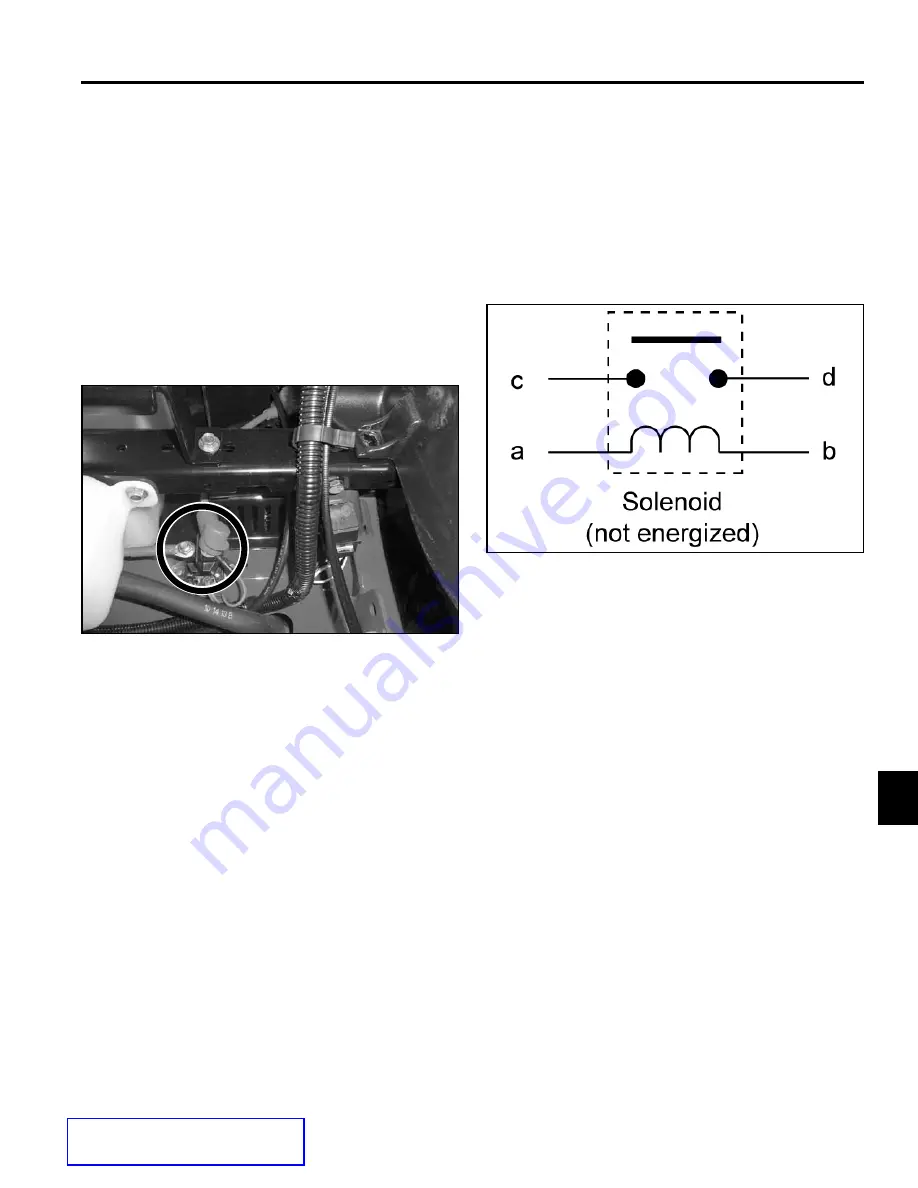
ELECTRICAL
7-9
Toro TITAN 2014 Service Manual
7
Starter Solenoid Testing (solenoid only)
1. Disconnect solenoid from the wiring harness.
2. With a multimeter (ohms setting), check to ensure
that terminals “c” and “d” are open (no continuity).
3. Apply +12 VDC to terminal “a” and ground terminal
“b”. Terminals “c” and “d” should now be closed
(continuity) (Fig. 127).
How It Works (solenoid only)
The solenoid has two primary parts. One, a coil of wire
is wrapped around an iron core. Whenever 12 volts is
applied to the coil, it becomes a magnet. The other part
is a bar type switch. Because it has a large contact area
with the contact terminals, it can easily handle the high
current loads required by the starter motor of the engine.
When 12 volts is applied to the coil, it becomes an elec-
tromagnet. This quickly pulls the contact bar toward the
contacts and closes the switch. When power is removed
from the coil, the spring loaded bar returns to its
“normally open” position. The solenoid closes and opens
the switch very quickly. This minimizes the “arcing” that
can damage other types of switches.
The ignition switch is protected because only a small
amount of current is needed to activate the coil.
Starter Solenoid & Starting System
Purpose
The solenoid’s purpose is a remote switch to connect
the battery to the starter motor on the engine when the
ignition switch is turned to “START”. The solenoid is
used to protect the ignition switch from the high current
drawn by the starter motor.
Location
The starter solenoid is located behind the operator’s
seat, near the fuse block (Fig. 126).
Fig. 126
PICT-3023
Fig. 127
xl solenoid
Summary of Contents for titan mx
Page 1: ...2014 TITAN ZX MX Service Manual Residential Products ...
Page 2: ......
Page 4: ...ABOUT THIS MANUAL THIS PAGE INTENTIONALLY LEFT BLANK ...
Page 10: ...SAFETY INFORMATION 1 2 Toro TITAN 2014 Service Manual 1 THIS PAGE INTENTIONALLY LEFT BLANK ...
Page 46: ...CHASSIS 3 26 Toro TITAN 2014 Service Manual 3 THIS PAGE INTENTIONALLY LEFT BLANK ...
Page 52: ...ENGINE 4 6 Toro TITAN 2014 Service Manual 4 THIS PAGE INTENTIONALLY LEFT BLANK ...
Page 84: ...MOWER DECK 6 18 Toro TITAN 2014 Service Manual 6 THIS PAGE INTENTIONALLY LEFT BLANK ...
Page 97: ...ELECTRICAL 7 13 Toro TITAN 2014 Service Manual 7 PTO Circuit Schematic Fig 131 PICT 2015 ...
Page 103: ...ELECTRICAL 7 19 Toro TITAN 2014 Service Manual 7 Fig 143 PICT 3020 Wire Harness View 1 of 3 ...
Page 104: ...ELECTRICAL 7 20 Toro TITAN 2014 Service Manual 7 Wire Harness View 2 of 3 Fig 144 PICT 3021 ...
Page 105: ...ELECTRICAL 7 21 Toro TITAN 2014 Service Manual 7 Fig 145 PICT 3022 Wire Harness View 3 of 3 ...
Page 106: ...ELECTRICAL 7 22 Toro TITAN 2014 Service Manual 7 THIS PAGE INTENTIONALLY LEFT BLANK ...
Page 107: ......
Page 108: ...2014 TITAN ZX MX Service Manual Form Number 492 9339 ...