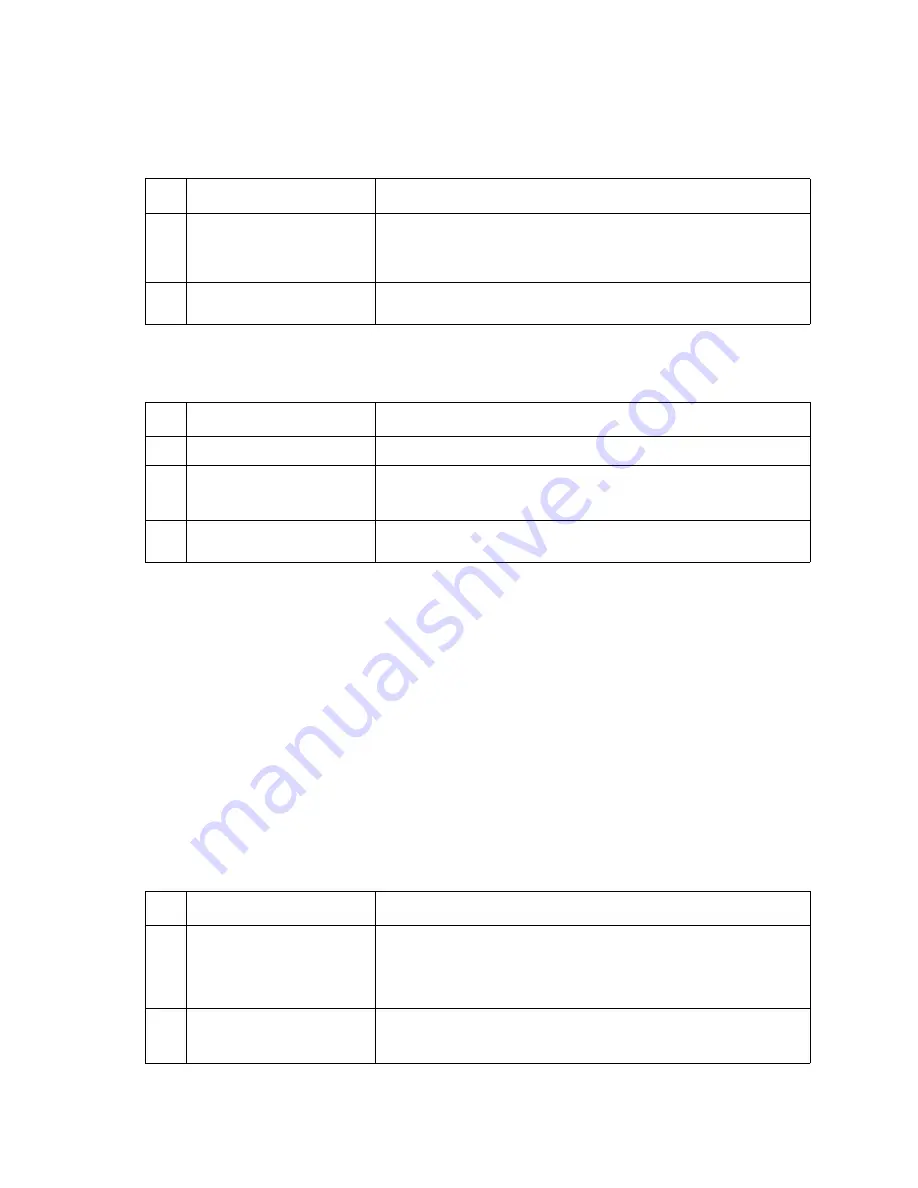
2-112
Service Manual
Paper feed service check
If you have a 936 Transport Motor Error go to
“Main drive service check” on page 2-105
.
Autocompensator fails to feed paper. Failures occur randomly throughout the stack
of paper
Paper feed failures occur only near the top of the stack of paper
The most common cause of this problem is paper curl. Remove the paper from tray
x
and check for the natural
curvature in the paper. Reinstall the paper in the correct manner. If the problem persists, it may be necessary to
reduce the stack height. Replace both pick rolls if the paper appears to be flat in the tray but there is still a
problem.
Failures occur mainly near the bottom of the stack of paper
The autocompensator pick arm may not be coming down far enough to allow the pick rolls to properly contact
the paper. Also the autocompensator motor may be failing. If this problem continues replace the
autocompensator assembly.
Double feeding paper
Note:
If double feeding paper occurs mostly from the bottom of the stack, check for missing or damaged
restraint pads in the tray.
