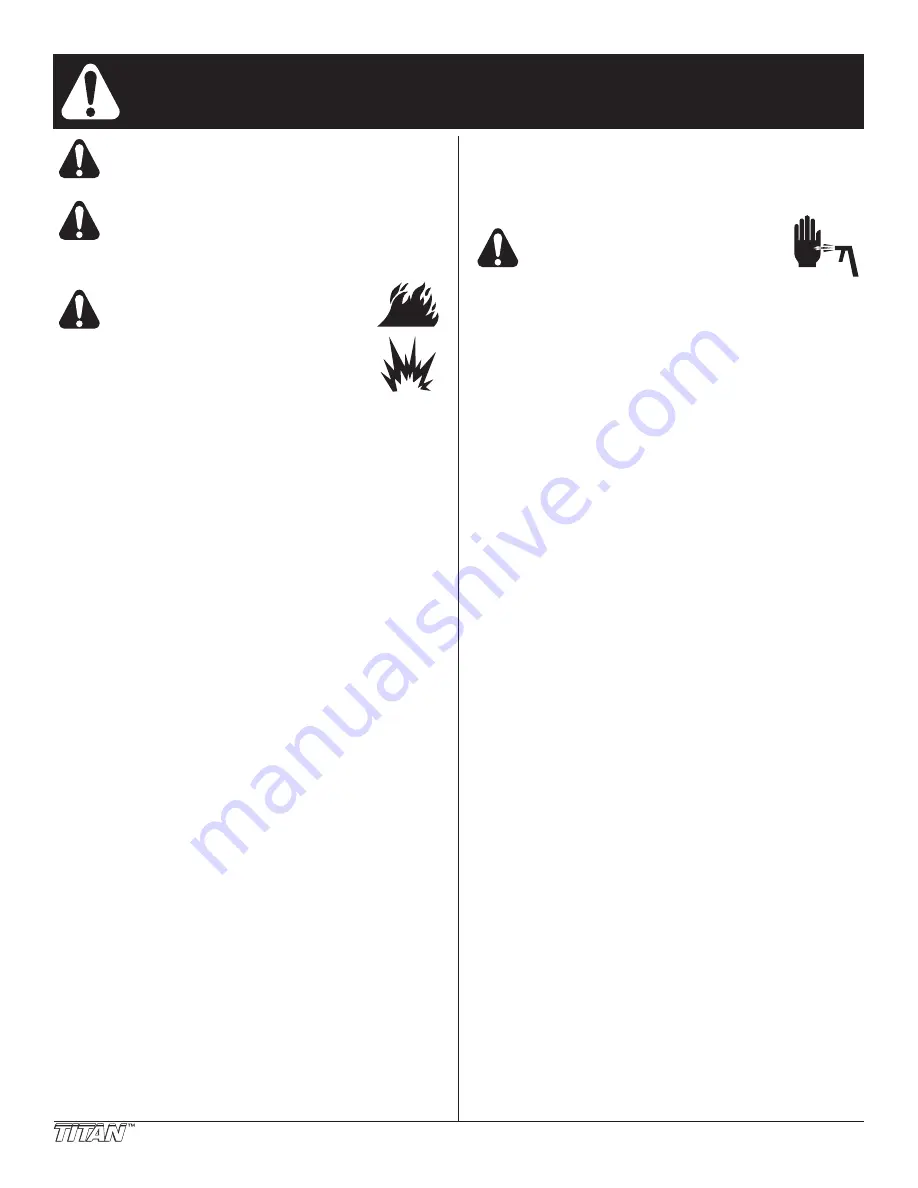
2
© Titan Tool Inc. All rights reserved.
Important Safety Information
·
Read all safety information before
operating the equipment. SavE ThESE INSTRucTIONS.
This symbol indicates a hazardous situation,
which, if not not avoided could result in death or
serious injury.
To reduce the risks of fire or explosion, electrical
shock, and the injury to persons, read and
understand all instructions included in this manual.
Be familiar with the controls and the proper usage
of the equipment.
WaRNING – To reduce the risk of fire or
explosion:
1. Do not spray flammable or combustible
materials near an open flame, pilot lights
or sources of ignition such as hot objects,
cigarettes, motors, electrical equipment and
electrical appliances. Avoid creating sparks
from connecting and disconnecting power cords.
2. For units intended for use with only water-based materials
— Do not spray or clean with flammable liquids. For use
with water-based liquids only.
