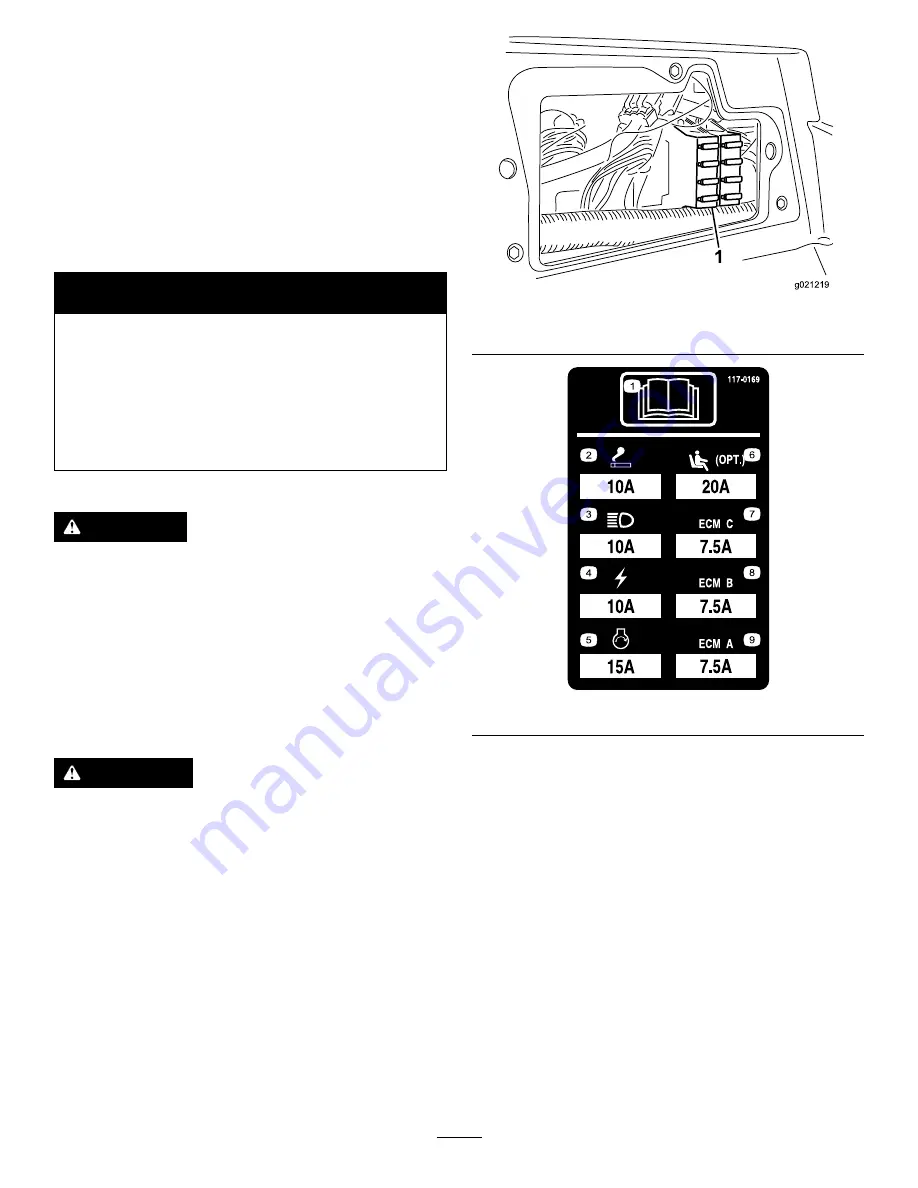
Electrical System
Maintenance
Important:
Before welding on the machine, disconnect
both cables from the battery, both wire harness plugs
from the electronic control module, and the terminal
connector from the alternator to prevent damage to the
electrical system.
Servicing the Battery
WARNING
CALIFORNIA
Proposition 65 Warning
Battery posts, terminals, and related
accessories contain lead and lead compounds,
chemicals known to the State of California
to cause cancer and reproductive harm.
Wash hands after handling.
DANGER
Battery electrolyte contains sulfuric acid which is a
deadly poison and causes severe burns.
•
Do not drink electrolyte and avoid contact with
skin, eyes, or clothing. Wear safety glasses to
shield your eyes and rubber gloves to protect
your hands.
•
Fill the battery where clean water is always
available for flushing the skin.
WARNING
Charging the battery produces gasses that can
explode.
Never smoke near the battery and keep sparks and
flames away from it.
Check the battery condition weekly or after every 50 hours
of operation. Keep the terminals and the entire battery case
clean because a dirty battery will discharge slowly. To clean
the battery, wash the entire case with a solution of baking
soda and water. Rinse it with clear water.
Fuses
There are 8 fuses in the electrical system. The fuse block
(Figure 53) is located behind the control arm access panel.
1
g021219
Figure 53
1.
Fuse block
Figure 54
37
Summary of Contents for 03673
Page 46: ...Notes 46 ...
Page 47: ...Notes 47 ...