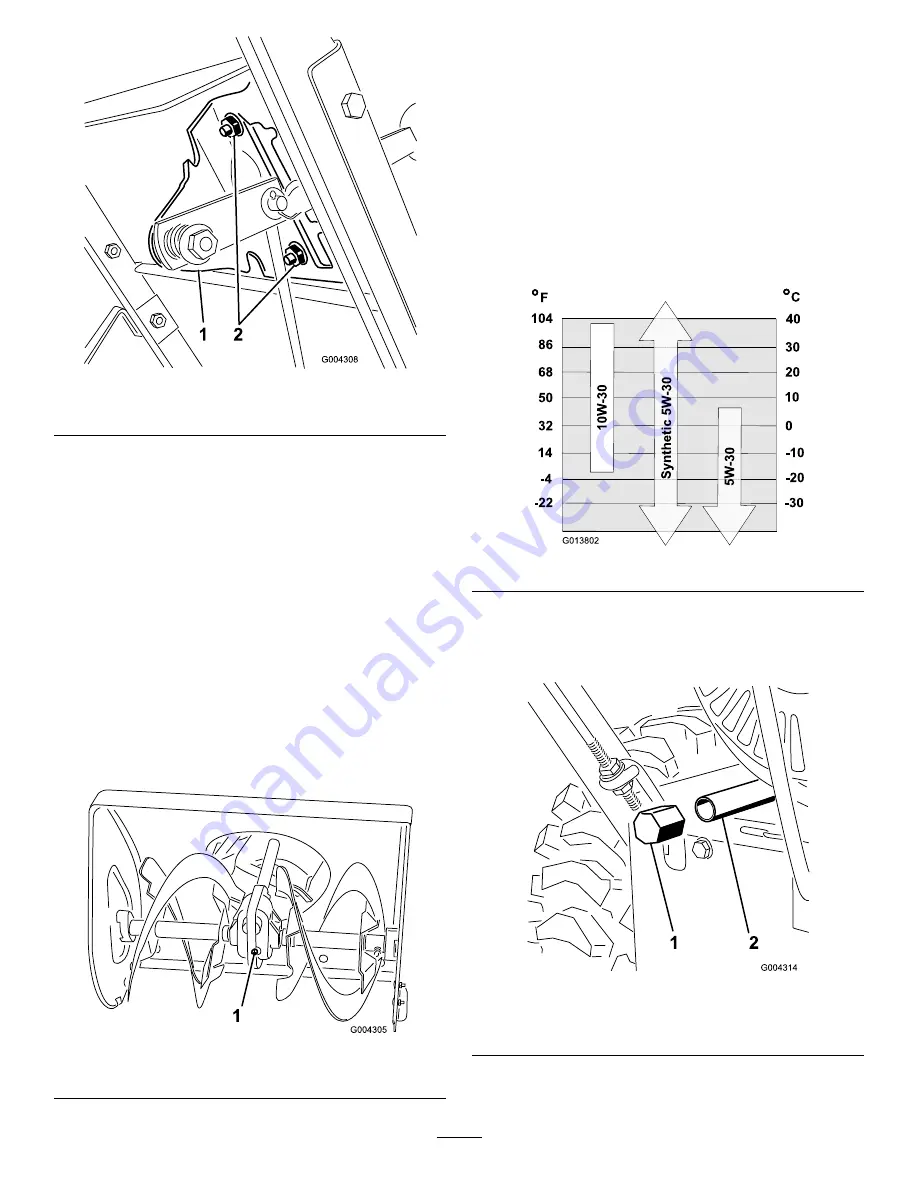
Figure 29
1.
Speed selector plate
2.
Flange nuts
4.
Shift the speed selector lever to third gear. Push down
on the speed selector plate and tighten the flange nuts
that secure the speed selector plate.
5.
If these steps do not resolve the issue, take the unit to
an authorized service location.
Checking the Auger Gearbox
Grease
Service Interval:
Yearly
The auger gearbox is packed with 5 oz. (140 g) of Lubriplate
MAG-1 (a low-temperature, high-pressure grease) and is
sealed at the factory. The pipe plug (Figure 30) is for factory
use only; you do not need to check or add grease. If the
gearbox is leaking grease, contact an Authorized Service
Dealer.
Figure 30
1.
Pipe plug
Changing the Engine Oil
Service Interval:
After the first 5 hours
Yearly
Every 50 hours
If possible, run the engine just before changing the oil because
warm oil flows better and carries more contaminants.
Max. fill: 20 oz. (0.6 l), type: automotive detergent oil with an
API service classification of SF, SG, SH, SJ, SL, or higher.
Refer to Figure 31 to select the best oil viscosity for the
outdoor temperature range expected.
Figure 31
1.
Block up the rear of the machine.
2.
Remove the left wheel.
3.
Clean the area around the oil drain plug (Figure 32).
Figure 32
1.
Oil drain plug
2.
Drain extension
4.
Slide an oil drain pan under the drain extension and
remove the oil drain plug (Figure 32).
21