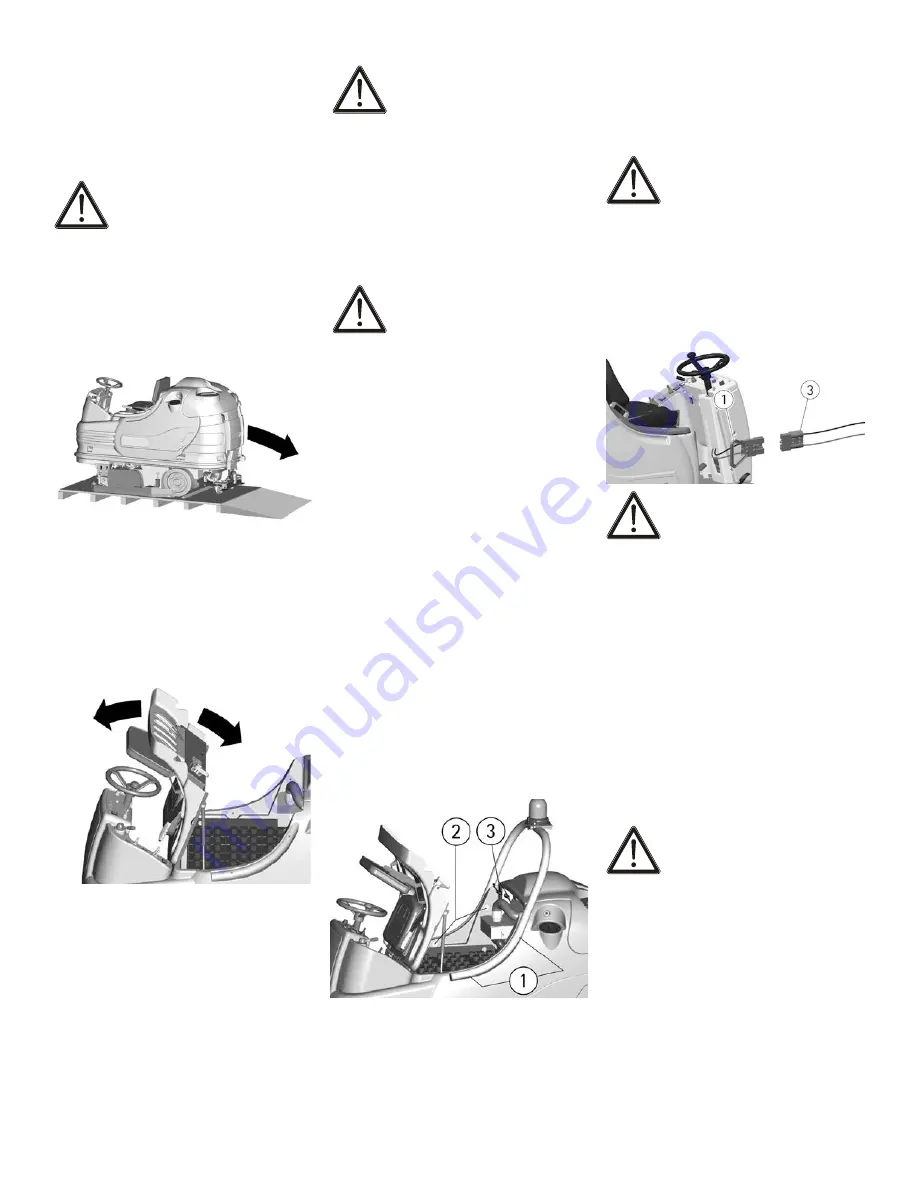
10
BEFORE USE
HANDLING OF THE PACKED MACHINE
The machine is supplied with suitable
packing for fork lift truck handling.
The total weight is 1587 lbs.720 kg.
Packing dimensions:
Base: 84” x 50” 213 cm x 125 cm
Height: 65” 165 cm
ATTENTION:
Do not place any packings on top.
