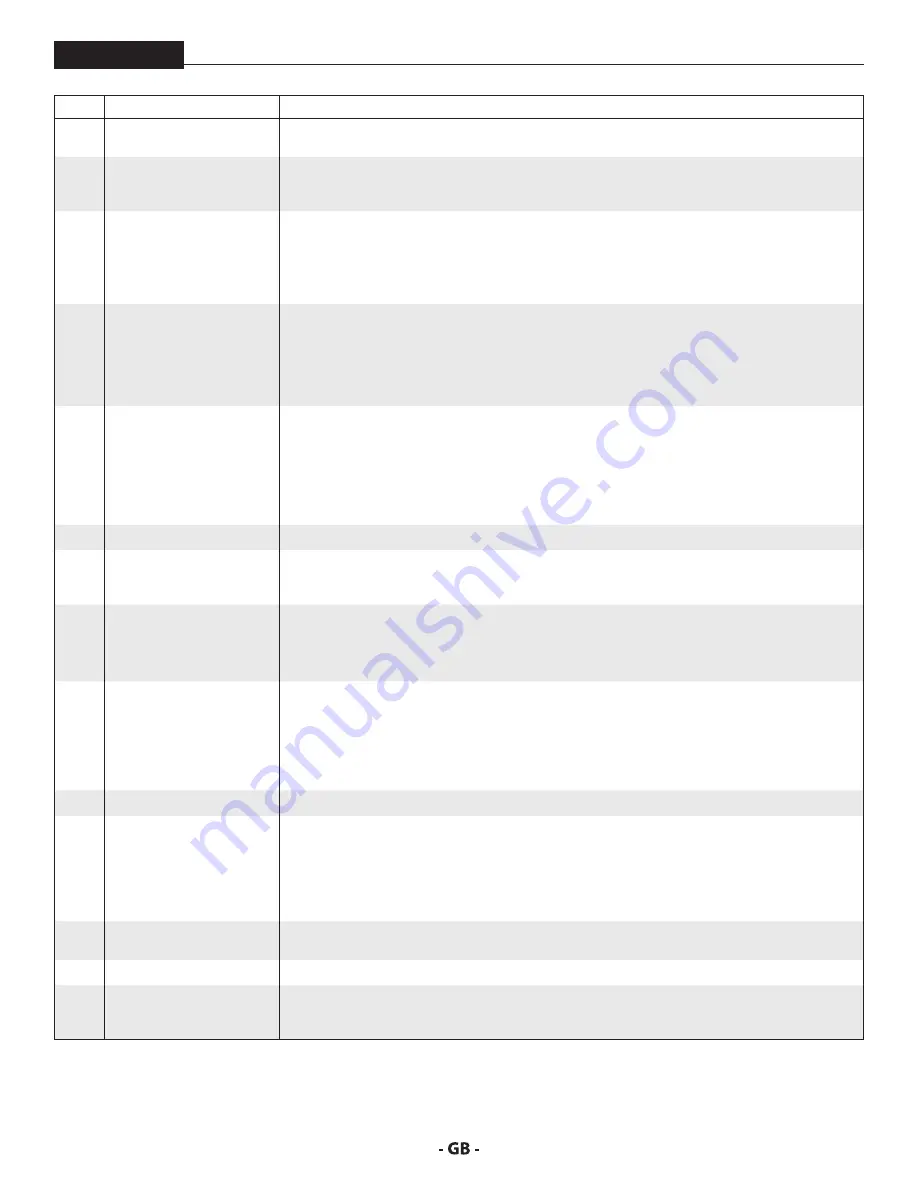
11
description of unit
ProMark
ITem DeScrIpTIoN
fuNcTIoN
1
DataLogger
The DataLogger tracks all of the performance information of the unit (see section 3.5 for a more detailed
description of the different DataLogger screens and options).
2
Gun / Bead activation button The gun / bead activation button activates the spray guns and bead dispenser. The spray guns and
bead dispenser(s) can be timed to trigger simultaneously (via DataLogger) or with a start/end delay
based on your spraying needs and spray gun / bead dispenser configuration.
