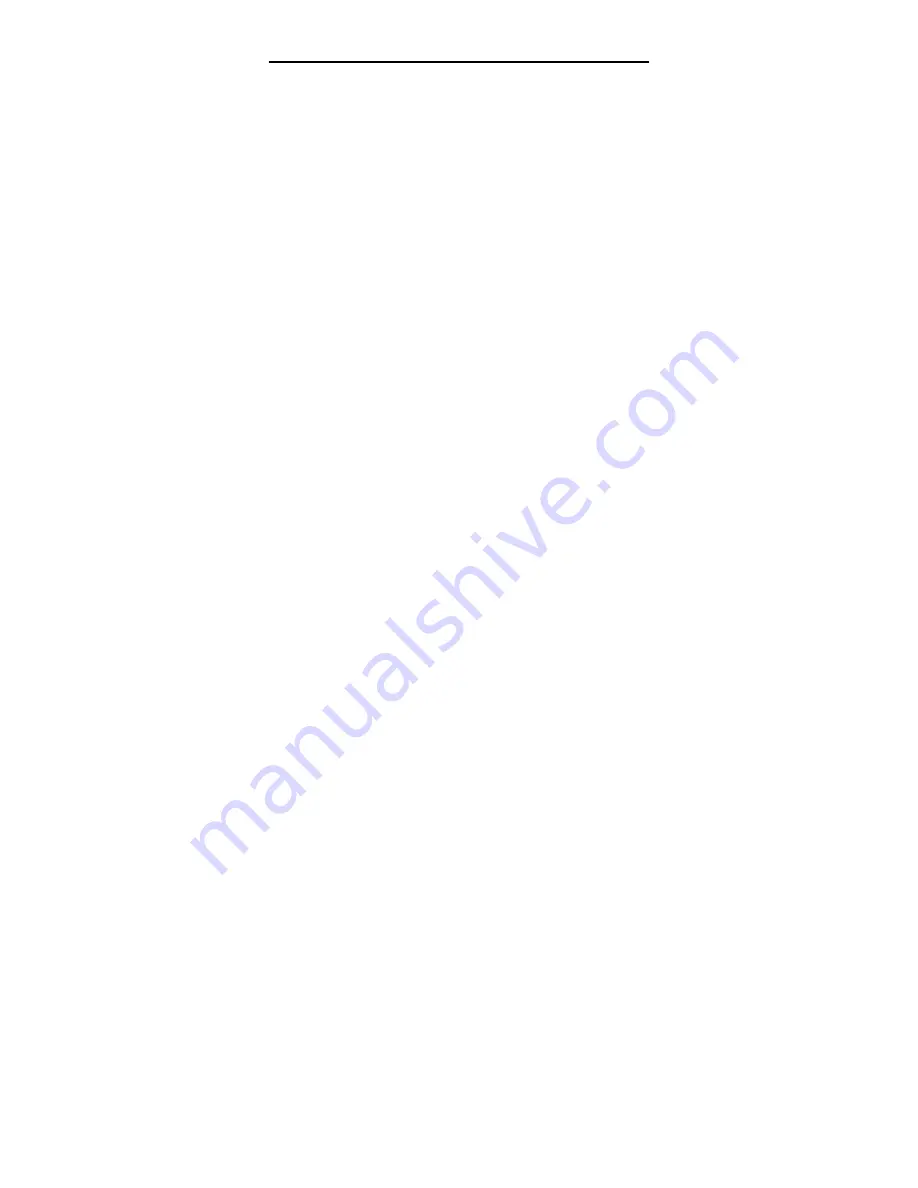
20
9-TROUBLESHOOTING
1. Motor does not run:
A.
Breaker or fuse blown.
B. Motor thermal overload tripped. Wait for overload to cool.
C.
Faulty wiring connections……Call electrician for service.
D.
Defective up button……Call electrician for service.
2. Motor runs but will not raise:
A.
A piece of trash is under the check valve. Push handle down and push the up
button at the same time. Hold for 10-15 seconds. This should flush the system.
B.
Check the clearance between the plunger valve of the lowering handle. There
should be 1/16”.
C. Remove the check valve cover and clean ball and seat.
D.
Oil level too low. Oil level should be just under the vent cap port when the lift is in
the lowered position.
3. Oil blows out breather of power unit:
A.
Oil reservoir overfilled.
B.
Lift lowered too quickly while under a heavy load.
4. Motor hums and will not run:
A.
Impeller fan cover is dented. Take off and straighten.
B.
Faulty wiring……Call electrician.
C.
Bad capacitor……Call electrician.
D.
Low voltage……Call electrician.
E.
Lift overloaded……Reduce weight.
5. Lift jerks going up and down: Air in hydraulic system. Raise lift all the way to top and
return to floor; Repeat 4-6 times. Do not let this overheat power unit.
6. Oil leaks:
A.
Check the power unit: If the power unit leaks hydraulic oil around the tank-
mounting flange, check the oil level in the tank. The level should be two inches
below the flange of the tank. Check with a screwdriver.
B.
Check the rod end of the cylinder: If the rod seal of the cylinder is out, rebuild or
replace the cylinder.
C.
Breather end of the cylinder: If the piston seal of the cylinder is out, rebuild or
replace the cylinder.
7.
Lift makes excessive noise:
A.
Leg of the lift is dry and requires grease.
B.
Cylinder pulley assembly or cable pulley assembly is not moving freely.
C.
May have excessive wear on pins or cylinder yoke.