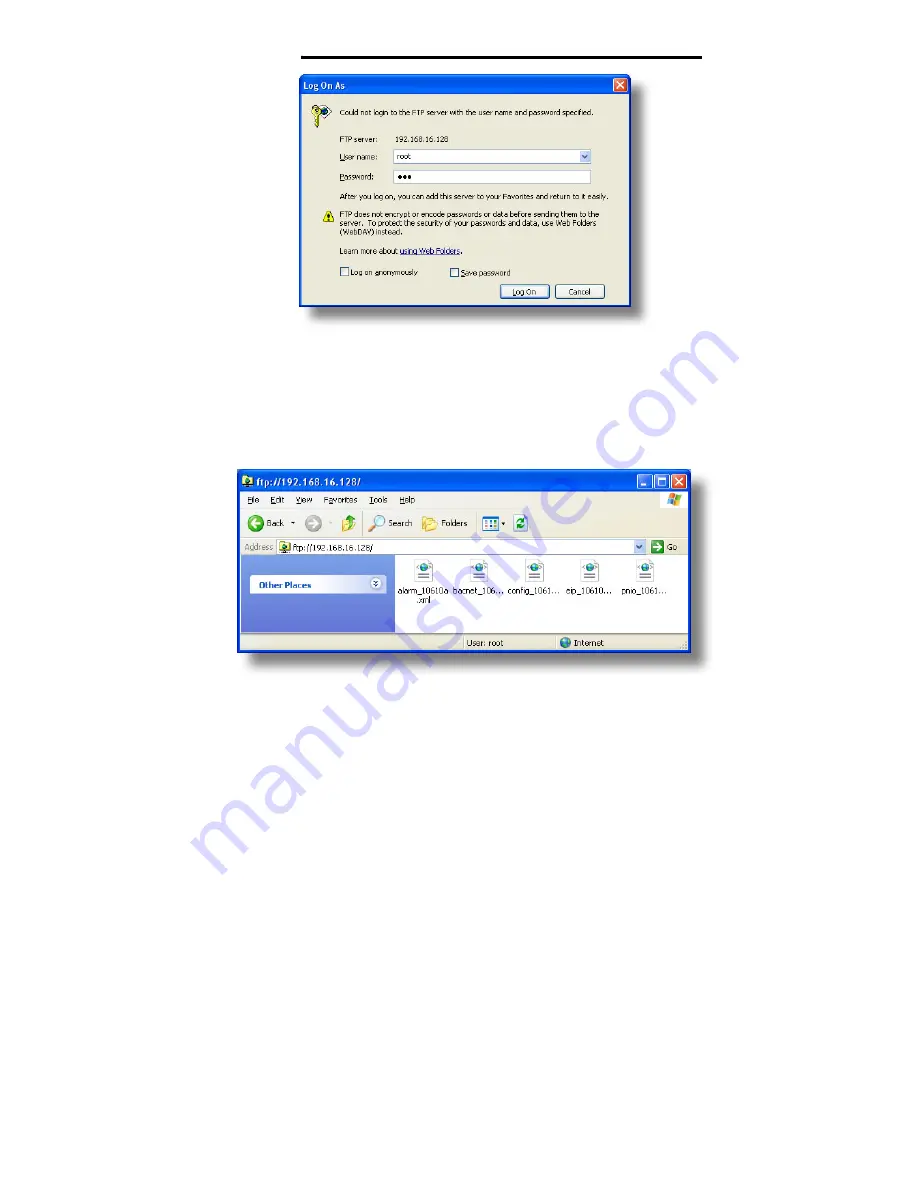
55
ICC
Figure 55: FTP Authentication
Windows Explorer will then display the filesystem’s contents (refer to Figure
56.) You can now perform normal file manipulation actions on the available
files (cut, copy, paste, open, rename, drag-and-drop transfers etc.) in the same
manner as though you were manipulating any traditional file stored on your
computer’s hard drive.
Figure 56: File Access with Windows Explorer