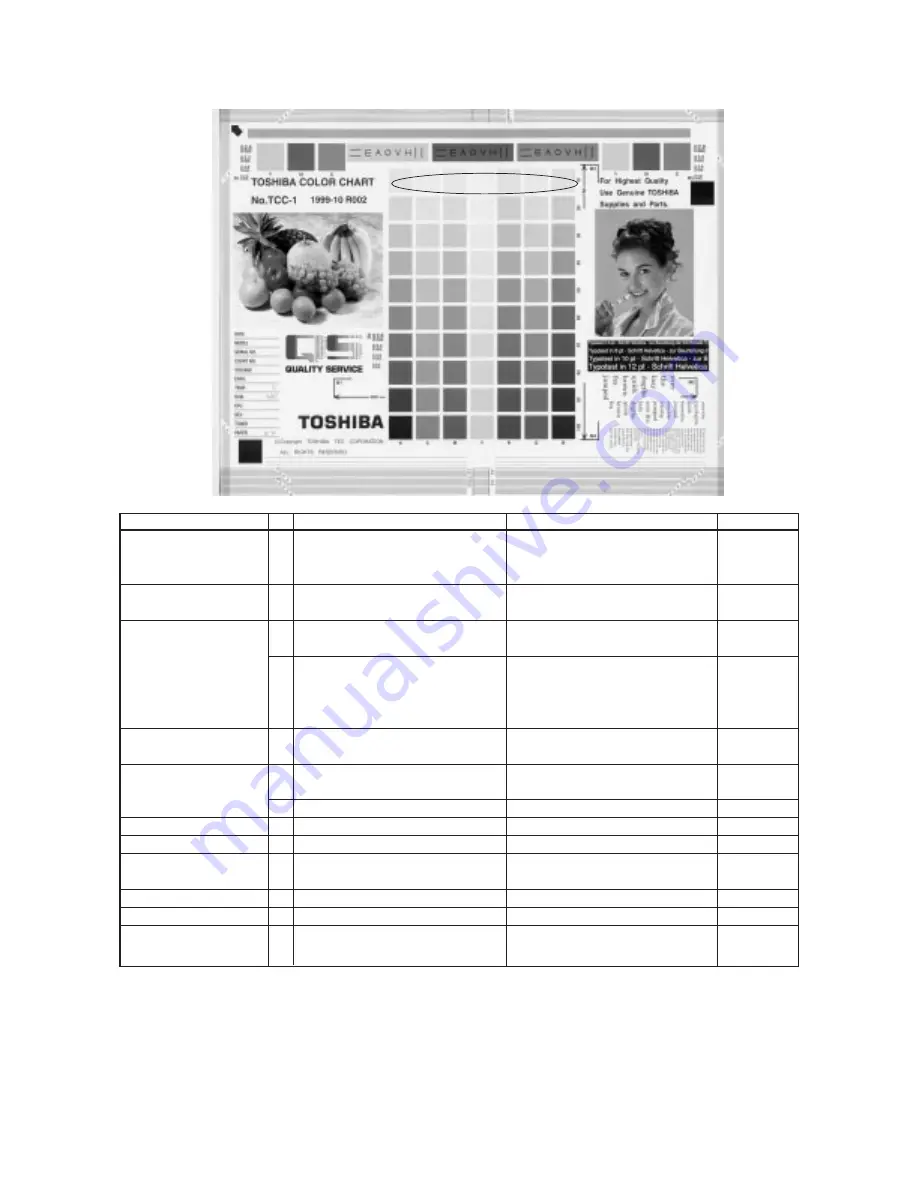
FC-22
TROUBLESHOOTING
4 - 60
January 2000 © TOSHIBA TEC
(4) Background Fogging
Note:
If the main charger and developer bias outputs seem to be abnormal, replace the main high-voltage transformer of the color likely
to be abnormal with another transformer of another color likely to be normal, and then, output the chart again.
If the same color remains abnormal, check if there is any disconnection of harness between the LGC board and the main high-
voltage transformer, disconnection of high-voltage harness, the power supply defect, or stain on the main charger wire.
If the color changes as the result of replacing the main high-voltage transformer, this fogging trouble is caused by the main high-
voltage transformer defect. Therefore, replace the main high-voltage transformer of the abnormal color with new one.
After this checking, return the other main high-voltage transformer back to the original color position.
Cause/Defect area
Step
Check items
Measures
Remarks
Density reproduction
1
Image density reproduction defect
Perform automatic adjustment of
Go to step 5
gamma correction.
If defects
occur.
Printer
2
Check printer image.
Output test print image (04-231) for
each color and check it.
Parameter adjustment
3
Check image processing parameters.
Check the value of offset amount of
value
processing background.
4
Adjust image processing
While checking the above encircled
parameters.
image, remove background fog by
adjusting offset amount of processing
background.
Scanner stain
5
Is the original glass or mirrors
Clean them.
or lens filter dirty?
Auto-toner
6
Is the auto-toner sensor normal?
Check operation of auto-toner sensor
and re-adjust.
7
Is the toner supply operating constantly?
Inspect motor and circuits.
Main charger output
8
Is the main charger output normal?
Check circuits. (Note)
Developer bias
9
Is the developer bias proper?
Check circuits. (Note)
Developer unit
10 Is the contact between the drum
Adjust doctor-to-sleeve gap and pole
and developer material right?
position.
Developer material
11 Is the developer's life finished?
Replace developer material.
Drum cleaning blade
12 Is it cleaned properly?
Inspect drum cleaning blade pressure.
Toner dusting
13 Is toner accumulated on the seals of
Remove toner and clean.
the developer unit?
Summary of Contents for FC22
Page 115: ...FC 22 PREVENTIVE MAINTENANCE 2 8 January 2000 TOSHIBA TEC Front side drive system 47 20 ...
Page 121: ......
Page 235: ...January 2000 TOSHIBA TEC 5 29 FC 22 FIRMWARE UPDATING ...
Page 237: ...FC 22 SERVICE HANDBOOK 6 WIRE HARNESS CONNECTION DIAGRAMS 6 2 DC Wire Harness ...
Page 238: ...FC 22 WIREHARNESS CONNECTION DIAGRAMS 6 3 January 20000 TOSHIBA TEC ...