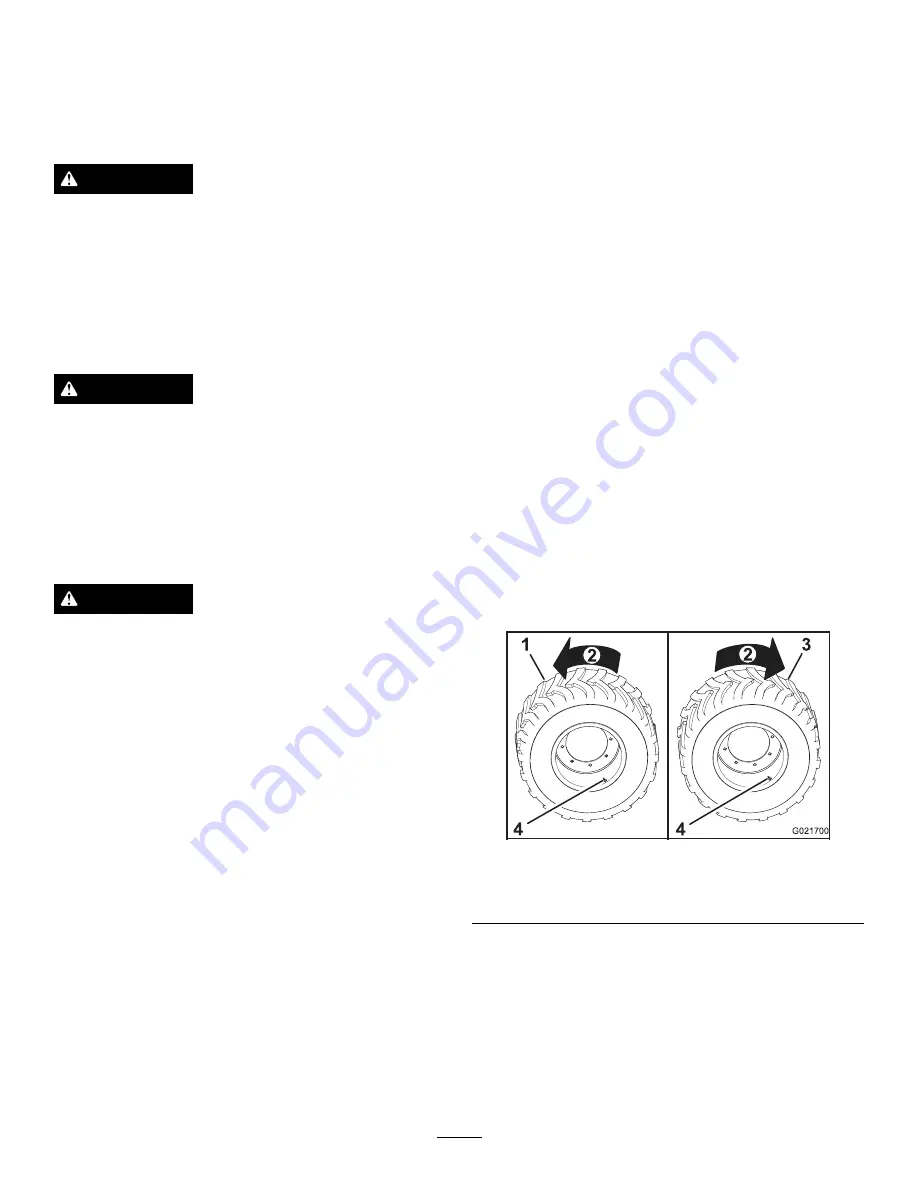
Drive System
Maintenance
Servicing the Tires
WARNING
Exploding tires and/or rim parts can cause injury
or death.
Keep yourself and others out of the area of danger.
Stand on the tread side of the tire. Always fill
the tires to the correct air pressure, and follow
the instructions in this manual for adding air or
servicing the tires.
WARNING
Do not weld the wheel or rim with the tire installed.
Welding with an explosive air/gas mixture can
ignite, causing serious injury or death, regardless of
whether the tire is inflated or deflated.
Removing the air or breaking the bead is not
adequate; you must completely remove the tire from
the rim before welding.
WARNING
An explosive separation of the tire and/or rim parts
can cause injury or death.
Have a qualified tire mechanic service the tire.
Checking the Tires and Wheels
Service Interval:
Before each use or daily
1.
Check each tire for embedded objects, separated plies,
missing tread, bulges, or a damaged bead, and replace
it, if necessary.
2.
Check each wheel for signs of unusual bending or
damage, and replace it, if necessary.
Maintaining the Air Pressure in the
Tires
Service Interval:
Every 50 hours
Important:
Maintain the air pressure in the tires at 310
kPa (45 psi).
1.
Measure the air pressure in the tires; if the tire pressure
is not at the recommended pressure, complete the rest
of this procedure.
Important:
Use an air hose with a remote shutoff
valve and a self-locking chuck.
Note:
Before you add air, ensure that the tire is
properly installed on the machine, or put the wheel in a
restraining device, such as a tire inflation cage.
2.
Remove the cap from the valve stem.
3.
Attach the self-locking chuck of the air hose to the
valve stem.
4.
When inflating the tire while it is mounted to the
machine, stand behind the tread of the tire.
Note:
Ensure that all persons are away from the side
of the tire before you start to add air.
5.
Open the remote shutoff valve to inflate the tire to the
specified pressure, then close the valve.
Important:
Do not inflate the tire more than the
recommended pressure.
6.
Remove the air chuck from the valve stem.
7.
Install the cap on the valve stem.
Maintaining the Tires and Wheels
Always have a qualified tire technician service the tires and
wheels of this machine. To prevent accidents, use a restraining
device (such as a tire inflation cage), the correct equipment,
and the correct procedure.
Important:
There are 2 different tire-tread pattern and
wheel combinations; the left-side tires and the right-side
tires are different. Ensure that the tread direction of the
tire and the valve stem in the wheel are correctly aligned
before installing the tire to the rim.
Figure 62
1.
Left-side tire
3.
Right-side tire
2.
Forward
4.
Valve stem
Torquing the Wheel Nuts
1.
Ensure that the mounting flange of the wheel is flush
against the mounting flange of the axle.
2.
Incrementally torque the wheel nuts for each wheel
as follows:
A.
Torque the all wheel nuts to 100 N-m (75 ft-lb) in
the sequence shown in Figure 63.
49
Summary of Contents for RT600
Page 71: ...Notes 71...