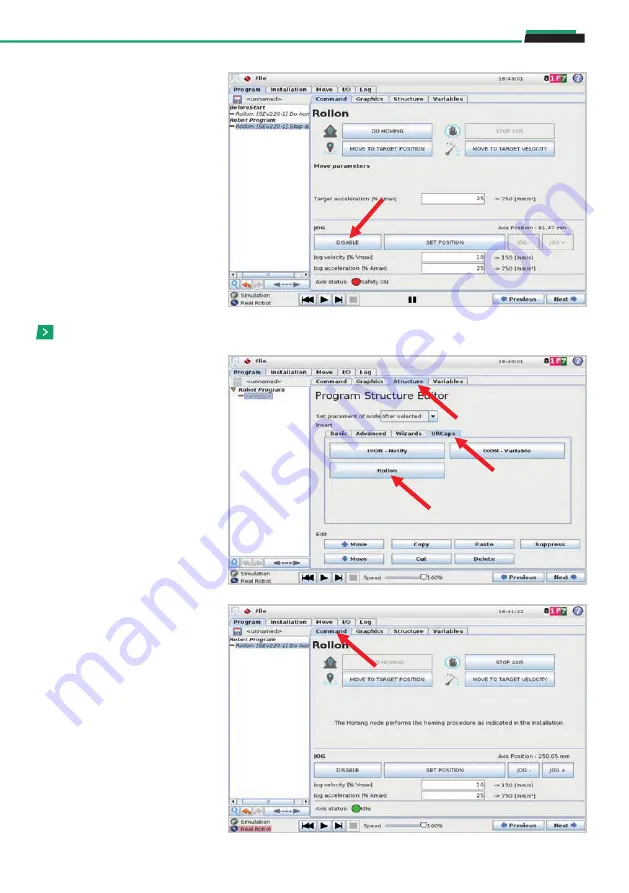
UM-35
Cobot Transfer Unit
Now move from “Structure” to “Com-
mand”, in the same menu, to set the
different instructions:
•
Do homing
•
Move to target position
•
Move to target velocity
•
Stop axis
To start programming, select “Program
robot” on the starting screen and then
upload your program or create a new one
clicking “Empty program”.
From the top menu, select “Structure”,
then “URCaps”, then “Rollon”.
Polyscope programming
In case you’ll need to move the car-
riage by hand, you’ll have to use the
“Disable” command (this operation is
strongly not suggested).
Fig. 71
Fig. 72
Fig. 73
Summary of Contents for ROLLON CTU 220-1I
Page 2: ......
Page 44: ...UM 42 Notes Notes...
Page 45: ...UM 43 Cobot Transfer Unit Notes...
Page 46: ...UM 44 Notes Notes...
Page 47: ......