FRU
Action
1
Alignment assembly
Check to ensure the alignment assembly is correctly attached to the
left side frame and the mounting screws are tight. Check the
alignment assembly for worn rollers, contaminated rollers, or binds.
Replace the alignment assembly if any problem is found.
2
Inner deflector
Check the inner paper deflector for correct installation. If the deflector
is bowed or not fitting correctly, replace the deflector.
FRU
Action
1
Pass thru sensor
Check the pass thru sensor for correct installation and operation.
2
Autocompensator
assembly
The autocompensator pick roll shaft assembly is not providing
enough torque if the pick rollers are not picking the paper correctly.
Replace the autocompensator assembly.
3
Wear strips in tray
x
problem is found.
Check the wear strips for excessive wear, scratches, or rough spots.
Replace the wear strips if a problem is found.
FRU
Action
1
Paper
Paper is usually the primary cause of a double feeding paper
problem. Flex the paper before placing the paper in the tray. Edge-
welded paper is the most common cause of double feeding. Loading
the paper in the tray in different locations and directions and using
rough paper and short grain paper also causes double feeding.
2
Autocompensator
Make sure the counterbalance spring is not missing, loose, or broken
at the top of the autocompensator arm assembly. If you find a
problem, replace the autocompensator assembly.
Summary of Contents for e-STUDIO500P
Page 1: ...PRINTER P N 12G9609 e STUDIO500P ...
Page 10: ...x Service Manual ...
Page 15: ...Laser notices xv Japanese Laser Notice ...
Page 16: ...xvi Service Manual Korean Laser Notice ...
Page 43: ...Diagnostic information 2 7 ...
Page 159: ...Diagnostic information 2 123 ...
Page 160: ...2 124 Service Manual ...
Page 161: ...Diagnostic information 2 125 ...
Page 181: ...Diagnostic aids 3 17 ...
Page 297: ...5 12 Service Manual ...
Page 298: ...Connector locations and connections 5 13 ...
Page 299: ...5 14 Service Manual ...
Page 301: ...6 2 Service Manual ...
Page 303: ...7 2 Service Manual Assembly 1 Covers ...
Page 305: ...7 4 Service Manual Assembly 2 Frame 1 ...
Page 307: ...7 6 Service Manual Assembly 3 Frame 2 ...
Page 309: ...7 8 Service Manual Assembly 4 Frame 3 ...
Page 311: ...7 10 Service Manual Assembly 5 Printhead ...
Page 313: ...7 12 Service Manual Assembly 6 Paper feed autocompensator ...
Page 315: ...7 14 Service Manual 4061 xx0 Assembly 7 Paper feed multipurpose feeder ...
Page 317: ...7 16 Service Manual Assembly 8 Paper feed alignment ...
Page 319: ...Page 7 19 has been removed from this document intentionally 7 18 Service Manual ...
Page 320: ...7 20 Service Manual Assembly 10 Integrated 500 sheet paper tray ...
Page 322: ...7 22 Service Manual Assembly 11 Drives Main drive and developer drive ...
Page 324: ...7 24 Service Manual Assembly 12 Hot roll fuser ...
Page 326: ...7 26 Service Manual Assembly 13 Transfer charging ...
Page 328: ...7 28 Service Manual Assembly 14 Electronics power supplies ...
Page 330: ...7 30 Service Manual Note ...
Page 332: ...7 32 Service Manual Assembly 16 Electronics shields ...
Page 336: ...7 36 Service Manual Assembly 19 Cabling diagrams 3 ...
Page 338: ...7 38 Service Manual Assembly 20 Cabling diagrams 4 ...
Page 340: ...7 40 Service Manual Assembly 21 Cabling diagrams 5 ...
Page 342: ...7 42 S ervice Manual THE FOLLOWING PAGE 7 43 HAS BEEN OMITTED FROM THIS MANUAL INTENTIONALLY ...
Page 347: ...7 48 S ervice Manual Pages 7 49 through 7 57 of this manual have been omitted intentionally ...
Page 348: ...7 58 Service Manual Assembly 35 High capacity feeder 1 ...
Page 350: ...7 60 Service Manual Assembly 36 High capacity feeder 2 ...
Page 354: ...7 64 S ervice Manual Pages 7 65 thru 7 70 ofthis manual were omitted intentionally ...
Page 362: ...I 8 Service Manual ...
Page 370: ...I 16 Service Manual ...