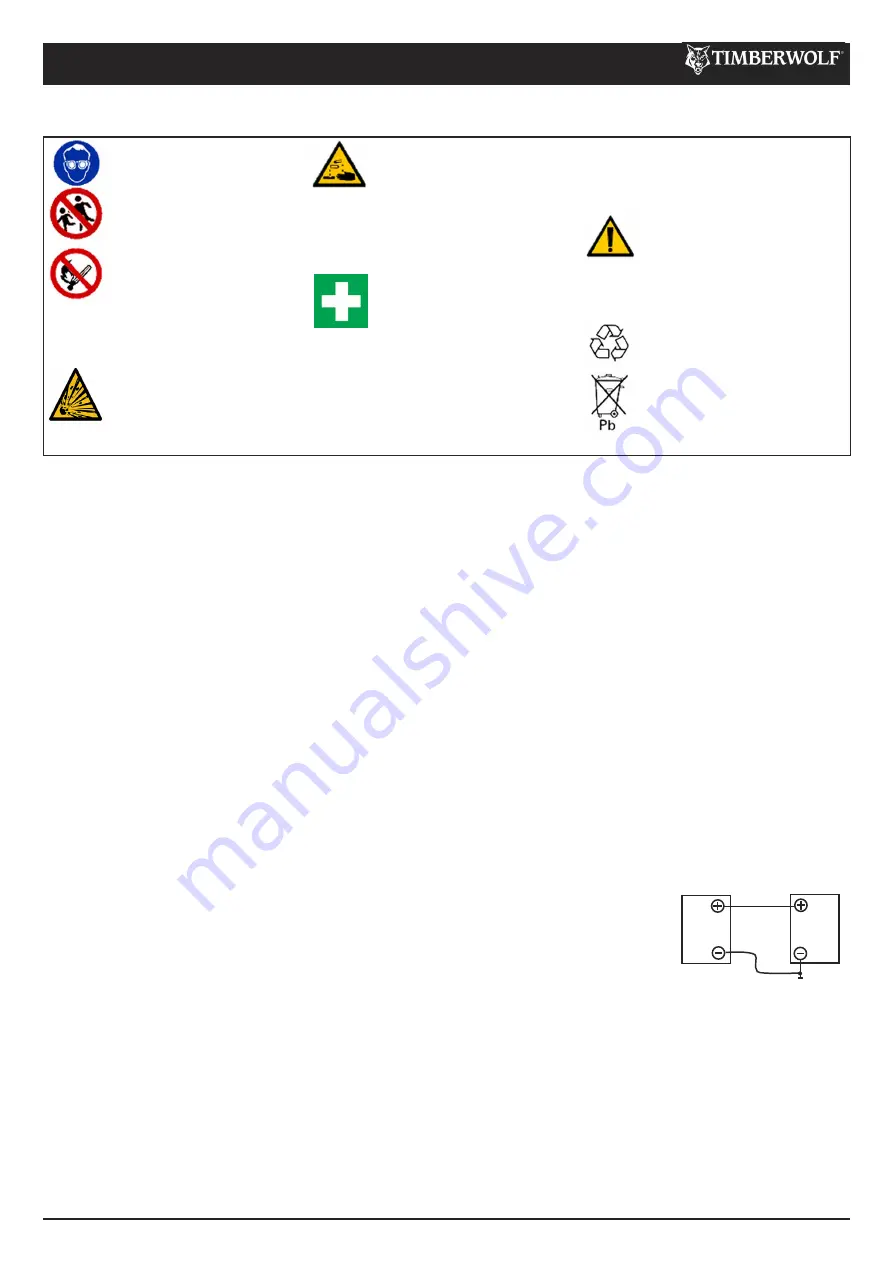
TW 160PH
SERVICE INSTRUCTIONS
17 / 51
C190-0013
11.04.2019
BATTERY SAFETY INFORMATION
1. Storage and transport
Batteries are filled with acid.
•
Always store and transport batteries upright and prevent
•
from tilting so that no acid can escape.
Store in a cool and dry place.
•
Do not remove the protective cap from the positive
•
terminal.
Run a FIFO (first in-first out) warehouse management
•
system.
2. Initial operation
The batteries are filled with acid at a density of 1.28g/ml
•
during the manufacturing process and are ready for use.
Recharge in case of insufficient starting power (see no. 4).
•
3. Installation in the vehicle and removal from the vehicle
Switch off the engine and all electrical equipment.
•
When removing, disconnect the negative terminal first.
•
Avoid short circuits caused by tools, for example.
•
Remove any foreign body from the battery tray, and
•
clamp battery tightly after installation.
Clean the terminals and clamps, and lubricate slightly
•
with battery grease.
When installing, first connect the positive terminal, and
•
check the terminal clamps for tight fit.
After having fitted the battery in the vehicle, remove the
•
protective cap from the positive terminal, and place it on
the terminal of the replaced battery in order to prevent
short circuits and possible sparks.
