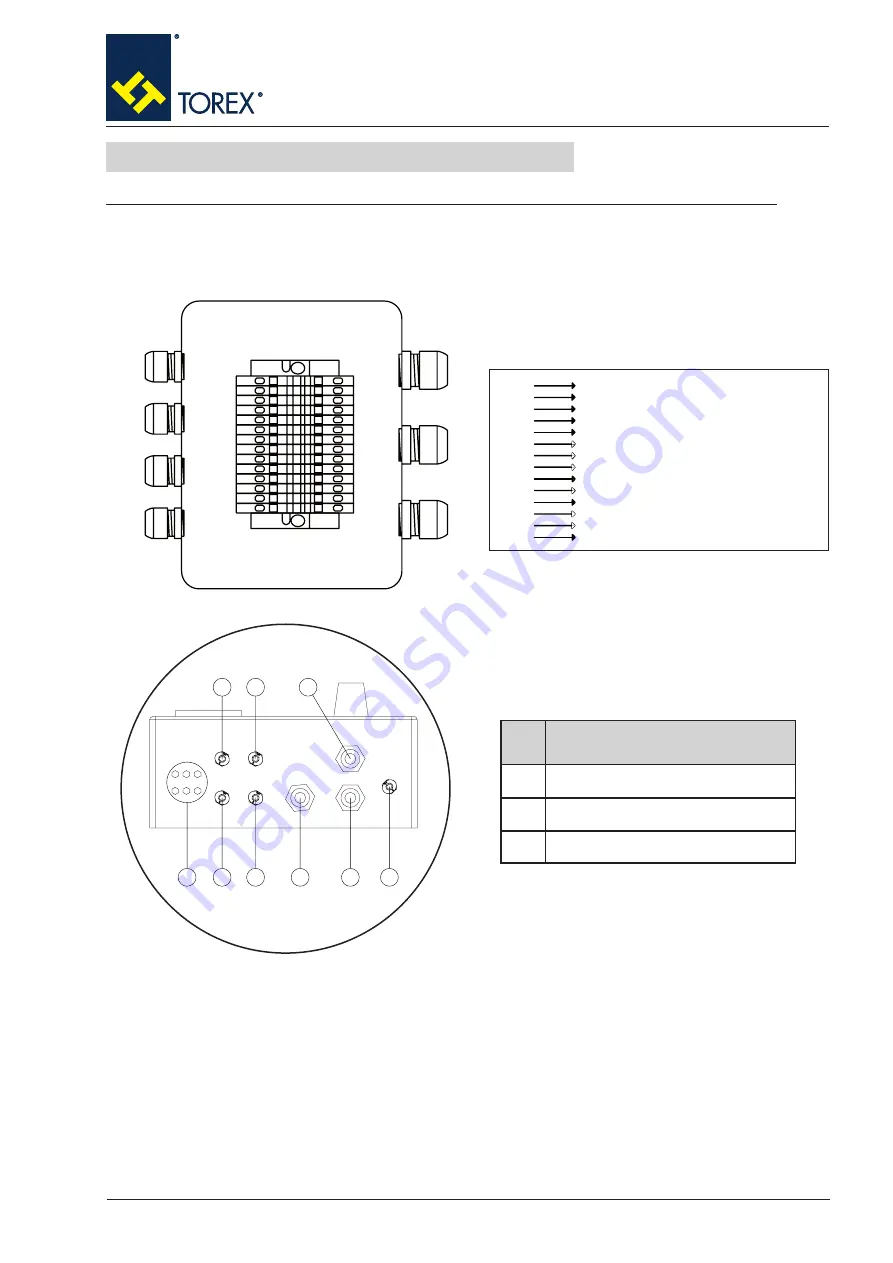
2 - Operation and maintenance
31
TO320 M - EN - Ed. 04.09
Electrical connections
12.6.5
Before carrying out any operation on the machine, make sure it is in safety condition!
The wiring diagram for connecting the VDC utilities is shown below.
After making the electrical connections, simulate a work cycle.
This simulation must be done without the guard for checking the movements of the lever mechanisms
and the signals. This operation must be performed solely by suitably trained personnel authorized for
the use and maintenance of the VDC only after having read this Manual.
Check to make sure the limit switches on the cylinders are adjusted correctly. The limit switch must
send a signal the moment the cylinder is in the maxium extended and retracted position.
Check to make sure the openings of the flaps correspond to the respective power supplies of the
coils.
Check to make sure there are no air leaks in the various connections.
Check to make sure, when the flap is open, the cylinder is completely extended and that there is a
gap of at least 5mm between the lever and the stud bolt.
0
0
08
06
15
16
14
11
24
24
24
24
17
24
5
6
8
7
3
1
9
2
4
No.
Description
5
Pressure switch signal output
6
Upper cylinder solenoid valve
7
Lower cylinder solenoid valve
08
0
06
0
11
14
15
16
17
24
24
24
24
24
DESCRIPTION OF CONNECTIONS
SOLENOID VALVE COMMON WIRE
SOLENOID VALVE COMMON WIRE
UPPER CYL. SOLENOID VALVE
LOWER CYL. SOLENOID VALVE
PRESSURE SWITCH
OPEN FLAP UPP. CYL. LIMIT SWITCH
CLOSED FLAP UPP. CYL. LIMIT SWITCH
OPEN FLAP LOW. CYL. LIMIT SWITCH
CLOSED FLAP LOW. CYL. LIMIT SWITCH
PRESSURE SWITCH COMMON WIRE
LIMIT SWITCH COMMON WIRE
LIMIT SWITCH COMMON WIRE
LIMIT SWITCH COMMON WIRE
LIMIT SWITCH COMMON WIRE
Summary of Contents for VDC 200
Page 1: ...VDC Double dump valve EN TO320 EN Ed 04 09 ...
Page 7: ...TECHNICAL CATALOGUE TO320 T EN Ed 04 09 1 VDC Double dump valve EN ...
Page 24: ......
Page 25: ...VDC Double dump valve EN OPERATION AND MAINTENANCE TO320 M EN Ed 04 09 2 ...
Page 66: ......
Page 67: ...SPARE PARTS CATALOGUE VDC Double dump valve EN TO320 R EN Ed 04 09 3 ...
Page 76: ...10 3 Spare Parts Catalogue TO320 R EN Ed 04 09 Plate 2 Counterweight 2 1 2 4 2 3 5 ...