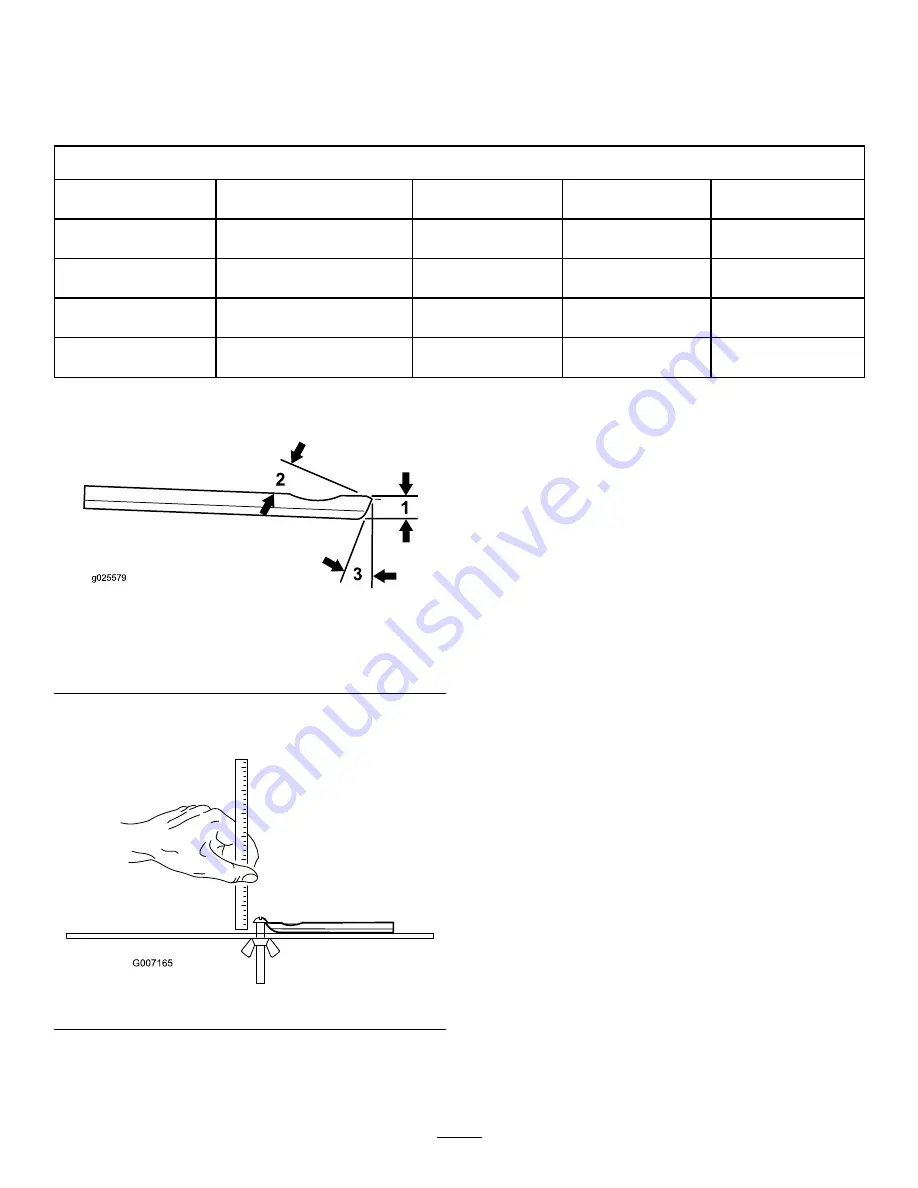
Servicing Bedknife
The bedknife service limits are listed in the following charts.
Important:
Operating the cutting unit with the bedknife below the “service limit” may result in poor after-cut
appearance and reduce the structural integrity of the bedknife for impacts.
Bedknife Service Limit Chart
Bedknife
Part No.
Bedknife Lip Height *
Service Limit*
Grind Angles
Top/Front Angles
Low HOC (Optional)
120–1641 (27 inch)
120–1642 (32 inch)
5.6 mm
(.220 inch)
.190 inch
(4.8 mm)
5/5 Degrees
EdgeMax® (Optional)
112-8910 (27 inch)
112–8956 (32 inch)
6.9 mm
(.270 inch)
.190 inch
(4.8 mm)
5/5 Degrees
Standard (Production)
114–9388 (27 inch)
114–9389 (32 inch)
6.9 mm
(.270 inch)
.190 inch
(4.8 mm)
5/5 Degrees
Heavy Duty (Optional)
114–9390 (27 inch)
114–9391 (32 inch)
9.3 mm
(.370 inch)
.190 inch
(4.8 mm)
5/5 Degrees
Recommended Top and Front Bedknife Grind Angles
g025579
2
3
Figure 23
1.
Bedknife service limit *
2.
Top grind angle
3.
Front grind angle
Note:
All bedknife service limit measurements reference the
bottom of the bedknife (Figure 24)
Figure 24
15