Use parts from the replaced battery, such as the terminal
•
covers, elbows, vent pipe connection and terminal
holders (where applicable); use available or supplied filler
caps.
Leave at least one vent open, otherwise there is a danger
•
of explosion. This also applies when old batteries are
returned.
4. Charging
Remove the battery from the vehicle; disconnect the lead
•
of the negative terminal first.
Ensure good ventilation.
•
Use suitable direct current chargers only.
•
Connect the positive terminal of the battery to the
•
positive output of the charger. Connect the negative
terminal accordingly.
Switch on the charger only after the battery has been
•
connected, and switch off the charger first after charging
has been completed.
Charging current-recommendation: 1/10 ampere of the
•
battery capacity Ah.
Use a charger with a constant charging voltage of 14.4V
•
for re-charging.
If the acid temperature rises above 55
o
Celsius, stop
•
charging.
The battery is fully charged when the charging voltage
•
has stopped rising for two hours.
5. Maintenance
Keep the battery clean and dry.
•
Use a moist anti-static cloth only to wipe the battery,
•
otherwise there is a danger of explosion.
Do not open the battery.
•
Recharge in case of insufficient starting power (see no. 4).
•
6. Jump Starting
Use the standardised jumper cable in compliance with
•
DIN 72553 only, and follow the operating instructions.
Use batteries of the same
•
nominal voltage only.
Switch off the engines of
•
both vehicles.
First connect the two
•
positive terminals (1) and (2),
then connect the negative
terminal of the charged battery (3) to a metal part (4) of
the vehicle requiring assistance away from the battery.
Start the engine of the vehicle providing assistance, then
•
start the engine of the vehicle requiring assistance for a
maximum of 15 seconds.
Disconnect the cables in reverse sequence (4-3-2-1).
•
7. Taking the battery out of service
Charge the battery; store in a cool place or in the vehicle
•
with the negative terminal disconnected.
Check the battery state of charge at regular intervals, and
•
correct by recharging when necessary (see no. 4).
(1)
(2)
(3)
(4)
12V
12V
For safety reasons, wear eye
•
protection when handling a
battery.
Keep out of reach of
•
children.
Fires, sparks, naked flames
•
and smoking are prohibited.
Avoid causing sparks when
•
dealing with cables and
electrical equipment, and
beware of electrostatic
discharges.
Avoid short circuits.
•
Explosion hazard:
A highly explosive
•
oxyhydrogen gas mixture is
produced when batteries are
charged.
Corrosive hazard:
Battery acid is highly corrosive,
therefore:
Wear protective gloves and
•
eye protection.
Do not tilt the battery, acid
•
may escape from the vent
openings.
First aid:
Rinse off acid splashed in the
•
eyes immediately for several
minutes with clear water!
Remove contact lenses if
worn and continue rinsing.
Then consult a doctor
immediately.
Neutralise acid splashes on
•
the skin or clothes
immediately with acid
neutraliser (soda) or soap
suds, and rinse with plenty of
water.
If acid is swallowed, consult a
•
doctor immediately.
Warning notes: The battery case
can become brittle, to avoid this:
Do not store batteries in
•
direct sunlight.
Discharged batteries may
•
freeze up, therefore store in
an area free from frost.
Disposal:
Dispose of old batteries at an
•
authorised collection point.
The notes listed under item 1
•
are to be followed for
transport.
Never dispose of old
•
batteries in household waste.
WARNING NOTES AND SAFETY REGULATIONS FOR FILLED LEAD-ACID BATTERIES
Summary of Contents for TW 160PH
Page 1: ...timberwolf uk com INSTRUCTIONMANUAL TW 160PH WOOD CHIPPER...
Page 25: ...TW 160PH DECLARATION OF CONFORMITY 22 51 C190 0013 11 04 2019...
Page 26: ...TW 160PH IDENTIFICATION PLATE 23 51 C190 0013 11 04 2019 EXAM PLE...
Page 37: ...TW 160PH 34 51 C190 0012 11 04 2019...
Page 38: ...35 51 C190 0012 11 04 2019 TW 160PH...
Page 39: ...36 51 C190 0012 11 04 2019 TW 160PH...
Page 40: ...TW 160PH 37 51 C190 0012 11 04 2019...
Page 41: ...TW 160PH 38 51 C190 0012 11 04 2019...
Page 42: ...TW 160PH 39 51 C190 0012 11 04 2019...
Page 44: ...TW 160PH 41 51 C190 0012 11 04 2019...
Page 45: ...TW 160PH 42 51 C190 0012 11 04 2019...
Page 46: ...TW 160PH 43 51 C190 0012 11 04 2019...
Page 47: ...TW 160PH 44 51 C190 0012 11 04 2019...
Page 48: ...TW 160PH 45 51 C190 0012 11 04 2019...
Page 49: ...TW 160PH 46 51 C190 0012 11 04 2019...
Page 50: ...TW 160PH 47 51 C190 0012 11 04 2019...
Page 51: ...TW 160PH 48 51 C190 0012 11 04 2019...