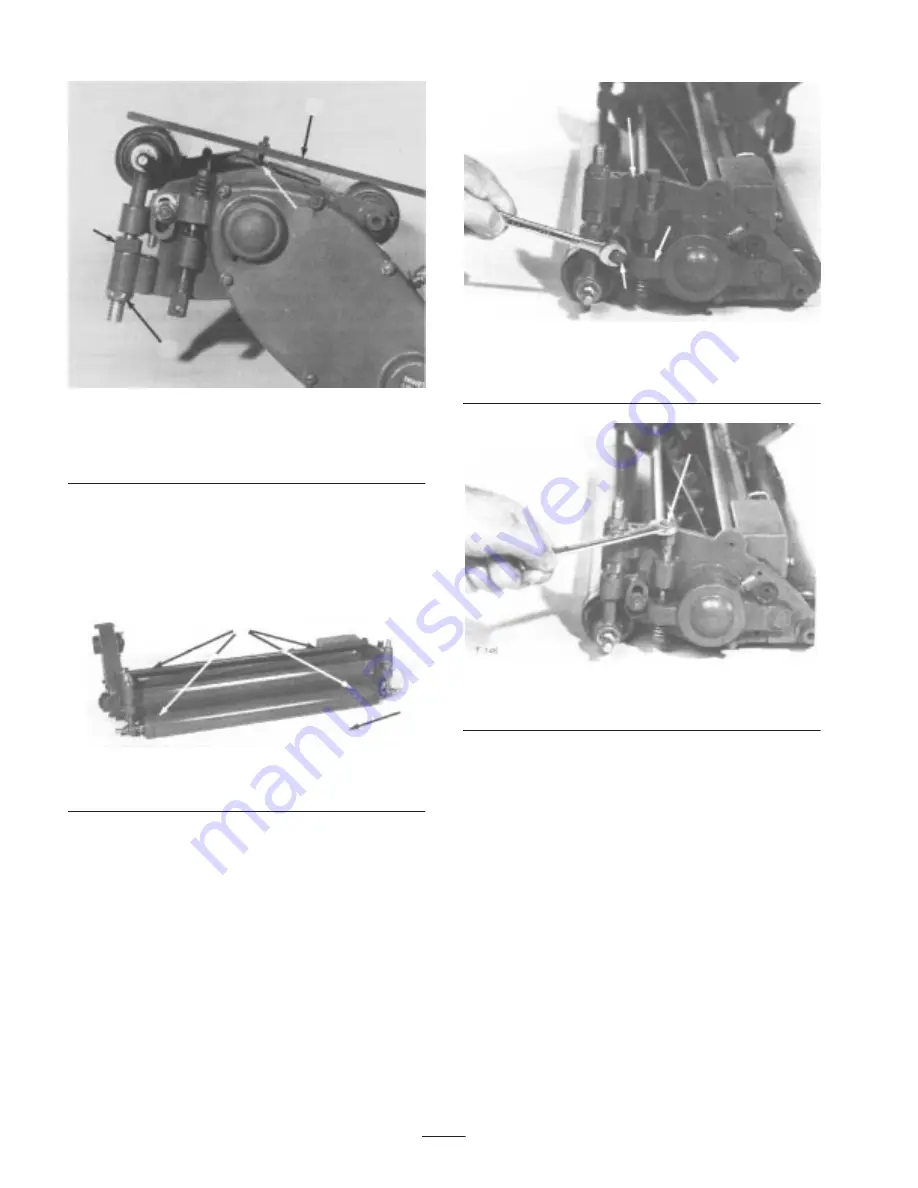
14
2
1
4
3
Figure 10
1.
Gauge bar against rollers
2.
Screw head over cutting
edge
3.
Top nut
4.
Adjustment nut
5. Tighten top nuts to secure roller adjustment (Fig. 10).
Turn cutting unit over and place on a level surface
(Fig. 11). Press down on each end of the front and rear
rollers (Fig. 11). Each roller should contact level
surface completely across unit (Fig. 11). If rollers do
not contact, repeat steps 3 and 4.
2
1
Figure 11
1.
Level surface
2.
Press down
Reel To Bedknife Adjustment
Note: Adjustment procedures can usually be more
accurate and precise with cutting unit adjusted on a
workbench.
1. Loosen nuts securing left and right reel brackets to
side plates (Fig. 12).
2. Adjust reel to knife clearance with adjusting screws at
each end of unit (Fig. 13). NEVER ALLOW
BEDKNIFE TO BEAR HEAVILY AGAINST REEL.
2
1
3
Figure 12
1.
Nut
2.
Reel bracket
3.
Side plate
1
Figure 13
1.
Reel adjusting screw
3. Place the newspaper at right angles to the top face of
the bedknife against the front cutting edge and rotate
the reel blades against the paper. The reel blades
should cut the paper cleanly all across the bedknife. If
the paper is not cleanly cut, the mower should be
either backlapped or resharpened: refer to Backlap
Operation and Reel and Bedknife Grinding.
4. Place a strip of newspaper flat on the top face of the
bedknife and adjust reel down until reel blades pinch
the paper equally all across the bedknife.
5. Tighten nuts to secure the adjustment.