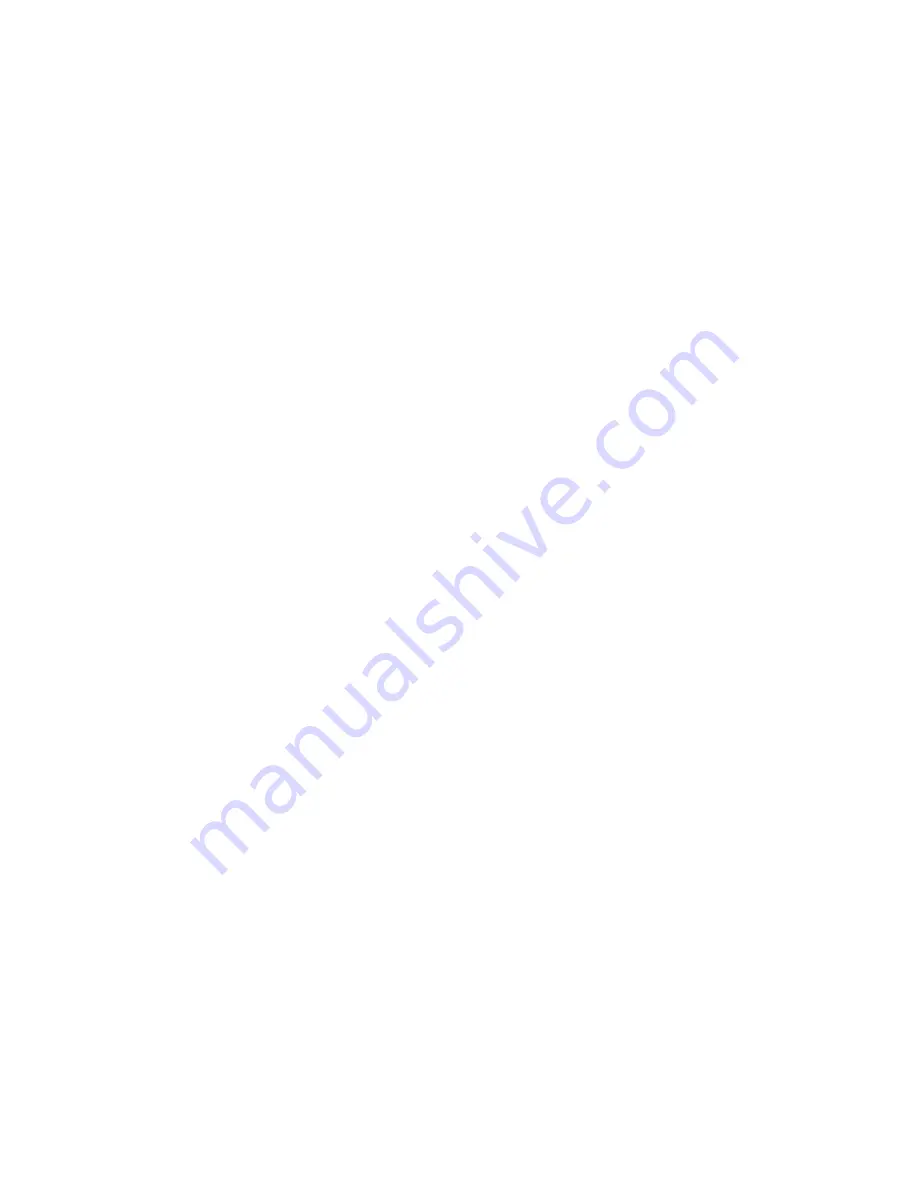
4
Warranty
2- Post Light Duty Automotive Lift Warranty Coverage
1 Year Structural Warranty (Materials and workmanship must be free of defects.)
1 Year Parts Coverage (All other assembly components and parts, such as; cables, sheaves, hydraulic
components, power units, chains, valves, switches, hoses, air cylinders, fittings, misc…)
1 year service coverage on labor with return of parts
The warranty does not extend to.:
Lifting pads and extensions.
Irregularities caused by normal wear, abuse, misusage, shipping damage, improper installation, voltage or
terms of required maintenance. Damages resulting from purchaser’s neglect or failure to operate products
according to instructions provided in the owner’s manual (s) and/or other accompanying instructions
supplied; Normal attrition items or normally serviced items required to maintain the product in a safe
operating condition; Components damaged in shipment of product. Other items not listed but may be
considered general attrition items. Damage caused by rain, excessive humidity, corrosive environments or other
contaminants.
These warranties do not extend to any cosmetic defect not interfering with equipment functionality or any
Incidental, indirect, or consequential loss, damage, or expense that may result from any defect, failure, or
malfunction of a product delay in performance of the warranty.
Manufacturer always recommends that lift be professionally installed.
Warranty applies to items only.
Always follow vehicle manufacturers vehicle lifting procedures. Failure to follow vehicle manufacturers lifting
procedures could cause injury and/or death. If vehicle manufacturers vehicle lifting procedures are not
followed, products will not be warranted.
The manufacturer reserves the right to change specifications, designs or add improvements to its product line
without incurring any obligation to make such changes to products sold previously.
The Manufacturer will not undertake any responsibilities for any damage caused due to incorrect installation or
usage of the equipment, whether indirectly or indirectly.
Keep a record of your lift here. Record the lift and power unit information.
This information is required when calling for parts or warranty issues.
Model # _____________________
Lift Serial # _____________________
Date of Mfg. _____________________
Power Unit Model # _____________________
Power Unit Date Of Mfg. _____________________
Power Unit Serial # _____________________
Summary of Contents for QJY240C
Page 9: ...9...
Page 23: ...23 Fig 12 Fig 12...
Page 32: ...34 Parts Diagram...
Page 33: ...35 Parts List...
Page 34: ...36 COMPANY INFO BACK PAGE...