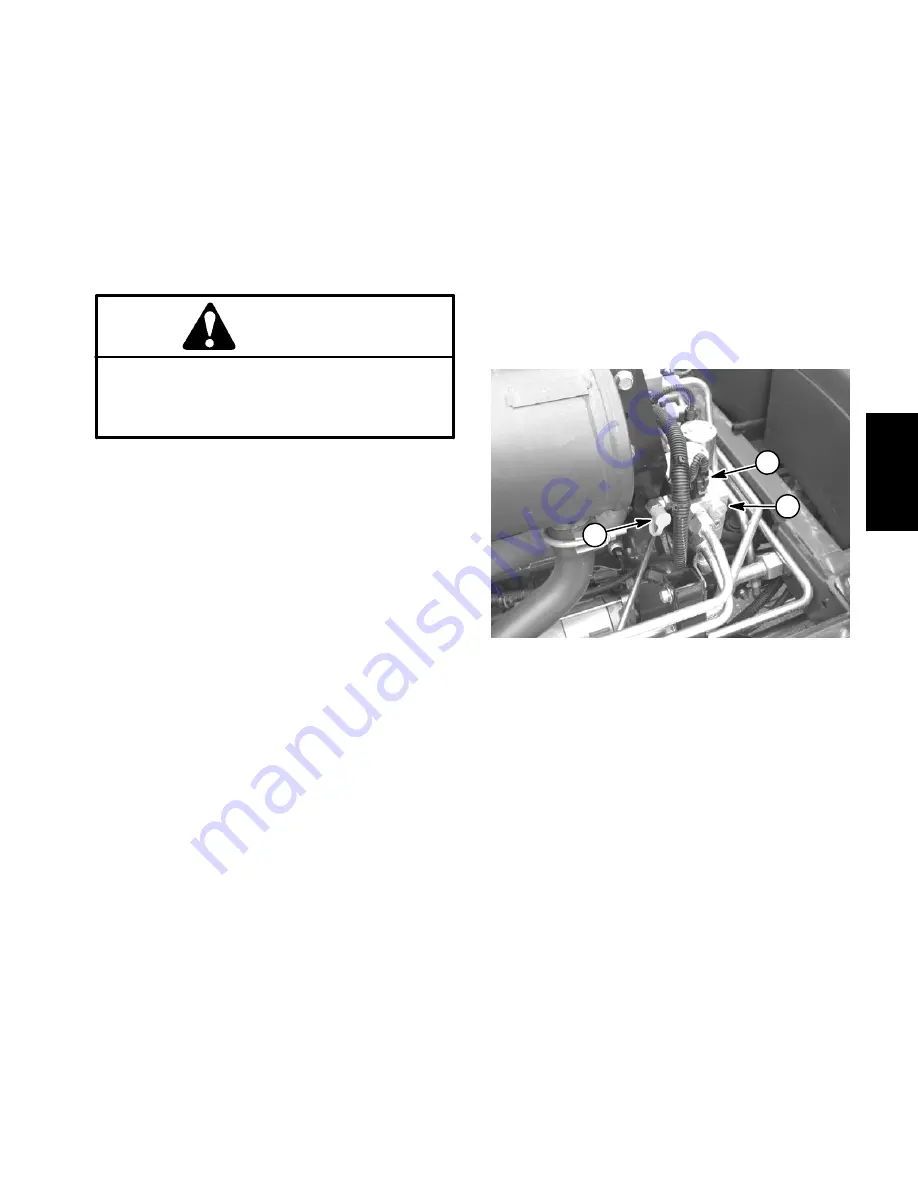
Reelmaster 7000
Hydraulic System
Page 4 -- 65
The cooling fan circuit test should be performed to make
sure that the engine cooling fan circuit has the correct
system pressure and fan speed.
Procedure for Cooling Fan Circuit Test
1. Make sure hydraulic oil is at normal operating tem-
perature by operating the machine for approximately ten
(10) minutes. Make sure the hydraulic tank is full.
2. Park machine on a level surface with the cutting units
lowered and off. Make sure engine is off and the parking
brake is applied.
CAUTION
Prevent personal injury and/or damage to equip-
ment. Read all WARNINGS, CAUTIONS and Pre-
cautions for Hydraulic Testing at the beginning
of this section.
