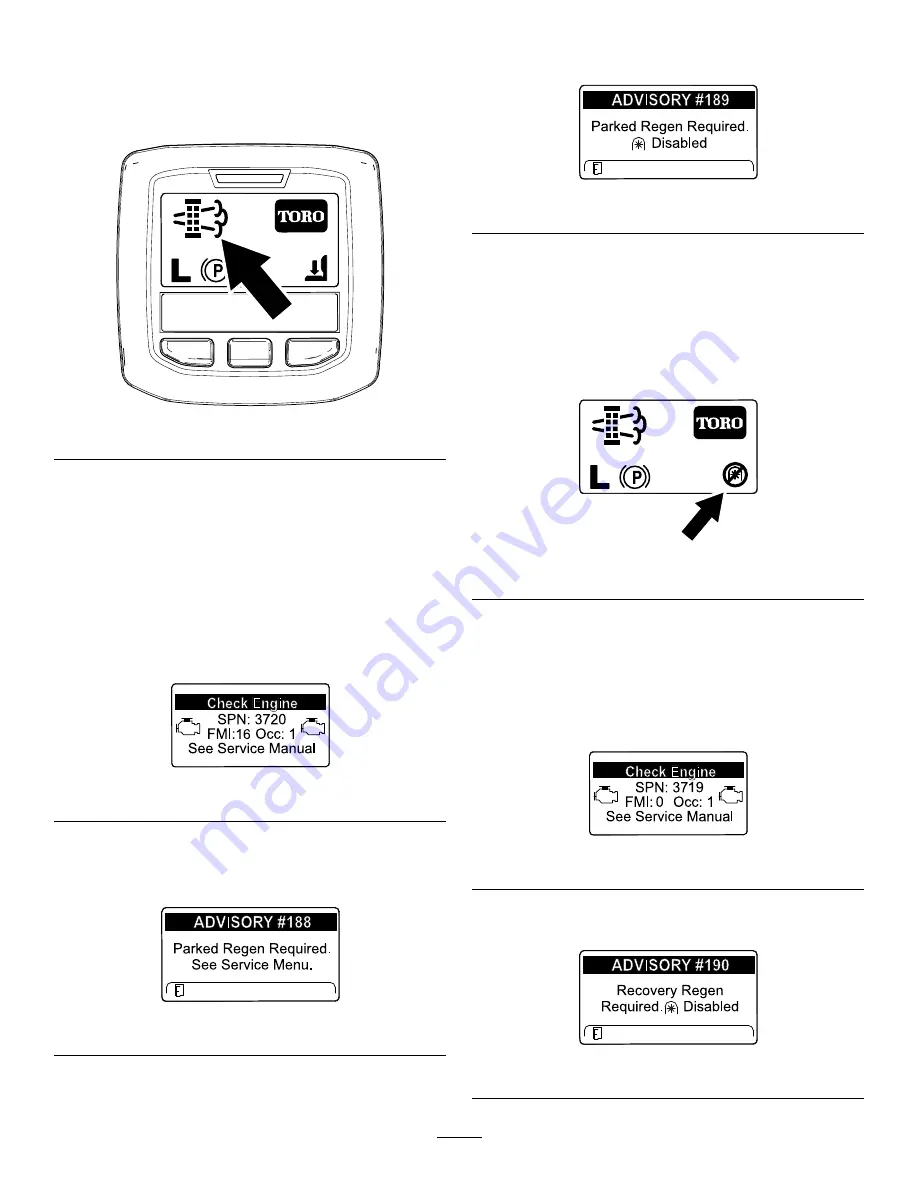
Parked or Recovery Regeneration
•
When the engine computer requests either a
parked regeneration or a recovery regeneration,
the regeneration request icon (
) displays
in the InfoCenter.
g224404
Figure 54
•
The machine does not automatically perform a
parked regeneration or a recovery regeneration,
you must run the regeneration through the
InfoCenter.
Parked Regeneration Messages
When a parked regeneration is requested by the
engine computer the following messages display in
the InfoCenter:
•
Engine warning SPN 3720, FMI 16 (
g213863
Figure 55
•
Parked regeneration required A
DVISORY
#188
Note:
Advisory #188 displays every 15 minutes.
g224397
Figure 56
•
If you do not perform a parked regeneration
within 2 hours, the InfoCenter displays parked
regeneration required—power takeoff disabled
A
DVISORY
#189 (
g224398
Figure 57
Important:
Perform a parked regeneration to
restore the PTO function; refer to
Perform a Parked or Recovery Regeneration
(page 47)
and
Performing a Parked or Recovery
Regeneration (page 47)
.
Note:
The Home screen displays the PTO
disabled Icon (
g224415
Figure 58
Recovery Regeneration Messages
When a recovery regeneration is requested by the
engine computer, the following messages display in
the InfoCenter:
•
Engine warning SPN 3719, FMI 0 (
g213867
Figure 59
•
Recovery regeneration required—power takeoff
disabled A
DVISORY
#190 (
)
g224399
Figure 60
46
Summary of Contents for Groundsmaster 4000
Page 85: ...Notes ...