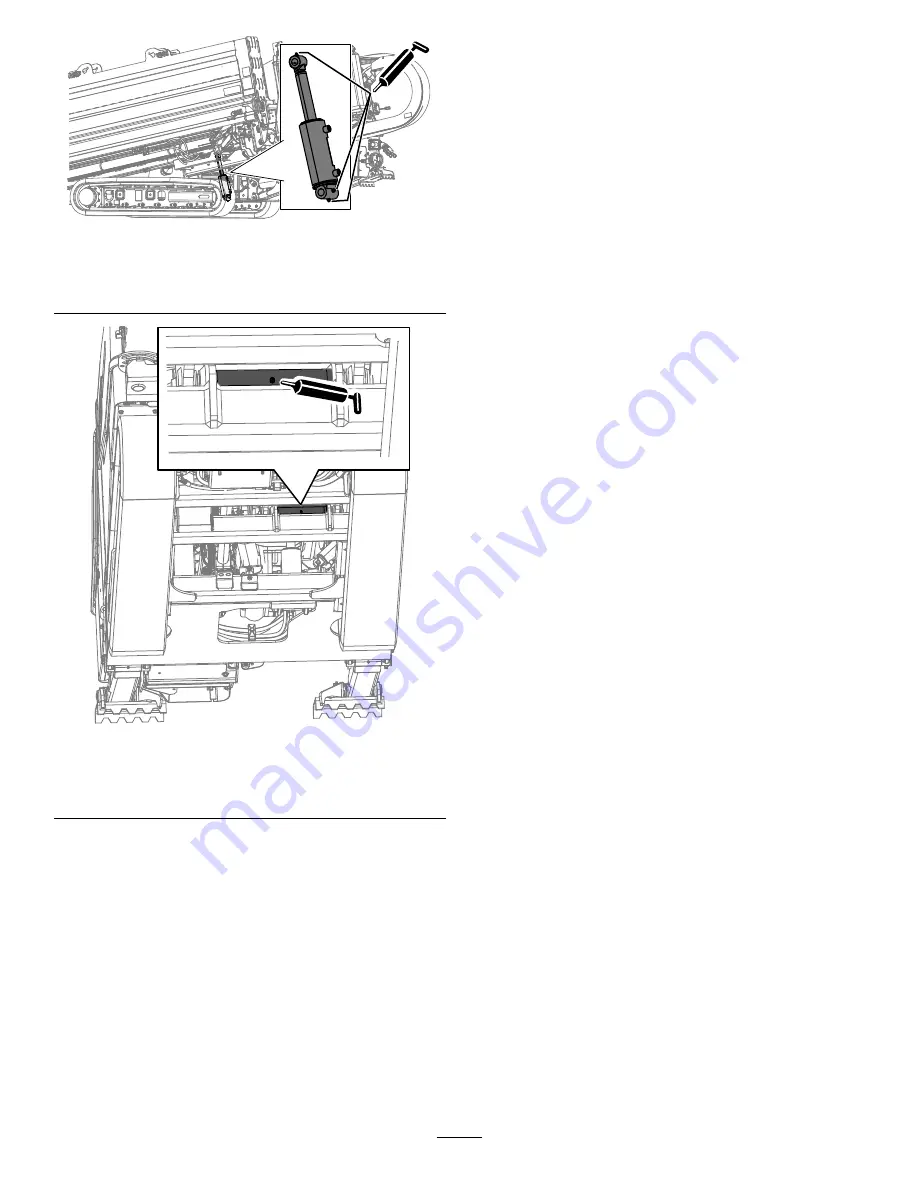
g223045
Figure 85
Lift Cylinder (Drill/Carriage Side; lower grease fitting is
behind the track roller)—3 fittings
g223046
Figure 86
Thrust Frame Pivot Pin (Underside of the Machine)—1
fitting
Engine Maintenance
Engine Safety
•
Shut off the engine before checking the oil or
adding oil to the crankcase.
•
Do not change the governor speed or overspeed
the engine.
Servicing the Air Cleaner
Check the air-cleaner body for damage that could
cause an air leak and replace it if it is damaged. Check
the entire intake system for leaks, damage, or loose
hose clamps. Also, inspect the rubber intake-hose
connections at the air cleaner and turbocharger to
ensure that the connections are complete.
Service the air-cleaner filter only when the “Check Air
Filter” message is displayed on the display; refer to
the
Software Guide
for the machine. Changing the air
filter before it is necessary only increases the chance
of dirt entering the engine when you remove the filter.
Ensure that the cover is seated correctly and seals
with the air-cleaner body.
Servicing the Air-Cleaner Cover
Service Interval:
Every 50 hours—Remove the
air-cleaner cover and clean out the
debris. Do not remove the filter.
Check the air-cleaner body for damage that could
cause an air leak. Replace a damaged air cleaner
body.
Clean the air-cleaner cover (
72
Summary of Contents for 2226
Page 107: ...Notes ...
Page 108: ......