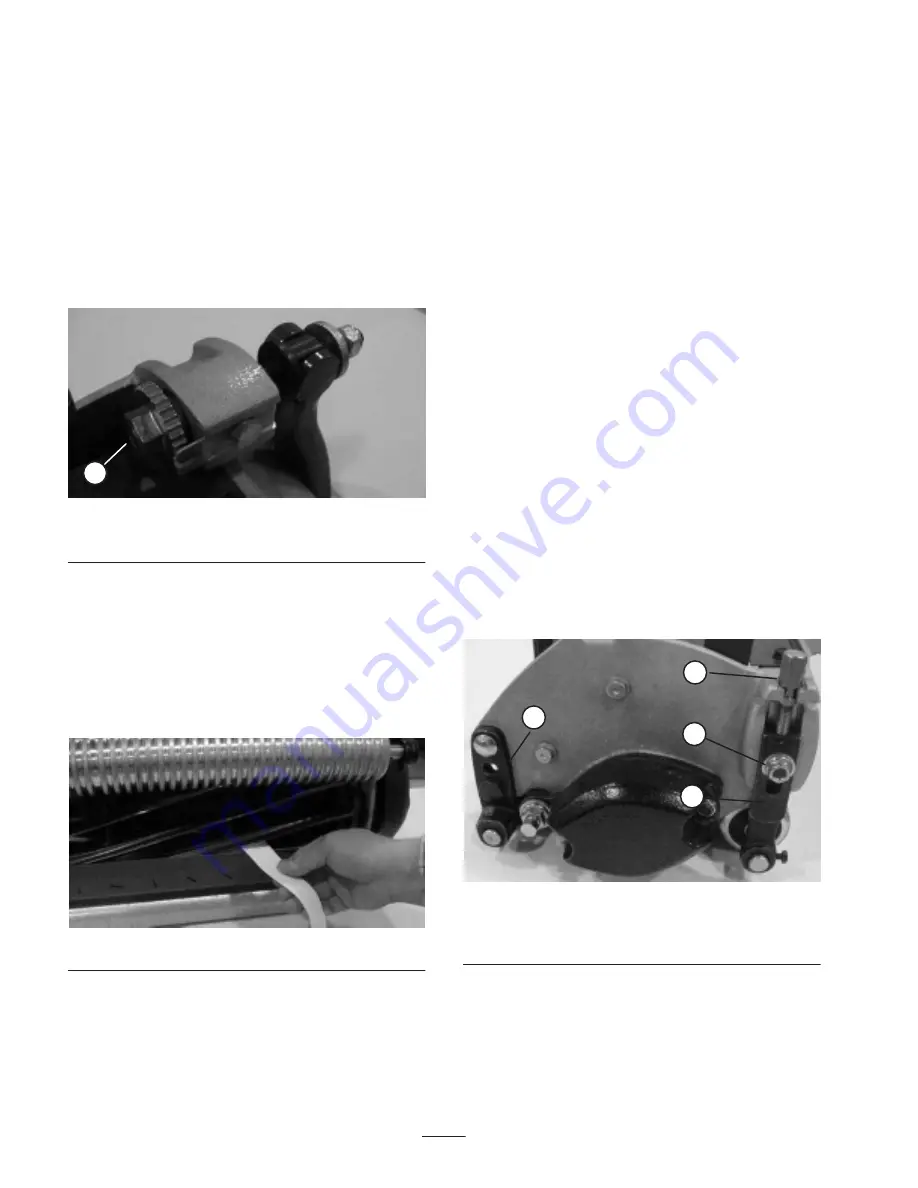
16
7. When roller is level, tighten nuts securely.
Adjusting the Bedknife to the
Reel
Bedknife to reel adjustment is accomplished by loosening
or tightening bedbar adjusting screws, located on top of
mower.
1. Position machine on a flat, level work surface. Make
sure reel contact is removed by turning bedbar
adjusting screws counterclockwise (Fig. 16).
1
Figure 16
1.
Bedbar adjusting screw
2. Tilt mower on back to expose bedknife and reel.
3. At one end of reel, insert a long strip of newspaper
between reel and bedknife (Fig. 17). While slowly
rotating reel forward, turn bedbar adjusting screw
clockwise (on same end of reel, one click at a time,
until paper is pinched lightly, when inserted from the
front, parallel to the bedknife. A slight drag will be
noted as the paper is pulled (Fig. 16).
Figure 17
Note: Each time adjusting screw is rotated one click
clockwise, bedknife moves .0007 in. closer to reel. Do not
overtighten the adjusting screws.
4. Check for light contact at other end of reel using paper
and adjust as required.
5. After adjustment is accomplished, check to see if reel
can pinch paper when inserted from the front and cut
paper when inserted at a right angle to the bedknife
(Fig. 17). It should be possible to cut paper with
minimum contact between the bedknife and the reel
blades. Should excessive reel drag be evident it will be
either necessary to backlap or regrind the cutting unit
to achieve the sharp edges needed for precision cutting
(see Toro reel sharpening manual).
Adjusting the Height of Cut
1. Adjust rear roller brackets (Fig. 18) to upper or lower
position depending on desired height of cut range.
•
The upper position (factory setting) is used when
height of cut settings range from 1/16 to 5/32”.
•
The lower position is used when height of cut settings
range from 1/8” to 19/64”.
2. Verify that rear roller is level and that bedknife to reel
contact is correct. Tip mower on back to expose front
and rear rollers and bedknife.
3. Loosen locknuts securing height-of-cut arms to
cutting unit side plates (Fig. 18).
2
3
4
1
Figure 18
1.
Rear roller bracket
2.
Height-of-cut arm
3.
Locknut
4.
Adjusting screw