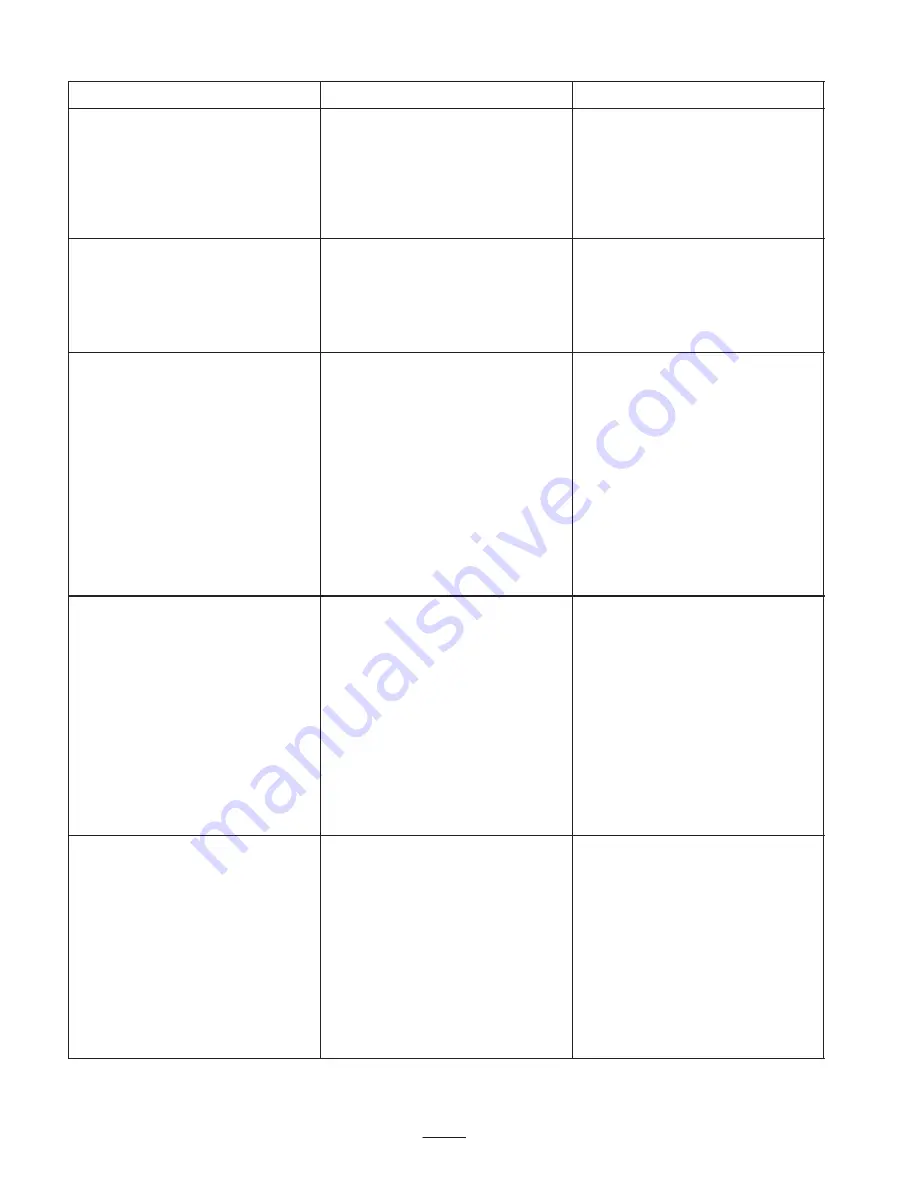
54
Problem
Corrective Action
Possible Causes
5. The crankcase oil level is
incorrect.
5. Fill or drain to the full mark.
6. The fuel mixture is lean.
6. Contact your Authorized
Service Dealer.
7. Excessive loading.
7. Reduce load; use lower ground
speed.
Machine does not drive.
1. Traction belt is worn, loose or
broken.
1. Contact Authorized Service
Dealer.
2. Traction belt is off pulley.
2. Contact Authorized Service
Dealer.
3. Hydro fluid level low.
3. Add hydro fluid to reservoir.
Abnormal vibration.
1. Cutting blade(s) is/are bent or
unbalanced.
1. Install new cutting blade(s).
2. Blade mounting bolt is loose.
2. Tighten blade mounting bolt.
3. Engine mounting bolts are
loose.
3. Tighten engine mounting bolts.
4. Loose engine pulley, idler
pulley, or blade pulley.
4. Tighten the appropriate pulley.
5. Engine pulley is damaged.
5. Contact Authorized Service
Dealer.
6. Blade spindle bent.
6. Contact Authorized Service
Dealer.
Uneven cutting height.
1. Blade(s) not sharp.
1. Sharpen blade(s).
g
g
2. Cutting blade(s) is/are bent.
2. Install new cutting blade(s).
3. Mower is not level.
3. Level mower from side-to-side
and front-to-rear.
4. Gage wheel not set correctly.
4. Adjust gage wheel height.
5. Underside of mower is dirty.
5. Clean the underside of the
mower.
6. Tire pressure is incorrect.
6. Adjust tire pressure.
7. Blade spindle bent.
7. Contact Authorized Service
Dealer.
Blades do not rotate.
1. Drive belt is worn, loose or
broken.
1. Install new drive belt.
2. Drive belt is off pulley.
2. Install drive belt and check
adjusting shafts and belt guides
for correct position.
3. Deck belt is worn, loose or
broken.
3. Install new deck belt.
4. Deck belt is off pulley.
4. Install deck pulley and check
the idler pulley, idler arm and
spring for correct position and
function.
Summary of Contents for Z287L Z Master
Page 6: ...6 Slope Chart ...
Page 7: ...7 ...
Page 12: ...12 103 2433 106 6571 106 6570 ...
Page 55: ...55 ...