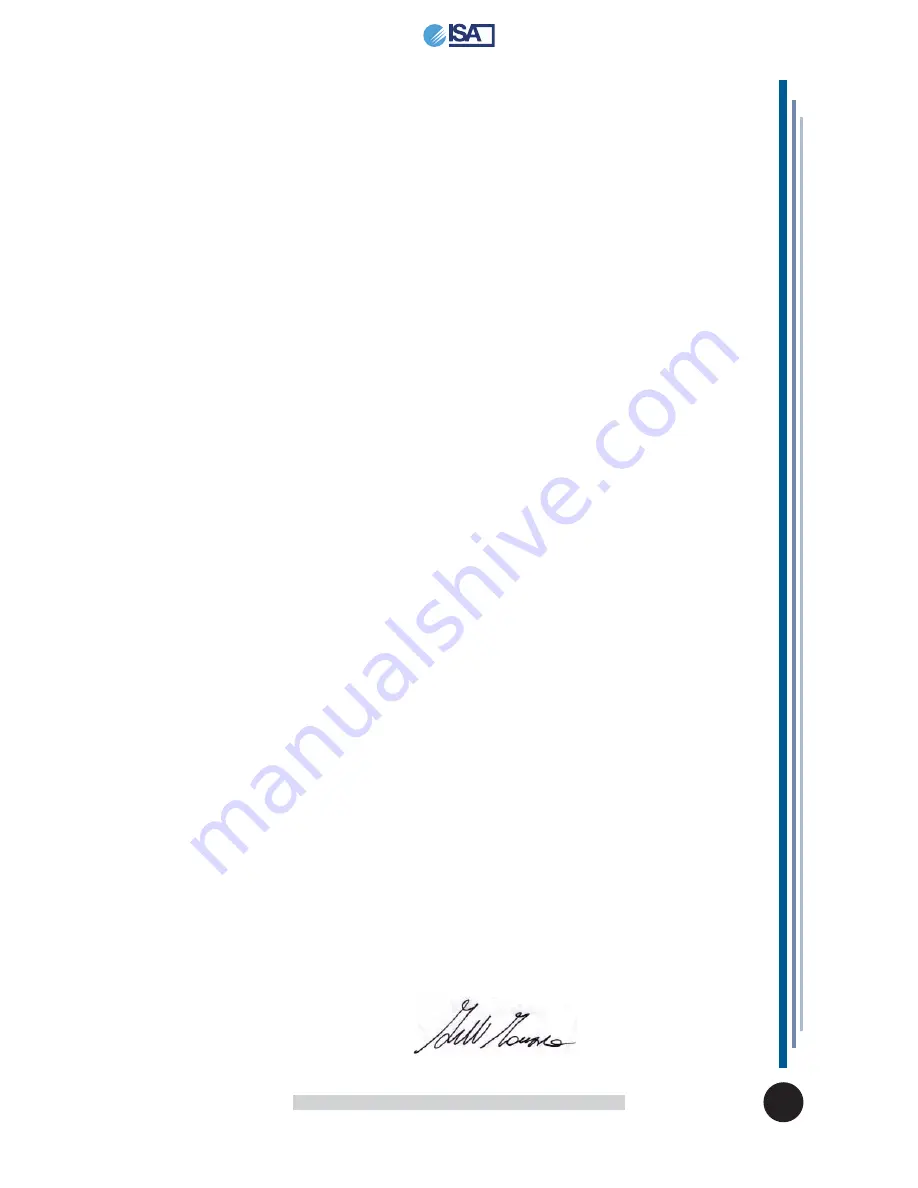
36
TORNADO
USE AND MAINTENANCE MANUAL
428000393
237
EN
UPRIGHT DISPLAY CABINETS
Attachment 1 - DECLARATION OF CONFORMITY
DECLARATION OF CONFORMITY
We: ISA S.r.l.
Via del Lavoro, 5 - 06083 - Bastia Umbra (PG)
declare under our own responsibility, that the product:
Product:
TORNADO
Serial number: .....
