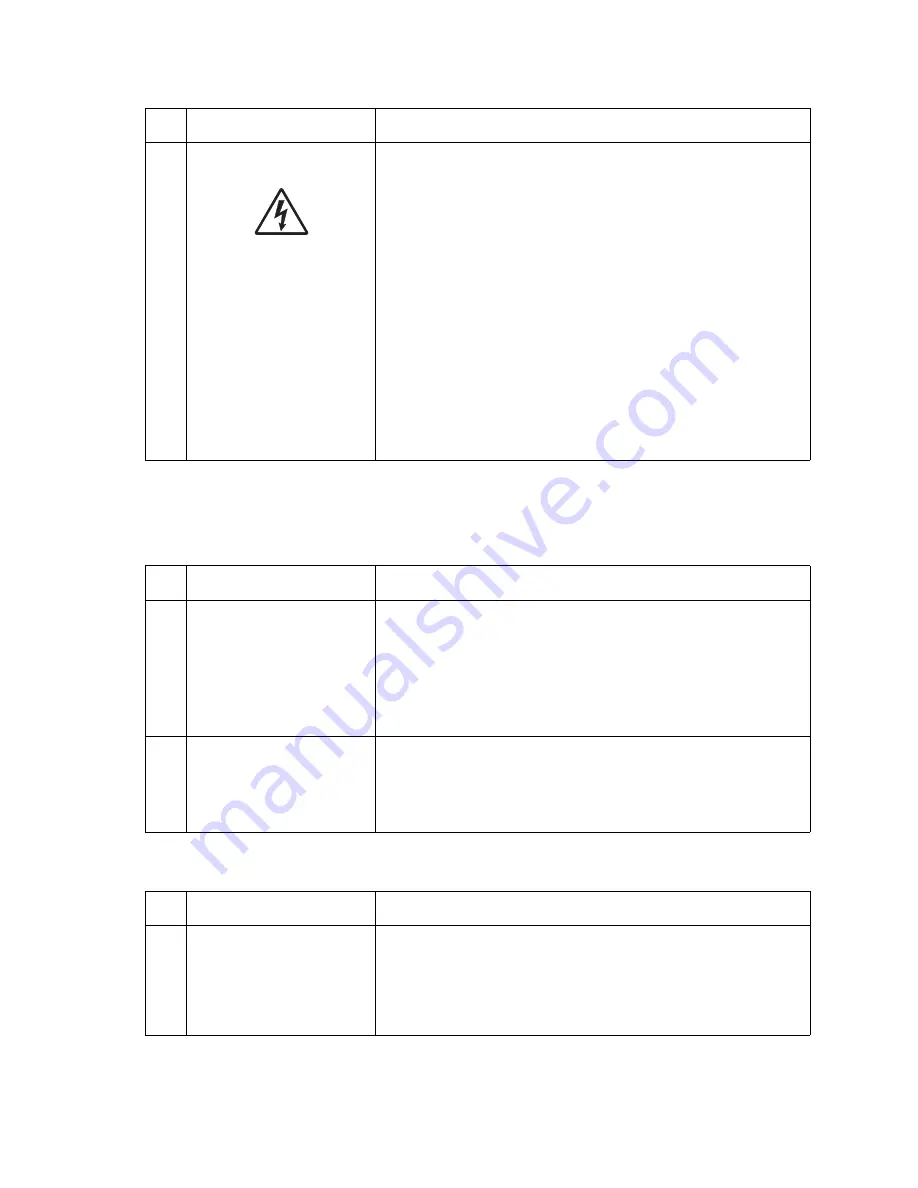
2-96
Service Manual
24
x.xx
Paper Jam
displays, paper jammed over the pass thru sensor
Where
x
=the printer displays the value of
x
for the paper tray where the error occurs. For example: 242.xx is a
Paper Jam Tray 2
Tray
x
Paper Low
displays when tray
x
is full or has adequate paper in the tray
4
High-capacity feeder option
control board
Check the voltage on J8-1 (green). The voltage me24 V dc.
If incorrect, check the autoconnect system for any problems.
+24 V dc must come from the base printer through the autoconnect
system to the high-capacity input for the high-capacity feeder to be
recognized. If the voltage is correct, check the voltages at J11-3(red)
and J11-4(red). The voltages m24 V dc. If correct, replace
the high-capacity feeder option system board. If incorrect, disconnect
J8 from the system board and measure the voltages again. If
incorrect, check the LVPS cable and the AC internal wiring from the
input appliance receptacle. If incorrect, replace as necessary. If
correct, replace the LVPS. If the voltages are correct, check the
stepper motor for shorts from the motor housing to each pin on the
motor connector. If you find a short between any pin and the motor
housing, replace the motor assembly. If no shorts are found, replace
the high-capacity feeder option control board.