3
High pressure filter
The high pressure filter filters out any impurities in the spray material as is passes on its way to the
mixing block.
a
Relief valve / bleed hose
This is the relief valve for the spray material side (A) of the system. When it is open (horizontal), spray
material will circulate from the material container through the siphon hose and back to the container
through the bleed hose. When it is closed, the system will build spraying pressure.
4
BPO (Benzoyl Peroxide) tank
The BPO tank provides the system with the catalyst necessary for spraying.
a
BPO pump
The BPO pump siphons the BPO chemical from the BPO tank to the mixing chamber or back to the BPO
pump, depending upon the position of the BPO valve (item 4b)
b
BPO valve
The BPO valve directs the flow of BPO. When closed (horizontal), BPO is directed to the mixing chamber.
When open (vertical), BPO is circulated back into the BPO tank.
5
Mixing block
The mixing block is where the spray material and the BPO are mixed prior to spraying. Upstream of the
mixing block are two shutoff valves. The red shutoff valve will cut off the flow of spray material to the
mixing block. The blue shutoff valve will cut off the flow of BPO to the mixing block.
a
Mixing hose
Once the material and BPO mixes in the mixing block, it travels down the mixing hose to the mixing
tube.
b
Static mixing tube
Allows the material to achieve the proper and a superior mix.
6
Spray gun(s)
The spray gun(s) deliver the spray material to the surface being sprayed.
7
SmartArm™
The SmartArm allows the user to adjust the height of the spray gun(s). The gun holder devices at the
end of the SmartArm allow the user to position each gun individually. The SmartArm can retract (pivot
up) for transport and storage.
8
Air compressor
The air compressor is powered by the gasoline engine and provides air pressure to the solvent flush
and the bead dispenser.
a
Air cylinder
The air cylinder provides the user with smooth controlled air delivery. Equipped with quick-disconnect
for auxiliary air tools (tools not included).
9
Solvent flush (located
behind the bead tank, see
inset)
The solvent flush tank provides the system with a quick flush whenever spraying activity stops. The
mixing hose, mixing block and the spray guns must be flushed whenever the system is not actively
spraying for a period of more than 2-3 minutes, otherwise the spray material / BPO mixture will harden
and set inside these components, rendering them inoperable.
a
Solvent flush valve
Provides solvent to the mixing block, mixing tube and spray guns when needed. This valve should
remain closed until the system is ready to be flushed.
10
Hydraulic motor
The hydraulic motor is powered by the hydraulic pump (10) which drives the spray material pump.
11
Pressurized bead dispenser
The pressurized bead dispenser contains the reflective beads used in marking.
a
Bead hose(s)
The bead hose(s) deliver the beads from the bead tank (10) to the bead dispenser(s) (10b).
b
Bead dispenser gun(s)
The bead dispenser gun(s) apply reflective beads to the material once it has been sprayed. The spray
guns and bead dispenser(s) can be timed to trigger simultaneously (via DataLogger) or independently
based on your spraying needs and spray gun / bead dispenser configuration.
12
Hydraulic pump
The hydraulic pump is powered by the gas engine (12) and provides hydraulic fluid to the hydraulic
motor (9)
13
Gasoline engine
The gasoline engine is the main power source for the ProMark system.
14
Front caster
The position of the front caster determines the driving direction of the system. It will remain locked in
a straight forward position until the caster trigger on the left handlebar is fully activated. The caster will
spin freely as long as the caster trigger remains activated.
Summary of Contents for 200
Page 12: ...12 description of unit ProMark 3 3 System controls FIGURE 3 1 5 4 8 2 3 6 7 9 10 11 12 ...
Page 45: ...45 troubleshooting ProMark ...
Page 56: ...56 Gerätebeschreibung ProMark 3 3 GERÄTESTEUERUNG abb 3 1 5 4 8 2 3 6 7 9 10 11 12 ...
Page 89: ...89 ProMark ...
Page 100: ...100 Description du matériel ProMark 3 3 COMMANDES DU SYSTÈME fig 3 1 5 4 8 2 3 6 7 9 10 11 12 ...
Page 133: ...133 ProMark ...