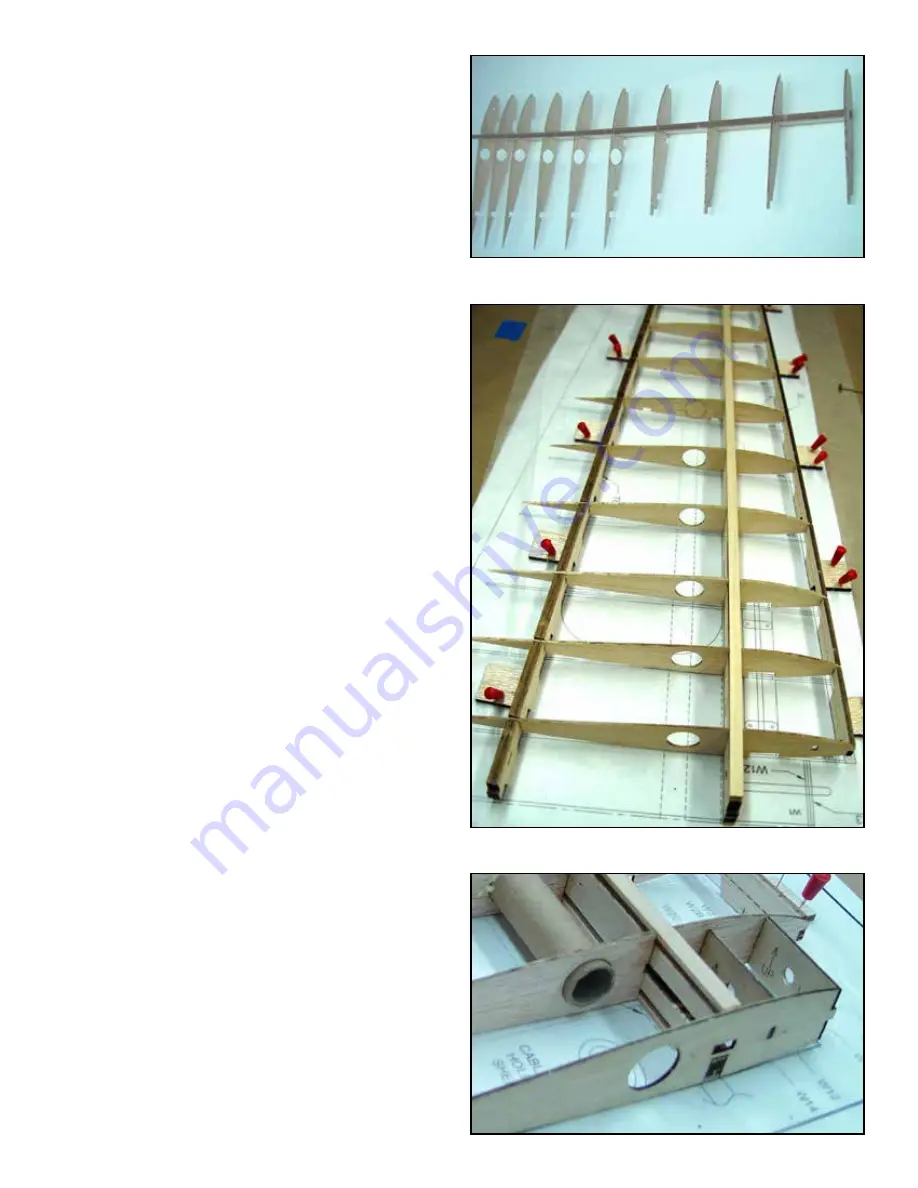
c
18
c
17
c
16
c
15
c
14
c
13
c
12
c
11
c
10
c
9
c
8
c
7
Slide ribs W2 through W10 into their appro-
priate slots in the spar. Make insure that the
bottom of the top notch is flush with the top
of the spar.
Install and glue the Top Spar Doubler (SD
TOP) on the top of the spar at the root end.
Cut a piece of 3/32” x 1/4” x 36” spruce
stick to the exact length of the spar. Glue
this piece to the top of the spar. You should
now have ribs W2 through W9 captive in the
spar.
After step #9 you will have ribs W2 through W9 captive in
the spar assembly
Remove the dash cut section of material at
the root end of the spar assembly.
Place the leading edge tab of each rib into
the appropriate slot in FLE. DO NOR GLUE.
Slide the trailing edge (TE) under the aft
section of the ribs and insert each rib into
the appropriate slot in TE, Do not force any-
thing, when it is correctly lined up it will drop
onto place.
Align the alignment line in the TE standoff
with the alignment line on the plans and se-
cure it to the building board with a pinning
tab tack glued to the standoff. Like you did
with FLE. Continue down TE and secure ev-
ery other tab in the same manner. Insure that
each standoff is flat on the building board.
You can now apply glue to all the joints.
Start with the leading edge, then the trailing
edge. As you apply glue insure each rib is
bottomed tin the slot.
Install and glue the root rib (W1) and the tip
rib (W10).
Install and glue W14 between W1 and W2.
Install and glue W12 between W1 and W2.
Note that the slot in W2 is oversize. Install
W12 to the back of the slot. W13 will be in-
stalled in the front of that slot in a later step.
Cut a 11-7/8” length of cable tunnel tubing
and install in between W2 and W7. Glue it
at each rib.
Before applying glue to each joint, insure that each rib is
bottomed in the slot.
RIGHT: The photo illustrates all the work done in steps 15
through 18. Note the dash cut material in the spar has been
removed (Step 10). The hole in W1 is only used to install the
cable tunnel tube which terminates at W2 and W7.
3