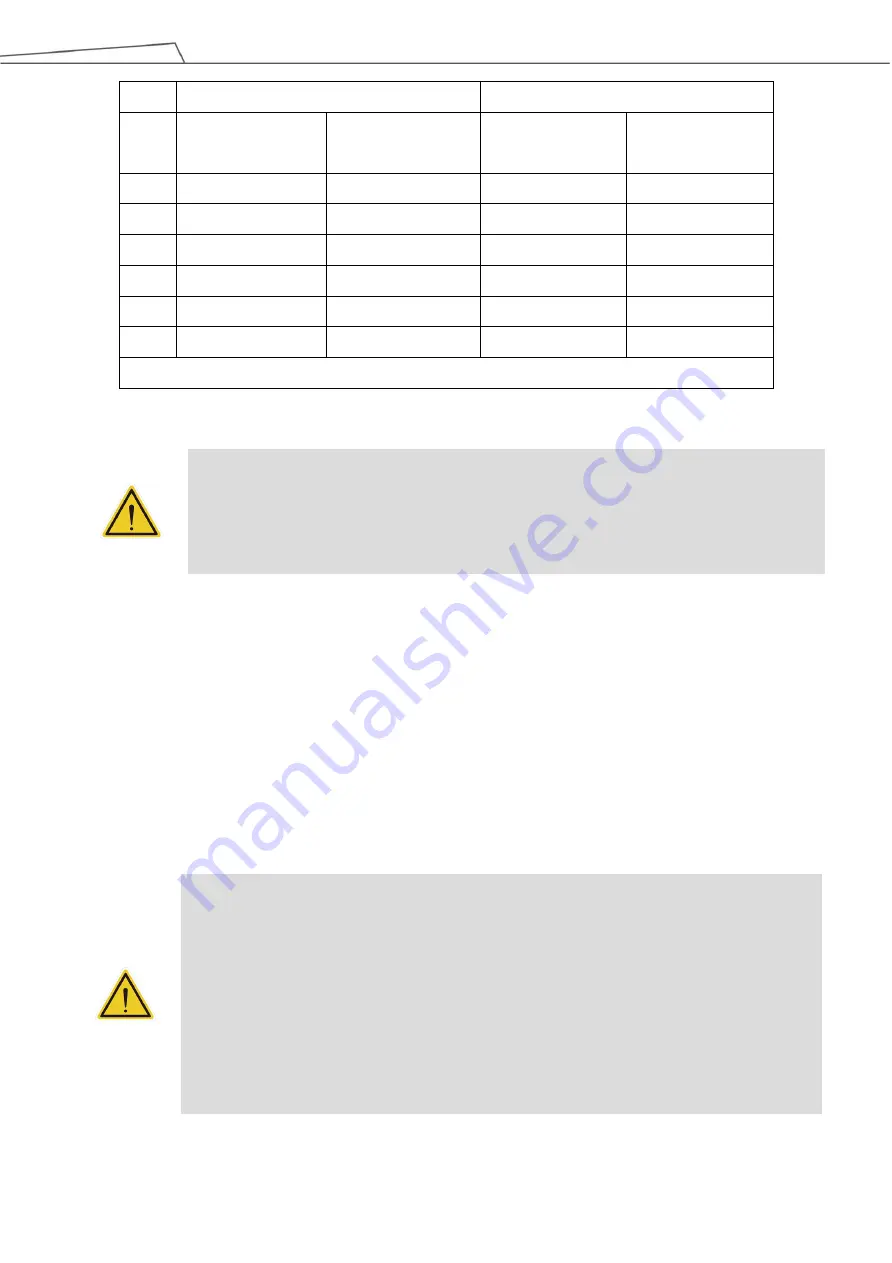
Medium & Heavy Payload Series-Hardware Installation Manual TM12/14 Series Hardware Version: 3.2
Document Version: 1.01
34
Model
TM12 Series
TM14 Series
Item
Rated torque
Limit for repeated
peak torque
Rated torque
Limit for repeated
peak torque
J1
311
353
311
353
J2
311
353
311
353
J3
118
157
118
157
J4
34
54
41
54
J5
34
54
41
54
J6
34
54
34
54
Unit: Nm
Table 4: Rated Torque and Limit for Repeated Peak Torque of Regular Payload Robot Series
WARNING:
Use the total weight of the end-effector and the payload to stay within the payload rating of
the robot. Ensure that the system never exceeds that maximum payload.
You should perform a full risk assessment that includes the end-effector and payload
samples, to ensure the safety of the entire system.
4.2.1.6
Robot Arm Installation
The robot can be secured to another surface with the use of (4) M10 screws and washers. The
mounting pattern is shown below. The recommended tightening torque is 40 Nm.
Optional - Two openings for 6 mm position pins are provided for more secure position mounting.
Ensure the strength of the mounting surface and its surround area before installations for upside down
mounting and side mounting such as on the ceiling or the wall. Wherever the installation takes place,
the robot setting remains equivalent.
DANGER:
1.
The TM Robot must be securely and tightly screwed down before use. The strength of the
mounting surface must be sufficient.
When operating at high speed, the robot can generate up to 350 N reaction force to the
mounting surface and screws. In order to avoid decreased performance caused by robot
slip or vibration, the recommended mounting surface should be a steel plate at least 20 mm
thick, its flatness should be 0.1 mm or less, its surface roughness should be Rz25 or less.
The recommended screw should be M10 x L30 mm, at least 8.8 strength.
2.
Do not immerse TM Robot in water. Installation in water or a humid environment will
permanently damage the robot.