Check the voltage at J9-1 (light blue). The voltage measures
approxi24 V dc. If incorrect, disconnect the cable at J9 and
check the voltage again. If the voltage continues to be incorrect,
replace the high-capacity feeder option system board. If the voltage
measures correctly, check the cable. If the cable is damaged, replace
as necessary. If no problem is found with the cable, replace the high-
capacity feeder option control board.
FRU
Action
1
Pass thru sensor and flag
assembly
The tray
x
option system board did not detect a piece of paper
actuating the pass thru sensor. Remove any jammed sheets of paper
from the printer and check the pass thru sensor and flag for proper
operation by running the appropriate Tray Sensor Test from the
diagnostics menu. If the test fails, check the sensor for correct
installation and the flag for proper operation. Also check the sensor
cable to make sure it is correctly connected to the option system
board. If incorrect, replace the tray
x
option pass thru sensor
assembly.
2
Power takeoff shaft and
spring, bevel gear, feed roll
gear, drive roll assembly,
wear plate, drive shaft
bearings, and skewed
backup roller
Check these parts for signs of broken or damaged parts,
contamination on the drive rollers or wear plate and wear or damage
to the drive shaft bearings. Check the drive roll assembly and skewed
backup roller for wear, slick spots, material buildup, and oil or grease
on the rollers. Also check for proper operation of the paper aligning
assembly. Repair or replace parts as necessary.
FRU
Action
1
Paper low switch
Paper low switch cable
High-capacity feeder Input
system board
Run the sensor diagnostics for tray
x
(
x
=the number that represents
the high-capacity input tray). If the test fails, disconnect the paper low
switch cable from J3 on the high-capacity system board. Short pins 1
and 2 together while observing the sensor test on the display. If the
display does not change, replace the high-capacity feeder system
board. If the display changes check the continuity of the switch. If
incorrect, replace the switch. If correct, replace the switch cable.
FRU
Action
Summary of Contents for e-STUDIO500P
Page 1: ...PRINTER P N 12G9609 e STUDIO500P ...
Page 10: ...x Service Manual ...
Page 15: ...Laser notices xv Japanese Laser Notice ...
Page 16: ...xvi Service Manual Korean Laser Notice ...
Page 43: ...Diagnostic information 2 7 ...
Page 159: ...Diagnostic information 2 123 ...
Page 160: ...2 124 Service Manual ...
Page 161: ...Diagnostic information 2 125 ...
Page 181: ...Diagnostic aids 3 17 ...
Page 297: ...5 12 Service Manual ...
Page 298: ...Connector locations and connections 5 13 ...
Page 299: ...5 14 Service Manual ...
Page 301: ...6 2 Service Manual ...
Page 303: ...7 2 Service Manual Assembly 1 Covers ...
Page 305: ...7 4 Service Manual Assembly 2 Frame 1 ...
Page 307: ...7 6 Service Manual Assembly 3 Frame 2 ...
Page 309: ...7 8 Service Manual Assembly 4 Frame 3 ...
Page 311: ...7 10 Service Manual Assembly 5 Printhead ...
Page 313: ...7 12 Service Manual Assembly 6 Paper feed autocompensator ...
Page 315: ...7 14 Service Manual 4061 xx0 Assembly 7 Paper feed multipurpose feeder ...
Page 317: ...7 16 Service Manual Assembly 8 Paper feed alignment ...
Page 319: ...Page 7 19 has been removed from this document intentionally 7 18 Service Manual ...
Page 320: ...7 20 Service Manual Assembly 10 Integrated 500 sheet paper tray ...
Page 322: ...7 22 Service Manual Assembly 11 Drives Main drive and developer drive ...
Page 324: ...7 24 Service Manual Assembly 12 Hot roll fuser ...
Page 326: ...7 26 Service Manual Assembly 13 Transfer charging ...
Page 328: ...7 28 Service Manual Assembly 14 Electronics power supplies ...
Page 330: ...7 30 Service Manual Note ...
Page 332: ...7 32 Service Manual Assembly 16 Electronics shields ...
Page 336: ...7 36 Service Manual Assembly 19 Cabling diagrams 3 ...
Page 338: ...7 38 Service Manual Assembly 20 Cabling diagrams 4 ...
Page 340: ...7 40 Service Manual Assembly 21 Cabling diagrams 5 ...
Page 342: ...7 42 S ervice Manual THE FOLLOWING PAGE 7 43 HAS BEEN OMITTED FROM THIS MANUAL INTENTIONALLY ...
Page 347: ...7 48 S ervice Manual Pages 7 49 through 7 57 of this manual have been omitted intentionally ...
Page 348: ...7 58 Service Manual Assembly 35 High capacity feeder 1 ...
Page 350: ...7 60 Service Manual Assembly 36 High capacity feeder 2 ...
Page 354: ...7 64 S ervice Manual Pages 7 65 thru 7 70 ofthis manual were omitted intentionally ...
Page 362: ...I 8 Service Manual ...
Page 370: ...I 16 Service Manual ...