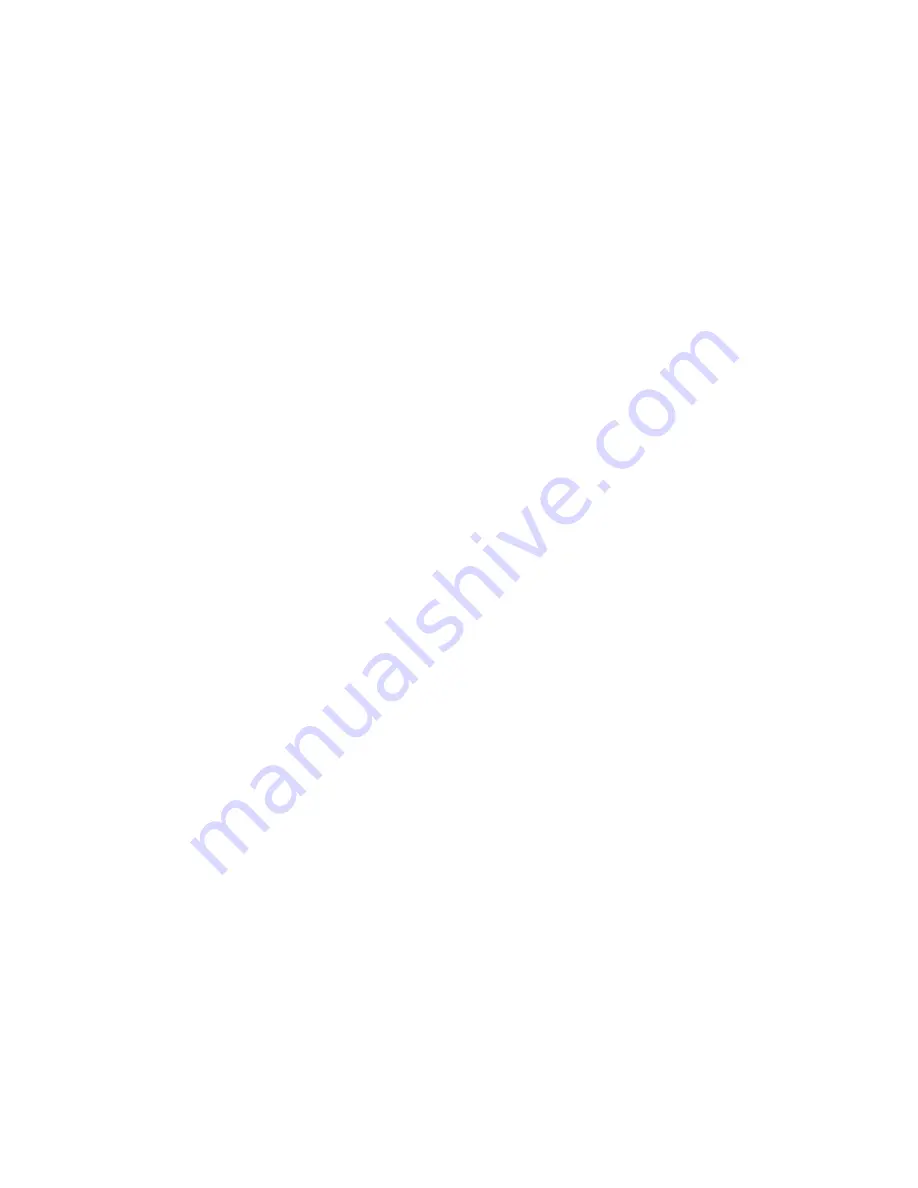
HYDRAULIC MOTOR & FLUID PUMP SERVICE
See Page 22 for maintenance and service instructions on the reci-
procating hydraulic motor and Page 26 for the fluid pump.
BASIC ENGINE MAINTENANCE
• For detailed engine maintenance and technical specifications
refer to the separate Honda engine manual.
• All service to the engine should be performed by an authorized
Honda Power Equipment dealer. To locate a dealer in your area,
look in the Yellow Pages of your telephone directory under
Gasoline Engines, Garden & Lawn Equipment & Supplies,
Lawnmowers, etc.
• The Honda engine is warranted exclusively by American Honda
Motor Co., Inc.
• Use a premium quality motor oil certified to meet or exceed U.S.
Automotive requirement SG.SF/CC.CD. SAE 10W30 is recom-
mended for general all temperature use. Other viscosities may be
required in other climates.
• Use only a (NGK) BP6ES or BPR6E spark plug. Gap the plug to
0.028 to 0.031 In. (0.7 to 0.8 mm) Always use a spark plug
wrench.
DAILY: Check engine oil level. Fill as necessary. Check gasoline
level. Fill as necessary.
WARNING: FOLLOW FUELING PROCEDURE ON PAGE 10
FIRST 20 HOURS: Change engine oil.
EVERY 100 HOURS: Change engine oil.
WEEKLY: Remove the air filter cover and clean the element. In
very dusty environments, check the filter daily. Replace the ele-
ment as needed. Replacement elements can be purchased from
your local Honda dealer.
ENGINE OPERATION AND SERVICE
1. Clean and oil air filter pad on gasoline engine every 25 hours or
once weekly. Do not permit the air intake screen around the fly
wheel of the gas engine to load up with paint or trash. Clean it reg-
ularly. The service life and efficiency of the gas engine model
depends upon keeping the gasoline engine running properly.
Change the oil in the engine every 100 hours. Failure to observe
this may result in engine overheating. Consult the engine manufac-
turer's service manual provided.
2. To conserve fuel, service life, and efficiency of the unit always
operate the gasoline engine at the lowest RPM at which it runs
smoothly without laboring and delivers the amount required for the
particular painting operation. Higher RPM does not produce higher
working pressure. The gasoline engine is connected to the
hydraulic pump by a pulley combination designed to produce full
paint delivery of 2.0 GPM at 3600 RPM.
3. The warranty on gasoline engines or electric motors is limited to
the original manufacturer.
IMPORTANT ELECTRIC MOTOR INFORMATION
WARNING: If electric motor overloads and stops running,
IMMEDIATELY turn the motor off and follow the Pressure
Relief Procedure on Page 10. Wait until the motor cools
(approximately 30 minutes). Then push in the bubble top,
manual reset button, turn the motor on and pressurize the
system.
For CSA approved units only:
The ON / OFF switch is also the RESET!
12
Summary of Contents for 449-700
Page 8: ...8 ...