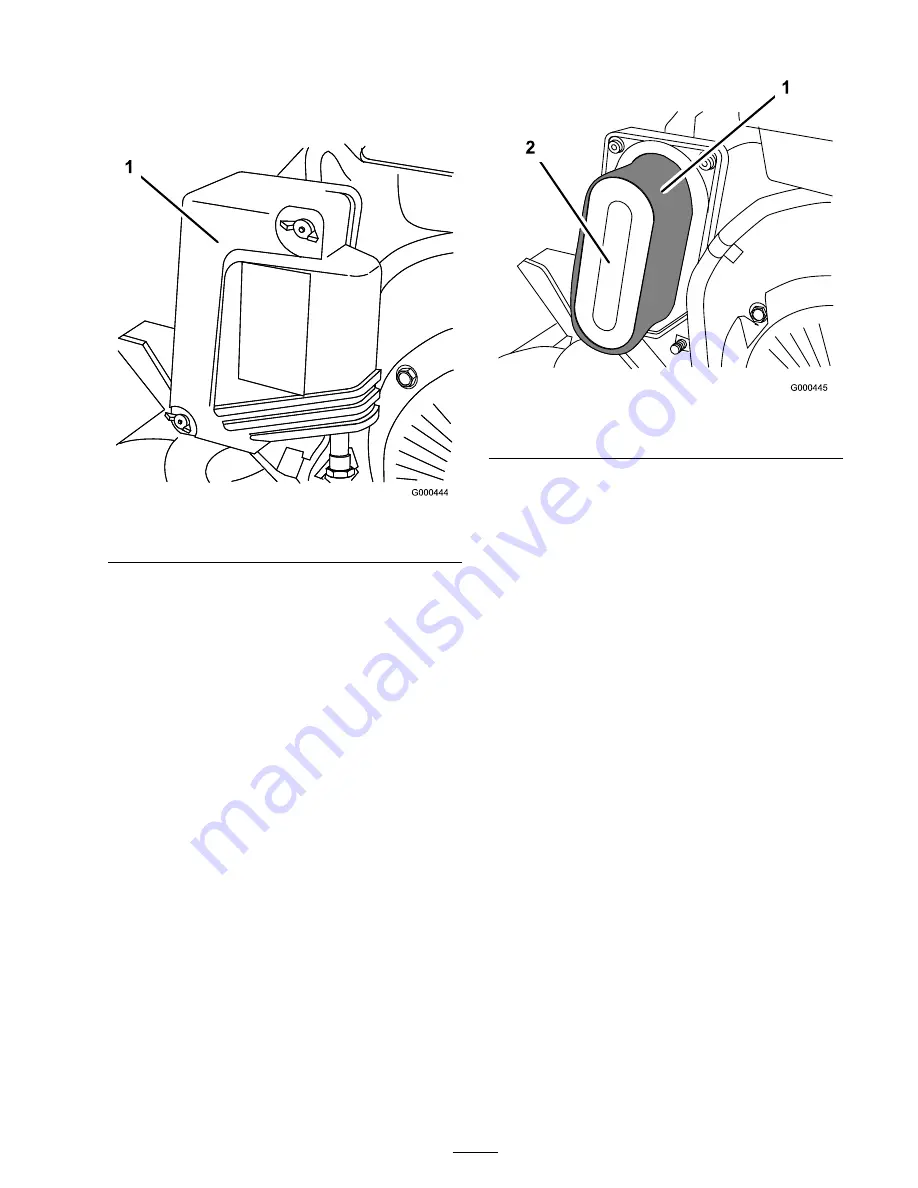
2. Remove wing nuts securing air cleaner cover
to air cleaner and remove cover. Clean cover
thoroughly (Figure 23).
Figure 23
1. Air cleaner cover
3. If foam element is dirty, remove it from paper
element (Figure 24). Clean thoroughly.
A. Wash foam element in a solution of liquid
soap and warm water. Squeeze to remove
dirt, but do not twist because the foam may
tear.
B. Dry by wrapping in a clean rag. Squeeze
rag and foam element to dry, but do not
twist because the foam may tear.
C. Saturate element with clean engine oil.
Squeeze element to remove excess oil and
to distribute oil thoroughly. An oil damp
element is desirable.
Figure 24
1. Foam element
2. Paper element
4. When servicing foam element, check condition
of paper element. Clean or replace every 100
hours or as required.
5. Install foam element, paper element, and air
cleaner cover.
Important:
Do not operate the engine
without the air cleaner element because
extreme engine wear and damage will
likely result.
Replacing the Spark Plug
Use an NGK BPR 5ES spark plug or equivalent.
Correct air gap is 0.028-0.032 inch Remove plug
after every 100 operating hours and check its
condition.
1. Pull molded wire off spark plug (Figure 25).
25