3. Raise and support hood to gain access to fan control
manifold (Fig. 47). Connect a 5,000 PSI (345 bar) gauge
with hydraulic hose attached to test fitting in port G2 on
rear of manifold.
4. After installing tester, start engine and run at idle
speed. Check for hydraulic leakage and correct before
proceeding with test.
5. Move throttle to full speed
(2850 RPM)
.
6. While monitoring the pressure gauge and using a
phototac to identify the cooling fan speed, disconnect
the wire harness connector (white/green and black
wires) from the proportional relief valve solenoid at fan
control manifold (port PRV). Both fan speed and pres-
sure should increase and stabilize after the solenoid is
disconnected.
PRESSURE GAUGE READING TO BE approxi-
mately
3000 PSI (207 bar)
PHOTOTAC (fan speed) READING TO BE approxi-
mately
2800 RPM
7. Stop engine and record test results.
8. If pressure rises to approximately
3000 PSI (207
bar)
but fan speed is low, consider that the fan motor is
worn or damaged. If pressure and fan speed are both
low, consider that gear pump P4 is worn or damaged
(see Gear Pump P4 Flow Test in this section).
NOTE:
If pressure and fan speed are both low and gear
pump P4 flow proves to be correct (see Gear Pump P4
Flow Test in this section), suspect that seals in fan con-
trol manifold are leaking or faulty (see Fan Control Man-
ifold Service in the Service and Repairs section of this
chapter) or that fan motor is worn or damaged.
9. When testing is complete, remove pressure gauge
from manifold fitting and reconnect wire harness to pro-
portional relief valve solenoid. Install dust cap to test port
fitting. Lower and secure hood.
1. Fan control manifold
2. Test fitting (port G2)
3. PRV solenoid
Figure 47
2
1
3
Hydraulic System
Summary of Contents for Reelmaster 7000
Page 2: ...Reelmaster 7000 This page is intentionally blank ...
Page 4: ...Reelmaster 7000 This page is intentionally blank ...
Page 10: ...Reelmaster 7000 Page 1 6 Safety This page is intentionally blank ...
Page 12: ...0 09375 Reelmaster 7000 Page 2 2 Product Records and Maintenance Equivalents and Conversions ...
Page 34: ...Reelmaster 7000 Page 3 18 Kubota Diesel Engine This page is intentionally blank ...
Page 36: ...Reelmaster 7000 Hydraulic System Page 4 2 This page is intentionally blank ...
Page 45: ...Reelmaster 7000 Hydraulic System Page 4 11 This page is intentionally blank Hydraulic System ...
Page 115: ...Reelmaster 7000 Hydraulic System Page 4 81 This page is intentionally blank Hydraulic System ...
Page 131: ...Reelmaster 7000 Hydraulic System Page 4 97 This page is intentionally blank Hydraulic System ...
Page 139: ...Reelmaster 7000 Hydraulic System Page 4 105 This page is intentionally blank Hydraulic System ...
Page 147: ...Reelmaster 7000 Hydraulic System Page 4 113 This page is intentionally blank Hydraulic System ...
Page 151: ...Reelmaster 7000 Hydraulic System Page 4 117 This page is intentionally blank Hydraulic System ...
Page 168: ...Reelmaster 7000 Hydraulic System Page 4 134 This page is intentionally blank ...
Page 214: ...Reelmaster 7000 Page 5 46 Electrical System This page is intentionally blank ...
Page 247: ...Reelmaster 7000 Page 7 3 Chassis This page is intentionally blank Chassis ...
Page 264: ...Reelmaster 7000 Page 7 20 Chassis This page is intentionally blank ...
Page 271: ...Reelmaster 7000 DPA Cutting Units Page 8 7 This page is intentionally blank DPA Cutting Units ...
Page 304: ...Reelmaster 7000 DPA Cutting Units Page 8 40 This page is intentionally blank ...
Page 306: ...Reelmaster 7000 Foldout Drawings Page 9 2 This page is intentionally blank ...
Page 310: ...Page 9 6 Reelmaster 7000 Main Wire Harness ...
Page 312: ...Page 9 8 Reelmaster 7000 Seat and Console Wire Harness ...
Page 314: ...Page 9 10 Reelmaster 7000 Power Center Wire Harness ...