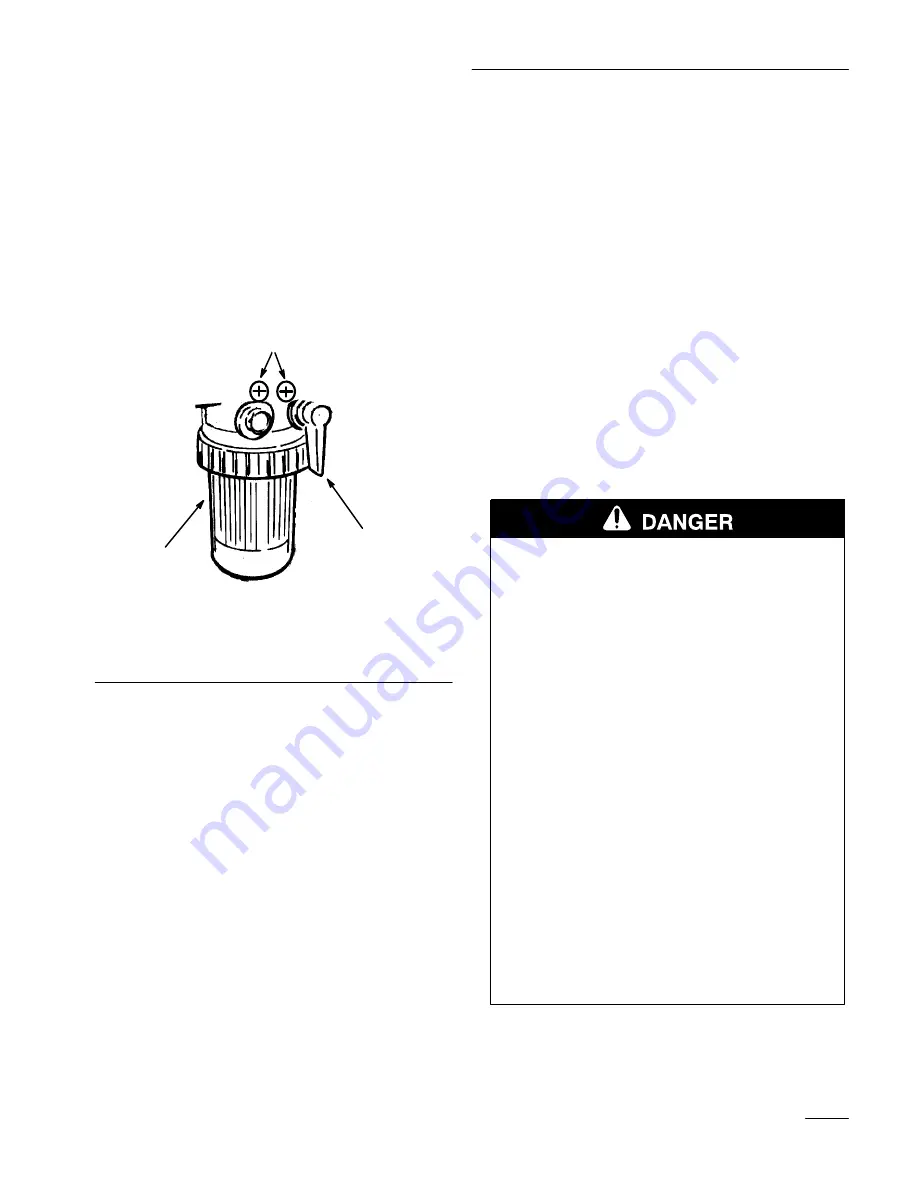
Maintenance
29
4.
Remove and inspect fuel filter. Replace if dirty.
5.
Re–install bowl to filter head. Make sure O–ring
is positioned properly between bowl mounting
nut and filter head.
6.
Open fuel shut–off on filter.
7.
Open bleed screws on filter mounting head to
re–fill bowl with fuel. Close bleed screws.
1
2
3
Figure 13
1.
Filter
2.
Fuel shut–off
3.
Bleed screws
Bleeding Fuel System
Bleeding of the fuel system is required if:
•
Initial start up of a new machine or a machine
that has been stored.
•
Engine has ceased running due to lack of fuel.
•
Maintenance has been performed on fuel system
components.
1.
Park the machine on a level surface. Make sure
fuel tank is at least half full.
2.
Lower the loader arms and turn the ignition key
to “OFF” to stop the engine. Remove the key.
3.
Open fuel shut–off on fuel filter and open fuel
cap vent.
POTENTIAL HAZARD
•
Under certain conditions fuel is extremely
flammable and highly explosive.
WHAT CAN HAPPEN
•
A fire or explosion from fuel can burn you,
others, and cause property damage.
HOW TO AVOID THE HAZARD
•
Use a funnel and fill the fuel tank outdoors,
in an open area, when the engine is cold.
Wipe up any fuel that spills.
•
Do not fill the fuel tank completely full.
Add fuel to the fuel tank until the level is
1/4” to 1/2” (6 mm to 13 mm) below the
bottom of the filler neck. This empty space
in the tank allows fuel to expand.
•
Never smoke when handling fuel, and stay
away from an open flame or where fuel
fumes may be ignited by a spark.
•
Store fuel in an approved container and
keep it out of the reach of children. Never
buy more than a 30-day supply.