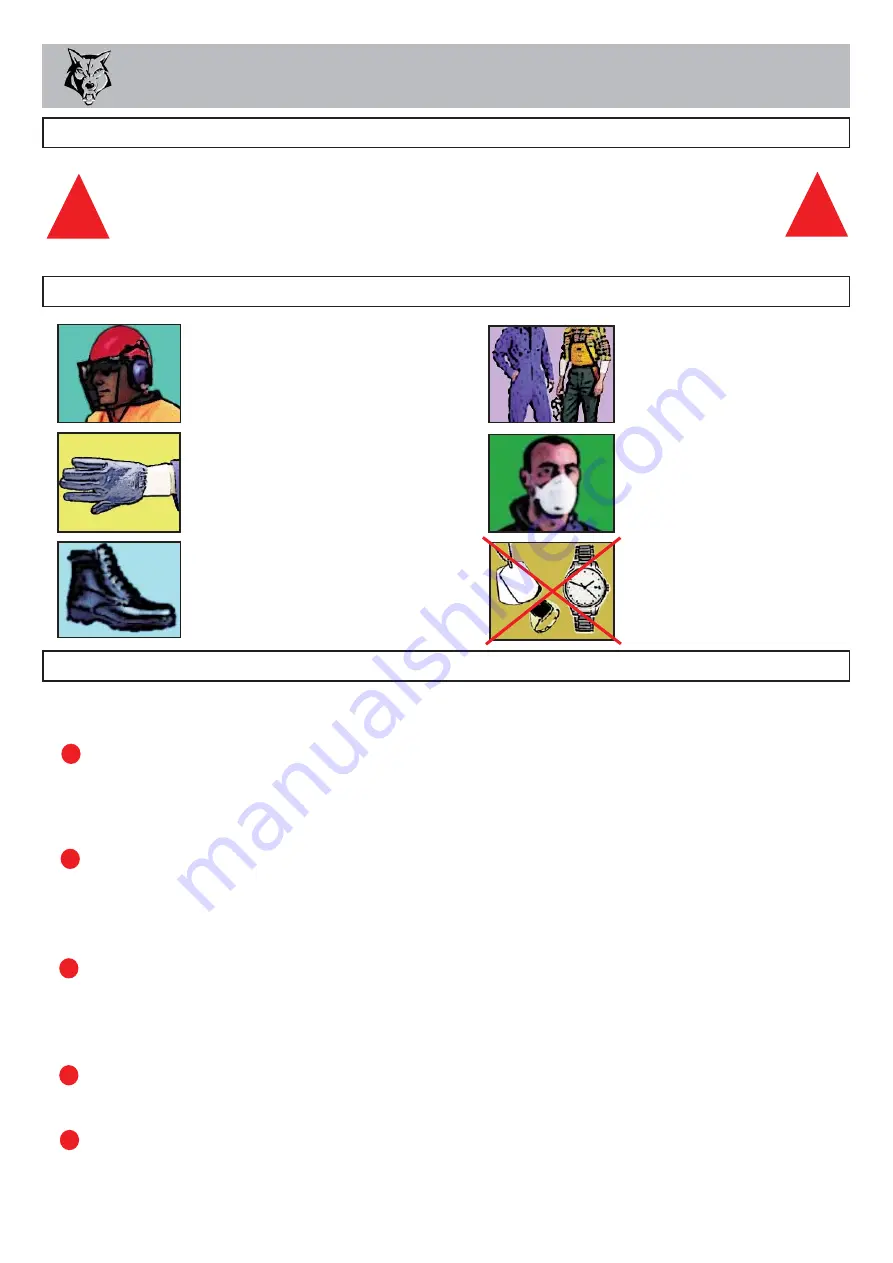
SAFE WORKING
5
BASIC WOODCHIPPING SAFETY
The operator should be aware of the following points:
MAINTAIN A SAFETY EXCLUSION ZONE
around the chipper of at least 10 metres for the
general public or employees without adequate protection. Use hazard tape to identify this
working area and keep it clear from debris build up. Chips should be ejected away from any
area the general public have access to.
HAZARDOUS MATERIAL
- Some species of trees and bushes are poisonous. The chipping
action can produce vapour, spray and dust that can irritate the skin. This may lead to
respiratory problems or even cause serious poisoning. Check the material to be chipped before
you start. Avoid confined spaces and use a facemask if necessary.
BE AWARE
when the chipper is processing material that is an awkward shape. The material
can move from side to side in the funnel with great force. If the material extends beyond the
funnel, the brash may push you to one side causing danger. Badly twisted brash should be
trimmed before being chipped to avoid thrashing in the feed funnel.
BE AWARE
that the chipper can eject chips out of the feed funnel with considerable force.
Always wear full head and face protection.
ALWAYS
work on the side of the machine furthest from any local danger, e.g. not road side.
WARNING
The chipper will feed material through on its own. To do this, it relies on
sharp blades on the chipper rotor. To keep the blades sharp, only feed the
machine with clean brushwood. DO NOT put muddy/dirty wood, roots,
potted plants, bricks, stones or metal into the chipper.
!
!
OPERATOR'S PERSONAL PROTECTIVE EQUIPMENT REQUIRED
Chainsaw safety helmet
fitted with mesh visor and
recommended ear defenders
to the appropriate
specifications.
Work gloves with
elasticated wrist.
Close fitting heavy-duty
non-snag clothing.
Face mask if
appropriate.
DO NOT
wear rings, bracelets,
watches, jewellery or any
other items that could be
caught in the material and
draw you into the chipper.
Steel toe cap safety boots.
Summary of Contents for TW PTO/100G
Page 17: ...CERTIFICATE OF CONFORMITY 16...