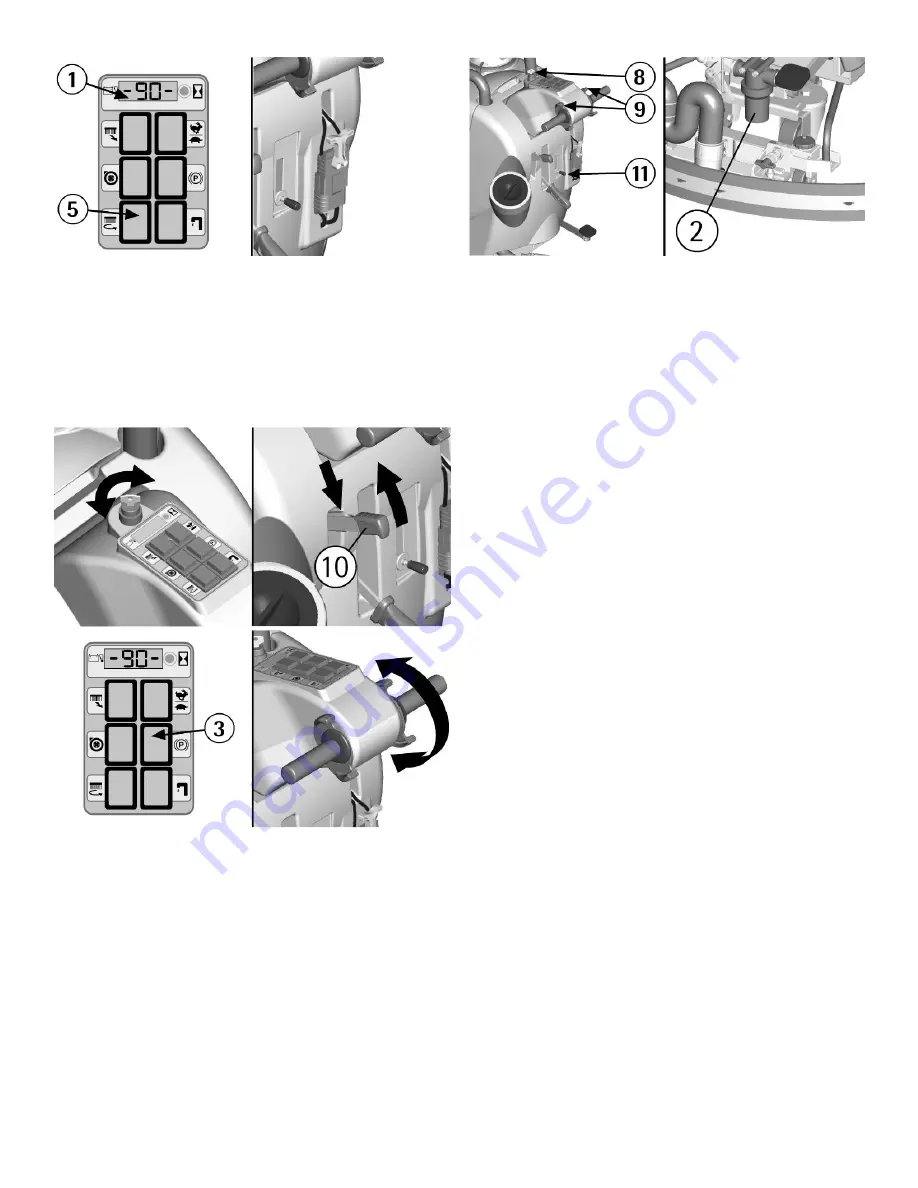
23
THE TRACTION MOTOR DOES NOT WORK
1. Switch off and on again the machine.
2. Release the brake (10) until the signal lamp (3)
comes off.
3. Act upon the levers drive control.
If the problem persists, please contact the autho-
rized technical assistance.
INSUFFICIENT WATER ON THE BASE
1. Check that the solution valve lever (11) is
open.
2. Check the level of the liquid in the solution
tank.
3. Check that the solution filter (2) is clean.
4. The machine is equipped with solenoid valve,
therefore act upon the levers drive control (9).
If the problem persists, please contact the autho-
rized technical assistance.
THE MACHINE DOES NOT CLEAN PROPERLY
1. Verify the presence of the PAD.
2. Verify that the PAD is intact.
3. To replace the pad, see under “PAD DISAS-
SEMBLY” and “PAD ASSEMBLY”.
4. The solution detergent is insufficient: open
more the solution valve.
5. Check that the liquid detergent is in the recom-
mended percentage.
6. Increase the base pressure (see at paragraph
"ADJUSTMENT OF THE BASE PRESSURE").
Contact the authorized technical assistance for
advice.
THE SQUEEGEE DOES NOT DRY PERFECTLY
1. Check that the squeegee rubbers are clean.
2. Check the adjustment of the height and the in-
clination of the squeegee. (see section “ADJUST-
MENT OF THE SQUEEGEE” in “BEFORE USE”).
3. Check that the suction hose is correctly insert-
ed in the proper seat on the recovery tank.
4. Clean the suction filter.
5. Replace the rubbers if worn out.
6. Check that the suction motor switch is on.
EXCESSIVE FOAM PRODUCTION
Check that low foam detergent has been used.
Eventually add small quantities of anti foam liquid
into the recovery tank.
Please be aware that a bigger quantity of foam is
produced when the floor is not very dirty. In this
case please dilute detergent solution.
https://harrissupplyind.com - To Order Parts Call 608-268-8080