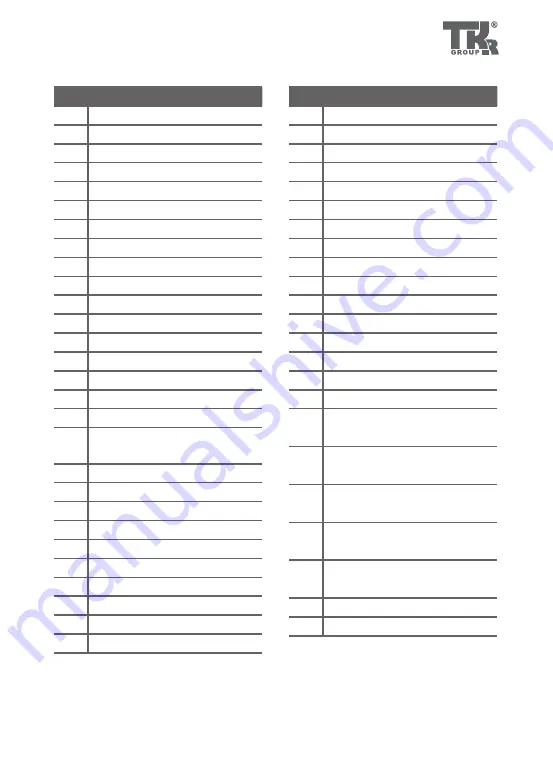
13
No. Title
1
Eye bolt
2
Annular nut
3
Pin
4
O-ring
5
Split pin
6
Handle
7
Control block
8
PVC hose Ø 14 mm
9
Handle
10
Relief valve
11
Pressure gauge Ø 50 mm
12
Kapsto plastic cover
13
Countersunk screw
14
Double nipple
15
T-piece
16
Exhaust valve
17
3-way ball valve
18
Straight threaded male
connector
19
Ermeto pipe 8x1
20
Bulkhead nipple
21
2-way ball valve
22
Threaded nozzle
23
Nozzle, straight
24
Straight insert nuts
25
Elbow fitting
26
Screw-in fitting
27
Straight male connector
28
Double nipple
No. Title
29
Elbow fitting connection
30
Disc
31
Hose, black Ø 6 mm
32
Hose, blue Ø 6 mm
33
Hose, transparent Ø 6 mm
34
Nozzle, bent
35
Granule container
36
Kapsto sealing screw
37
Press nipple
38
Protective hose
39
Follow manual
40
Observe the general information
41
Wear face mask
42
Wear ear protection
43
Wear gloves
44
Wear protective clothing
45
Warning! System under
pressure
46
Warning! General source of
danger
47
Warning against damage to
hearing
48
Warning against high levels of
noise
49
PVC washer for 1/4“
connection
50
Hose clamp
51
Type plate
Summary of Contents for PG 5-8
Page 21: ...4 3 10 4 3 9 4 3 1 1 21...