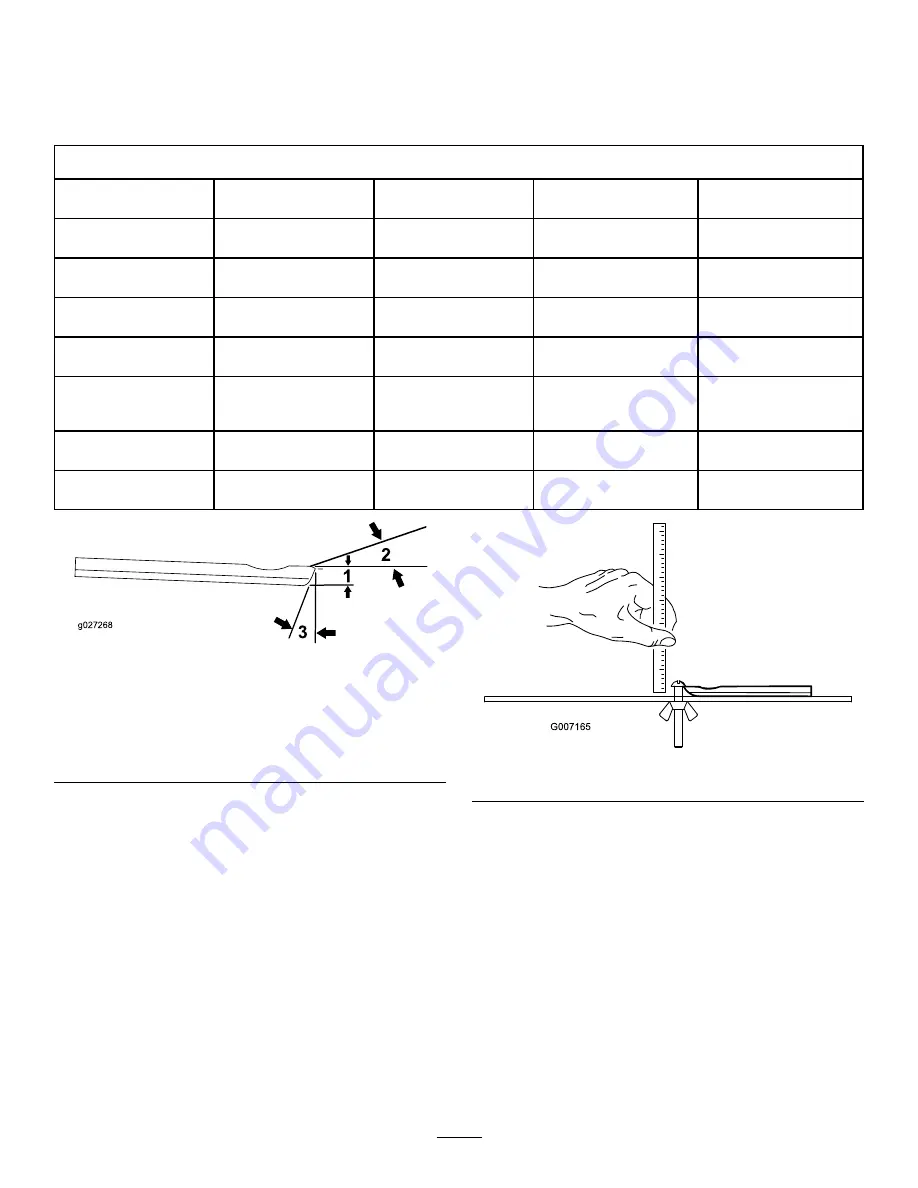
Servicing the Bedknife
The bedknife service limits are listed in the following chart.
Important:
Operating the cutting unit with the bedknife below the service limit may result in poor
after-cut appearance and reduce the structural integrity of the bedknife for impacts.
Bedknife Service Limit Chart
Bedknife
Part
Bedknife Lip Height*
Service Limit*
Grind Angles
Top/Front Angles
EdgeMax® Low HOC
(Optional)
137-0832
5.6 mm
(0.220 inch)
6.4 to 12.7 mm
(0.250 to 0.500 inch)
10/5 degrees
Low HOC (Optional)
110-4084
5.6 mm
(0.220 inch)
4.8 mm
(0.190 inch)
10/5 degrees
Extended EdgeMax®
Low HOC (Optional)
119-4280
5.6 mm
(0.220 inch)
4.8 mm
(0.190 inch)
10/10 degrees
Extended Low HOC
(Optional)
120-1640
5.6 mm
(0.220 inch)
4.8 mm
(0.190 inch)
10/10 degrees
EdgeMax®
(Models 03698 and
03699)
137-0833
6.9 mm
(0.270 inch)
4.8 mm
(0.190 inch)
10/5 degrees
Standard (Optional)
108-9096
6.9 mm
(0.270 inch)
4.8 mm
(0.190 inch)
10/5 degrees
Heavy Duty (Optional)
110-4074
9.3 mm
(0.370 inch)
4.8 mm
(0.190 inch)
10/5 degrees
g027268
Figure 32
Recommended Top and Front Bedknife Grind Angles
1.
Bedknife service limit*
2.
Top grind angle
3.
Front grind angle
Note:
All bedknife service limit measurements relate
to the bottom of the bedknife (
g007165
Figure 33
20
Summary of Contents for 03698
Page 25: ...Notes ...