3. For units intended for use with only water-based or mineral
spirit-type materials with a minimum flash point of 21ºC
(69.8ºF) — Do not spray or clean with liquids having a
flash point of less than 21ºC (69.8ºF). Flash point is the
temperature at which a fluid can produce enough vapor to
ignite.
4. Paint or solvent flowing through the equipment is able to
result in static electricity. Static electricity creates a risk of
fire or explosion in the presence of paint or solvent fumes.
All parts of the spray system, including the pump, hose
assembly, spray gun and objects in and around the spray
area shall be properly grounded to protect against static
discharge and sparks. Use only conductive or grounded
high-pressure airless paint sprayer hoses specified by the
manufacturer.
5. Verify that all containers and collection systems are
grounded to prevent static discharge.
6. Connect to a grounded outlet and use grounded extension
cords (electric models only). Do not use a 3 to 2 adapter.
7. Do not use a paint or solvent containing halogenated
hydrocarbons. Such as chlorine, bleach mildewcide,
methylene chloride and trichloroethane. They are not
compatible with aluminum. Contact the coating supplier
about compatibility of material with aluminum.
8. Keep spray area well ventilated. Keep a good supply of
fresh air moving through the area to keep the air within the
spray area free from accumulation of flammable vapors.
Keep pump assembly in well ventilated area. Do not spray
pump assembly.
9. Do not smoke in the spray area.
10. Do not operate light switches, engines, or similar spark
producing products in the spray area.
11. Keep area clean and free of paint or solvent containers,
rags, and other flammable materials.
12. Know the contents of the paint and solvents being
sprayed. Read all Material Safety Data Sheets (MSDS)
and container labels provided with the paints and solvents.
Follow the paint and solvent manufacture’s safety
instructions.
13. Place pump at least 25 feet (7.62 meters) from the
spray object in a well ventilated area (add more hose if
necessary). Flammable vapors are often heavier than
air. Floor area must be extremely well ventilated. The
pump contains arcing parts that emit sparks and can ignite
vapors.
14. Plastic can cause static sparks. Never hang plastic to
enclose spray area. Do not use plastic drop cloths when
spraying flammable material.
15. Fire extinguisher equipment shall be present and working.
WaRNING – To reduce the risk of skin
injection:
haZaRD:
Injection injury – a high pressure fluid stream produced by
this equipment can pierce the skin and underlying tissues,
leading to a serious injury and possible amputation. See a
physician immediately. DO NOT TREaT aN INJEcTION aS a
SIMPLE cuT.
1. Do not aim the gun at, or spray any person or animal.
2. Keep hands and other body parts away from the
discharge. For example, do not try to stop leaks with any
part of the body.
3. Always use the nozzle tip guard. Do not spray without the
nozzle tip guard in place.
4. Only use a nozzle tip specified by the manufacturer.
5. Use caution when cleaning and changing nozzle tips. In
the case where the nozzle tip clogs while spraying,
ALWAYS lock gun trigger, shut pump off, and release
all pressure before servicing, cleaning tip or guard, or
changing tip. Pressure will not be released by turning off
the motor. The PRIME/SPRAY valve or pressure bleed
valve must be turned to their appropriate positions to
relieve system pressure. Refer to PRESSURE RELIEF
PROCEDURE described in the pump manual.
6. Do not leave the unit energized or under pressure while
unattended. When the unit is not in use, turn off the
unit and relieve the pressure in accordance with the
manufacturer’s instructions.
7. High-pressure spray is able to inject toxins into the body
and cause serious bodily injury. In the event that injection
occurs, seek medical attention immediately.
8. Check hoses and parts for signs of damage, a leak can
inject material into the skin. Inspect hose before each use.
Replace any damaged hoses or parts.
9. This system is capable of producing 3300 PSI / 22.8
MPa. Only use replacement parts or accessories that
are specified by the manufacturer and that are rated a
minimum of 3300 PSI. This includes spray tips, nozzle
guards, guns, extensions, fittings, and hose.
10. Always engage the trigger lock when not spraying. Verify
the trigger lock is functioning properly.
11. Verify that all connections are secure before operating the
unit.
12. Know how to stop the unit and bleed pressure quickly. Be
thoroughly familiar with the controls. Pressure will not be
released by turning off the motor. The PRIME/SPRAY
valve or pressure bleed valve must be turned to their
appropriate positions to relieve system pressure. Refer
to PRESSURE RELIEF PROCEDURE described in the
pump manual.
13. Always remove the spray tip before flushing or cleaning
the system.