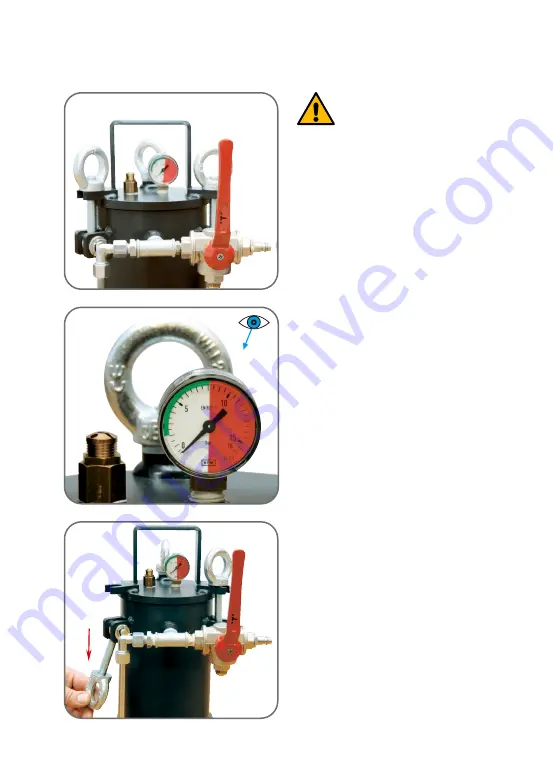
20
4.3.2
4.3.1
4.3.3
Attention!
Device may only be filled if
container is depressurised
and the air supply line has
been disconnected.
Fig. 4.3.1
3-way ball valve in „Relieve“ position
Fig. 4.3.2
Pressure gauge must not be indicating any
pressure
Fig. 4.3.3
Undo eye bolts and swivel out swivelling
screw fitting
4.3
Filling with blasting material
Summary of Contents for 81 29 2 208 034
Page 2: ...2...