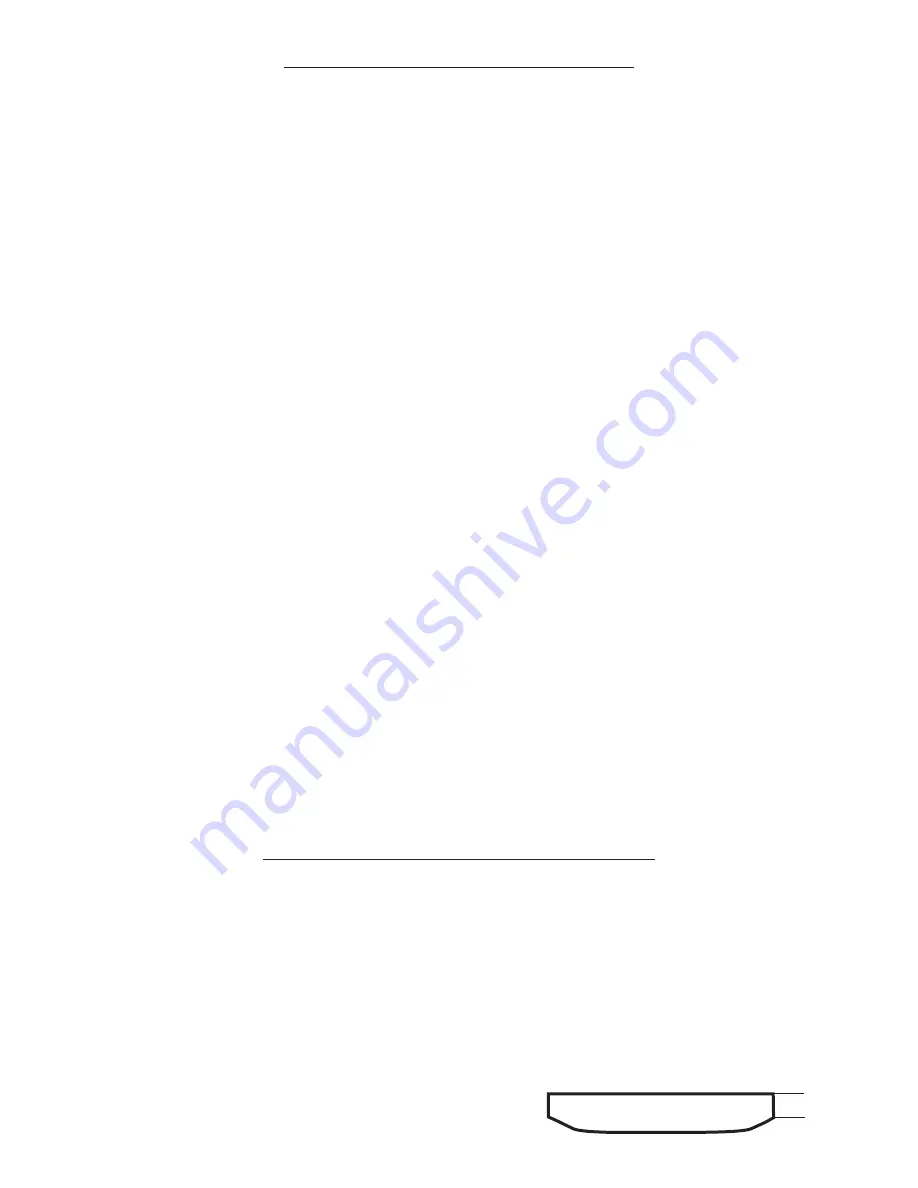
Ensure Proper Pressure, Filtration & Lubrication
Properly lubricated pneumatic tools work better, last longer between maintenance intervals and are safer in
general use. The maintenance costs are reduced dramatically when a little time is taken to regularly lubricate
the tools. There are several ways to ensure proper lubrication.
1) Filters, Regulators & Lubricators
These devices should be installed in the air system at each grinding station and inspected regularly to ensure
proper operation. Each device in this set performs a vital task that greatly affects the performance of the tool
and overall longevity of the component parts.
Filters
A filter is a device used to trap/contain particulate and liquid contaminants in the compressed air system. They
generally have a cartridge or screen that requires cleaning or replacement regularly. Without this maintenance,
the filtering device can become clogged and reduce the flow of air to the tool. A loss in performance can result.
Regulators
A regulator adjusts the operating pressure supplied to the tool. This device generally is used with a pressure
gauge that will indicate the current pressure setting. All Top Cat ® pneumatic tools are designed to operate at
90 PSI (6.2 bar) while the tool is running. The tool should never be run if the pressure should exceed 90 PSI
(6.2 bar).
Lubricators
Lubricators are devices that induce a controlled amount of oil into the air supply for pneumatically driven tools.
They generally contain a reservoir that one must keep filled with oil. A light grade oil such as Mobil DTE light
or equivalent is recommended. There is a variable setting on the lubricator that will determine the amount
of oil induced into the air supply. It is important to inspect both the setting and amount of oil in the lubricator
regularly to determine proper functioning of the device. The lack of oil in the air system will greatly reduce the
performance and longevity of the pneumatically driven tool.
2) Direct injection of oil into the tool
A simple and easy way to ensure proper lubrication is to inject the oil directly into the tool air inlet. This should
be performed prior to storage of the tool. To perform this task one must have a small container of the proper
lubricating oil.
● Disconnect the tool from the air supply at the air coupling.
● Place a few drops of oil from the container into the air inlet of the tool directly.
● Reconnect the tool to the air supply.
● Direct the exhaust of the tool away from any bystanders or cover the exhaust with a shop rag.
● Run the tool until the oil has completely passed through the unit.
The best lubrication techniques include both methods.
What Conditions Indicate the Need for Maintenance?.
Pneumatic tools will exhibit several distinct signs that maintenance is required. Higher costs can be avoided
if maintenance is performed when the first signs are evident. The following list details conditions that may
indicate the necessity for service.
1) With the tool disconnected from the air supply, grasp the spindle and spin in the direction of operation. The
spindle should spin freely with no resistance.
2) With the tool disconnected from the air supply, grasp the spindle by hand. Attempt to move the spindle from
side to side and back and forth. Excess play can be a sign that service is required.
3) A reduction in power may indicate the necessity for maintenance.
4) Should the tool not maintain a uniform operating speed, servicing may be required.
The Common Wear Items:
The Blades (700-13) are subjected to contaminants within the
air system. It is common for grit or sand to enter the tool through
.
347
↕
661-45
or
661-52
661-48