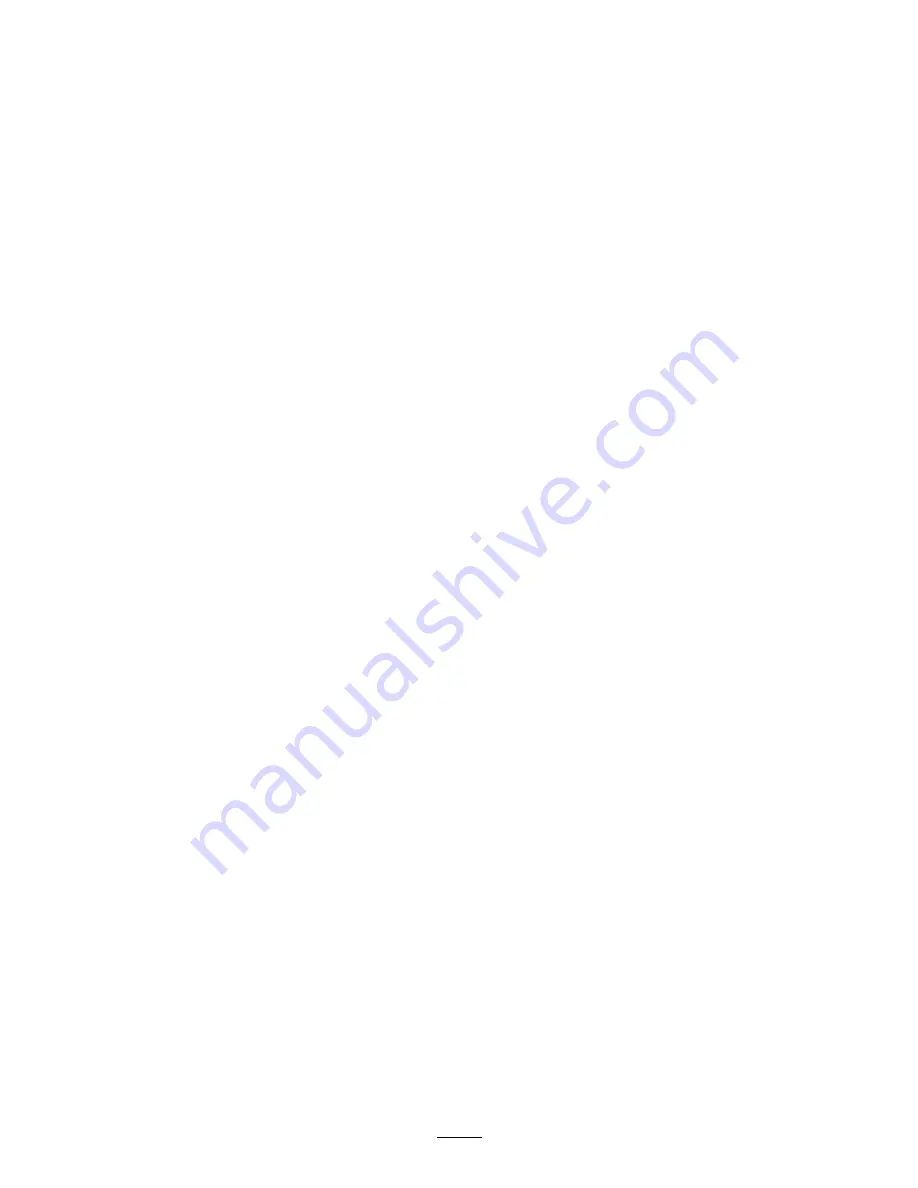
3.
Inspect the LPG tank and the fuel-connection
joint for leaks. Use the following procedure
below to detect leaks:
A.
Apply an approved leak detector solution,
obtained from a trained and qualified LPG
distributor, or a thick non-ammonia soapy
water solution (50% non-ammonia soap
and 50% water).
Important:
A leak detector solution that
contains ammonia causes the fittings to
corrode and leak.
B.
Using a small brush or spray bottle, apply
the solution around all the fittings of the
LPG tank and the fuel-connection joint.
C.
Slowly open the gas valve a half-turn.
•
If you detect bubbles, the joint or fitting
has a leak. Shut off the valve, tighten
the leaking connection, and slowly open
the valve again. If bubbles still appear,
do not
use the tank. If it is safe to do
so, remove the tank from your mower;
otherwise, contact trained and qualified
personnel immediately.
•
If you do not detect bubbles, you may
use the LPG tank.
Inspecting the System Weekly
1.
Check the LPG hoses, regulator, and
connections for damage or deterioration.
2.
Check the LPG hoses, regulator, and
connections for leaks at all joints using the same
method as described in
With Each Tank Change (page 48)
.
3.
Follow all the inspection checks as specified in
Inspecting the System Before Each Use (page
48)
and
Inspecting the System With Each Tank
.
Tank Requalification
•
USDOT (United States Department of
Transportation) regulations require LPG tanks to
be inspected, requalified, and marked within 12
years of the manufacture date and on a regular
basis thereafter. Typically this occurs when the
tank is refilled; contact a trained and qualified LPG
tank provider for more details.
•
Do not fill the LPG tank if it is beyond the
requalification period.
•
Do not fill damaged or rusted LPG tanks.
Servicing the Electronic
Fuel-Injection System
This machine contains an electronic fuel-injection
system. It controls the fuel flow under different
operating conditions.
The electronic-control unit (ECU) continuously
monitors the operation of the EFI system.
If a problem or fault within the system is detected, the
malfunction-indicator light (MIL) illuminates. The MIL
is the red light located in the right console panel.
Once the MIL illuminates, make initial troubleshooting
checks; refer to the MIL section under
(page 76)
.
If these checks do not correct the problem, further
diagnosis and servicing by an Authorized Service
Dealer is necessary.
49
Summary of Contents for Z Master Professional 5000 Series
Page 13: ...decal136 5508 136 5508 1 Belt routing 13...
Page 78: ...Schematics g021490 Wire Diagram Rev A 78...
Page 79: ...Notes...