UNPACKING OF THE MACHINE
1. Remove the external packing.
2. Move the machine backwards, as
indicated in the figure, avoiding heavy
contacts to mechanical parts.
3. Keep the pallet for further transport.
ACCESS TO THE BATTERY COMPART-
MENT
1. Bring the machine on a level surface.
2. Rotate the seat platform forward up to
the blocking of the support arm.
3. When completed, close the battery com-
partment, after releaseing the support arn,
reposition the seat platform.
BATTERY INSTALLATION AND SETTING
OF THE BATTERY TYPE
The machine is equipped either with bat-
teries in serial connection or elements of
DIN-type assembled together and connect-
ed in series for a total of 36 Volt, placed
in its appropriate compartment under the
seat platform and must be handled using
suitable lifting equipment (due to weight,
considering the type of batteries chosen,
and coupling system).
The batteries must be in accordance with
CEI 21-5 Norms.
ATTENTION:
The machine and its battery check card
are factory set for the use of traditional
lead batteries.
CHECK THE SETTING OF THE CHECK
CARD
(see under paragraph "
BATTER-
IES CHARGE LEVEL INDICATOR"
).
In case of GEL batteries installation, it is
necessary to set the battery check card.
Please contact the authorized technical
assistance.
ATTENTION:
Strictly follow manufacturer/distributor
indications for the maintenance and re-
charge of the batteries. All installation and
maintenance operations must be executed
by specialized staff, using suitable protec-
tion accessories.
For batteries installation it is necessary to
reach the battery compartment as indi-
cated under paragraph “ACCESS TO THE
BATTERY COMPARTMENT”.
1. Place the batteries in its compartment.
2.
Connect the terminals, respecting the
polarities, avoiding contact with other
parts that could create short circuit.
ASSEMBLING OF THE ROLLBAR
For packing reasons the support of the
blinking light is supplied disassembled.
Proceed as follows:
1. Take off the four fixing screws (1) from
the rollbar.
2. Place the rollbar into their seats (2) on
the tank.
3. Fasten the screws passing them in the
same order in their holes foreseen on the
support.
4. Complete the assembly connecting the
connectors (3) to supply the blinking light
and the working lights (optional).
BATTERY CHARGER
Make sure that the battery charger is
suitable for the installed batteries both
for their capacities and type (lead/acid
or GEL and equivalent).
In the plastic bag containing the use and
maintenance you will find the coupling
connector for the charger. It must be as-
sembled onto the cables of your charger,
following the instructions given by the
manufacturer.
ATTENTION:
This operation must be carried out by
qualified staff. A wrong or faulty cable
connection can cause serious damages to
persons or equipment.
BATTERIES RECHARGING
1. Plug the connector (3) of the battery
charger into the battery connector.
2. Proceed with the charging.
ATTENTION:
Never charge a GEL battery with a non
suitable charger. Strictly follow the
instructions supplied by the batteries
and charger manufacturer.
In order not to cause permanent damages
to the batteries, it is necessary to avoid
their complete discharge, providing for the
charging within a few minutes after the
batteries discharge signal starts blinking.
NOTE: Never leave the batteries com-
pletely discharged even if the machine is
not used. In case of traditional batteries,
please check the electrolyte level every 20
charging cycles and eventually top them
up with distilled water. Never leave the
batteries discharged for more than two
weeks.
ATTENTION:
For the recharge of the batteries it is nec-
essary to follow strictly all the indications
given by the manufacturer/distributor. All
the installation and maintenance opera-
tions must be carried out by qualified staff.
Danger of gas exhalations and emis-
sion of corrosive liquids. Fire danger:
do not approach with free flames.
BATTERIES DISPOSAL
It is compulsory to hand over exhausted
batteries, classified as dangerous waste,
to an authorized institution according to
the current laws.
https://harrissupplyind.com - To Order Parts Call 608-268-8080