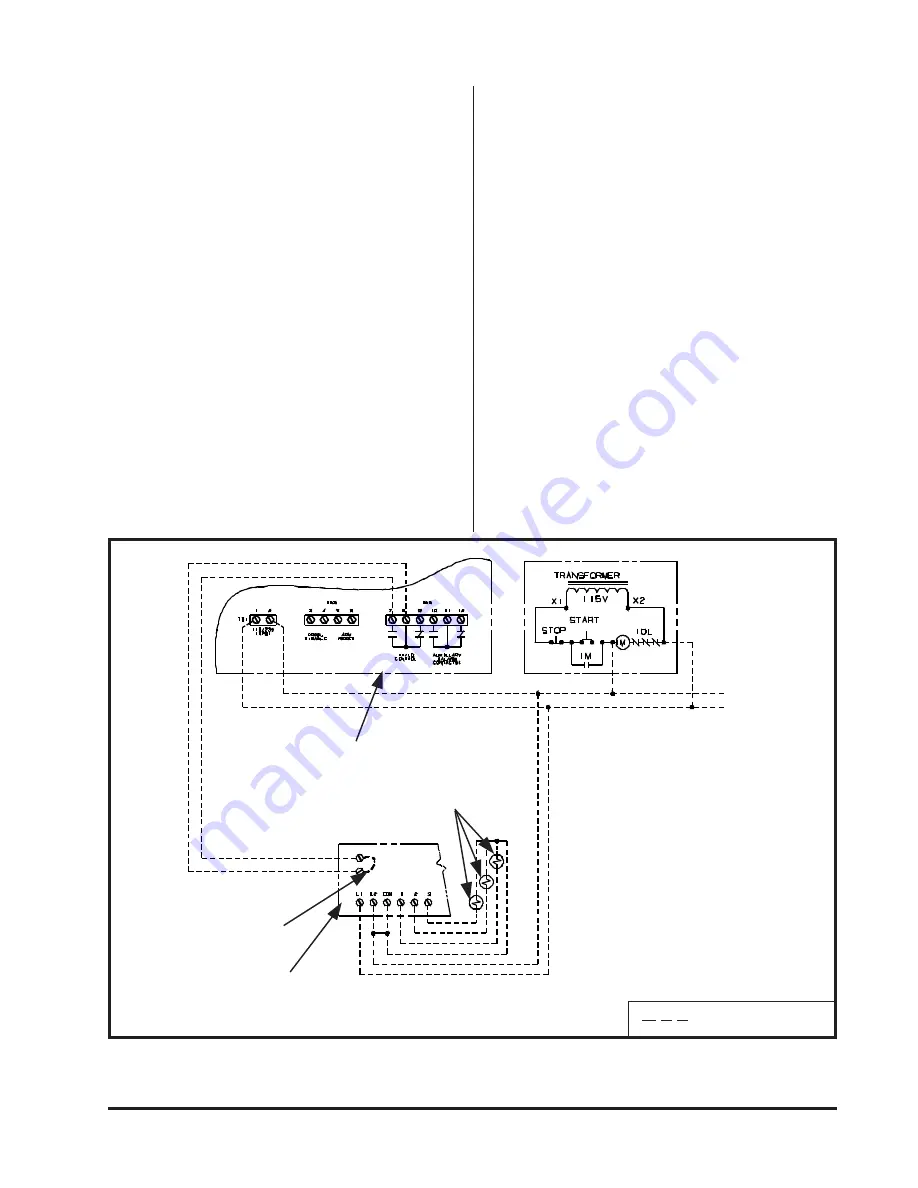
Donaldson Company, Inc. © 1995
37
2.6.6 Photohelic Gage (See Figure 34
Photohelic Gage & Figure 35 Remote-
Mounted Photohelic Gage)
Some units are supplied with an optional
Photohelic gage where the gage, pressure taps,
and tubing have been preinstalled in our factory.
Proper wiring of the gage is necessary.
1. Remove the four (4)#6-32 x 5/16 long
screws and plastic enclosure on the back of
the Photohelic gage and set aside.
2. Add the two jumper wires (not supplied by
Torit) and wire the gage using 3/4" conduit
opening, as shown in Figure 36 Photohelic
Gage Wiring Diagram.
3. Reassemble the plastic enclosure and fasten
securely, using the #6-32 x 5/16" long
screws previously removed.
4. Zero and maintain the Photohelic gage per
the operating and maintenance instructions
provided by the manufacturer of the
Photohelic gage.
For remote-mounted gages, the plastic tubing
will determine the distance away from the unit
that the gage can be located. If more tubing is
required, please contact your local Torit
representative.
Mount the remote gages as shown in Figure 35
Remote-Mounted Photohelic Gage. Make the
connections as shown in Figure 32 Photohelic
Gage. The high pressure port is connected to the
dirty air plenum. The low pressure port is
connected to the clean air plenum. The high and
low pressure connections are located in the
electrical compartment. Use bulkhead fittings
and mount them through the cabinet to the
electrical compartment. Wire the Photohelic
gage per the instructions previously stated in this
section.
Figure 36
Photohelic Gage Wiring Diagram
Wiring by others
*For use with Solid State Timer only
Timer Board
Solenoid Valves
∆
P Control
PRESSURE
SWITCH
110VAC
NEUT
From main
control panel
Remove factory installed
jumper on timer labeled
(Pressure Switch)