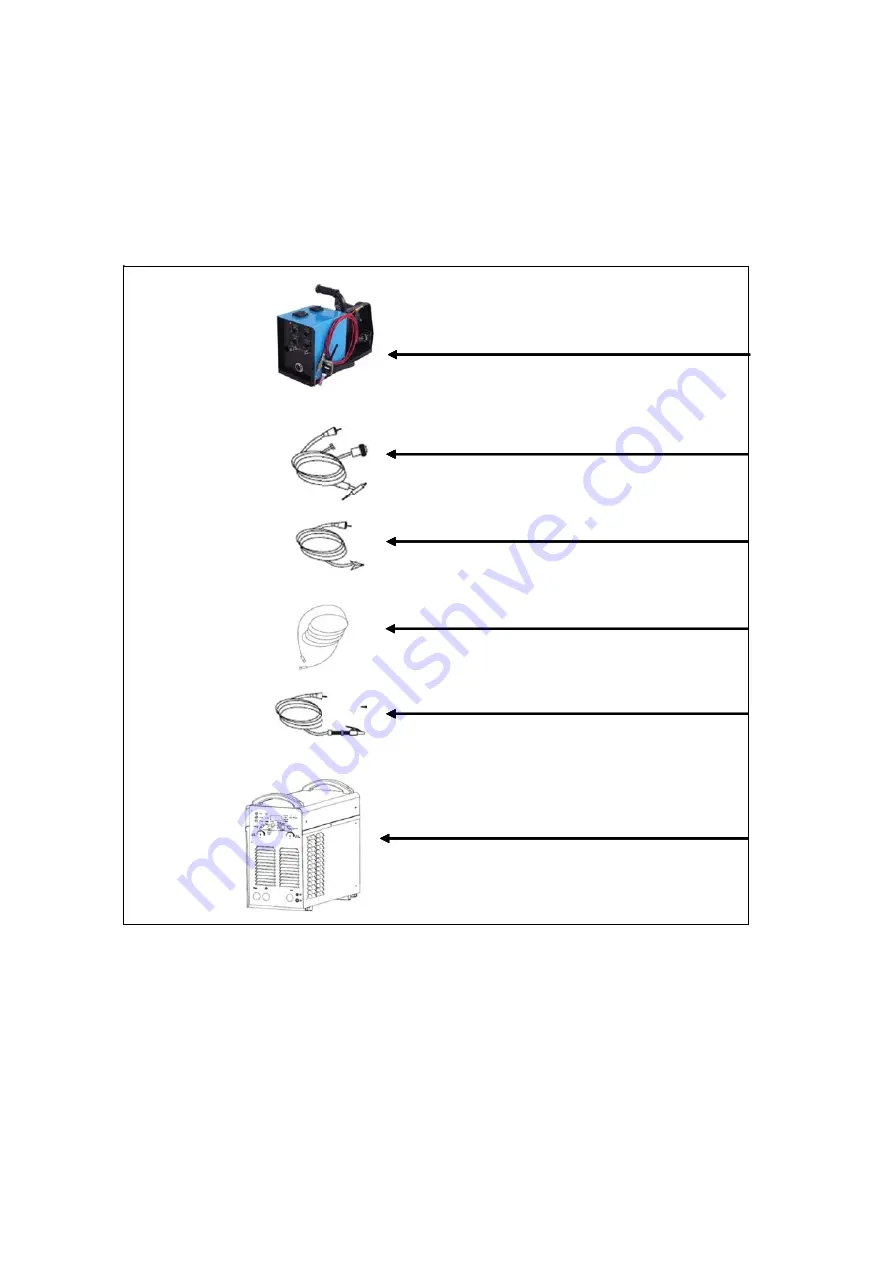
3-SB-10
3-1 Syste
This series
special site
3-2 Basic
Basic equip
-P
m compon
of machine
es with differ
equipmen
pments are
- Welding
- Welding
n
ents
es can be eq
rent configur
nts for weld
needed for n
machine
cable
uipped with
rations. Plea
Fig. 3-1-1
ding
normal weld
many differ
ase refer to
: System co
ding. Below a
rent accesso
Fig. 3-1-1.
Welding
omponents
are the lists
ories and ca
SB-10-P
TIG torch
Ground ca
Gas hose
Welding ca
machine (TI
:
an be used in
able
able
IG series)
n various
Summary of Contents for 320020-00001H
Page 1: ...TIG TIG Cold Wire Feeder ...