To which this declaration refers, is in compliance with e following:
MACHINERY SAFETY
General electric safety Standard EN 60335-1: 2012-01+Modifi cation A11. Particular requirements for commercial refrigerating appli-
ances EN 60335-2-89/Ed.2010. Standard for Measuring Electromagnetic Fields (EMF) of Electrical Appliances EN 62233:2008, Directive
2006/95/EC of the European Parliament and the Council of 12th December 2006 on the harmonisation of the Laws of Member States
relating to electrical equipment for use within certain voltage limits EN 62471/Ed.2009 Photo-biologic safety of lamps and lamp systems
ELECTROMAGNETIC COMPATIBILITY (EMC)
On the basis of the construction evaluations and test results the equipment under test is in compliance with the following standards CEI
EN 55014-1 (CEI 110-1) “Electromagnetic compatibility - Requirements for household appliances, electric tools and similar apparatus” .
Part 1: Emission “Fifth Edition Technical File 9159 (January 2008) with amendment A1 Technical File 10790 (October 2010) and amend-
ment A2 Technical File 11786 (February 2012) and CEI EN 55014-2 (CEI 210-47) “Electromagnetic compatibility - Requirements for
household appliances, electric tools and similar apparatus. Part 2: Immunity - Product family standard” First Edition Technical File 4788
- (October 1998) with amendments A1 Technical File 6577 (August 2002) and amendment A2 Technical File 9942 (August 2009), CEI
EN 61000-3-2 (CEI 110-31) “Electromagnetic Compatibility (EMC) - Part 3-2: Limits for harmonic current emissions (equipment input
current
16A per phase).” Technical File 8802 (April 2007) IV Edition with amendment A1/A2 Technical File 11514 (September 2011)
and CEI EN 61000-3-3 (CEI 210-96) “Electromagnetic Compatibility (EMC) - Part 3: Limits Section 3: Limitation of voltage fl uctuations
and fl icker in low-voltage supply systems for equipment with rated current
16A.” II Edition Technical File 13414 (March 2014).
PRESSURE EQUIPMENT DIRECTIVE (PED) 97/23/EC
As the equipment falls into a class lower than I, it is excluded from the PED’s application fi eld (art.1 par.3.6)
FOODSTUFF COMPATIBILITY
Regulation (CE) N.1935/2004 of the European Parliament and of the Council dated 27 October 2004 Regulation (CE) N.2023/2006 of
the Council dated 22 December, Directive 2008/39/CE of the Council dated 6 March 2008 Directive 2007/19/CE of the Council dated 30
March 2007 Directive 2005/79/CE of the Council dated 18 November 2005 Directive 2004/19/CE of the Council dated 10 March 2004
Directive 2004/1/CE of the Council dated 6 January 2004 Regulation (UE) 10/2011 of the Council dated 14 January 2011
ROHS and WEEE
Directive 2011/95/EC of the European Parliament and of the Council of 8th June 2011
Directive 2002/96/EC of the European Parliament and of the Council of 27th January 2003
REACH
Regulation (CE) n. 1907/2006 of the European parliament and council dated 18 December 2006 concerning the recording, evaluation,
authorisation and restriction of the chemical substances (REACH), which establishes a European Agency regarding chemical substances,
which modifi es the Directive 1999/45/CE and that repeals the Regulation (CEE) n. 793/93 of the Council and the regulation (CE) n.
1488/94 of the Commission 91/155/CEE, 93/105/CE and 2000/21/CE
SUBSTANCES THAT REDUCE THE OZONE LAYER
Regulation (CE) N. 1005/2009 dated 16 September 2009 (Offi cial Journal (OJ) of the European Union 31/10/2009 L286)
According to the requirements set by Directives: 2006/95/EC, 2004/108/EC, 2006/42/EC, 97/23/EC
The person authorised to draw-up the Technical Folder is Mr. Minelli Maurizio (Technical Department Manager)
Via del Lavoro 5 - 06083 Bastia Umbra (PG)
Bastia Umbra: 02 / 11 / 2015
(place and date of issue)
Minelli Maurizio