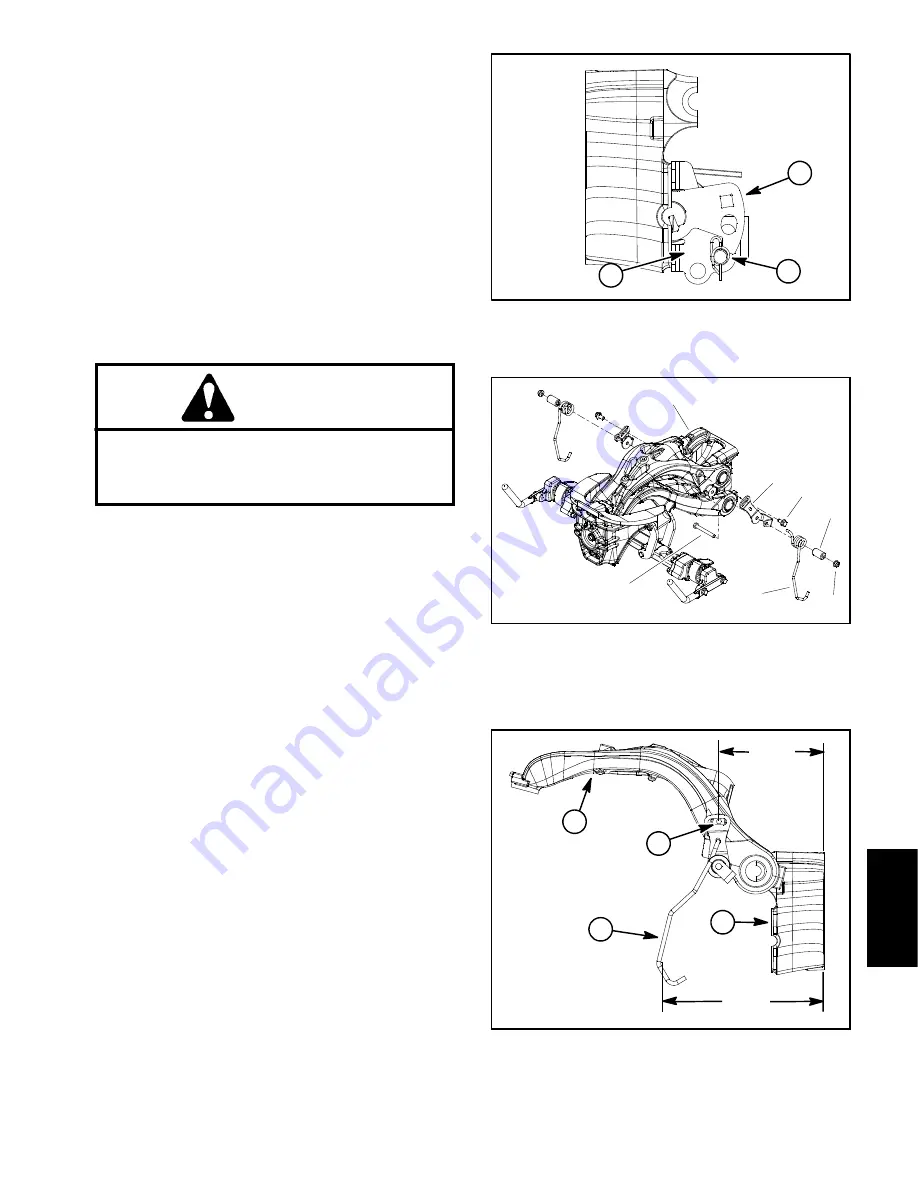
Greensmaster 3320/3420
Page 7 -- 25
Chassis
Disassembly (Fig. 20)
1. If cutting unit suspension is attached to machine:
A. Park machine on a level surface, engage the
parking brake, lower the cutting units and stop the
engine. Remove key from the ignition switch.
B. Disconnect the cutting units from the electrical
power supply by separating the cutting unit power
disconnect couplers (see Opening Electrical Circuit
to Cutting Units in the General Information section of
this chapter). This will prevent unexpected cutting
unit operation.
2. Remove tension from suspension counterbalance
assembly:
CAUTION
Be careful when removing tension from the sus-
pension counterbalance system. The counter-
balance spring is under heavy load and may
cause personal injury.
A. Remove cotter pin from clevis pin that secures
counterbalance tensioner arm.
B. Use 3/8” drive breaker bar in tensioner arm
square drive hole to hold tensioner arm in place so
that clevis pin can be removed.
C. Remove clevis pin and allow counterbalance
springs to relax.
3. Disassemble suspension assembly as required us-
ing Figure 20 as a guide.
NOTE:
Medium strength Loctite #609 retaining com-
pound is applied to ball joint housing during assembly.
Localized heat around the ball joint housing will allow
easier ball joint removal from A--arm.
Assembly (Fig. 20)
1. Install all removed suspension assembly compo-
nents using Figure 20 as a guide.
A. If any ball joint (item 3) was removed from A--arm,
clean ball joint housing and A--arm bore with Loctite
cleaning solvent (or equivalent) and allow to dry. Ap-
ply Loctite #609 retaining compound (or equivalent)
to ball joint housing before inserting ball joint into A--
arm.
B. If any clamp (item 9) was removed, make sure
that raised boss in clamp bore is positioned in groove
of ball joint stud before securing clamp.
1. Clevis pin
2. Counterbalance mount
3. Tensioner arm
Figure 21
2
1
3
1. Suspension assembly
2. Cap screw
3. Spring retainer
4. Flange head screw
5. Spacer
6. Flange nut
7. Stabilizer spring
Figure 22
1
3
5
7
4
6
2
1. Stabilizer spring
2. Upper a--arm
3. Pivot mount
4. Spring hole
Figure 23
2
1
3
8.760”
(222.5 mm)
5.710”
(145.0 mm)
4
Chas
sis
Summary of Contents for Greensmaster 3420 TriFlex
Page 2: ...Greensmaster 3320 3420 This page is intentionally blank ...
Page 4: ...Greensmaster 3320 3420 This page is intentionally blank ...
Page 6: ...Greensmaster 3320 3420 This page is intentionally blank ...
Page 24: ...Greensmaster 3320 Page 3 6 Gasoline Engine This page is intentionally blank ...
Page 38: ...Greensmaster 3420 Page 4 4 Diesel Engine This page is intentionally blank ...
Page 54: ...Greensmaster 3420 Page 4 20 Diesel Engine This page is intentionally blank ...
Page 56: ...Greensmaster 3320 3420 Hydraulic System Page 5 2 This page is intentionally blank ...
Page 150: ...Greensmaster 3320 3420 Hydraulic System Page 5 96 This page is intentionally blank ...
Page 250: ...Greensmaster 3320 3420 Page 6 100 Electrical System This page is intentionally blank ...
Page 277: ...Greensmaster 3320 3420 Page 7 27 Chassis This page is intentionally blank Chassis ...
Page 325: ...Greensmaster 3320 3420 Groomer Page 9 13 This page is intentionally blank Groomer ...
Page 340: ...Greensmaster 3320 3420 Page 10 2 Foldout Drawings This page is intentionally blank ...
Page 347: ...Page 10 9 This page is intentionally blank ...
Page 356: ...Page 10 18 E Reels Wire Harness Drawing Greensmaster 3320 3420 Serial Number Below 312000000 ...
Page 358: ...Page 10 20 E Reels Wire Harness Drawing Greensmaster 3320 3420 Serial Number Above 312000000 ...
Page 360: ...Page 10 22 This page is intentionally blank ...