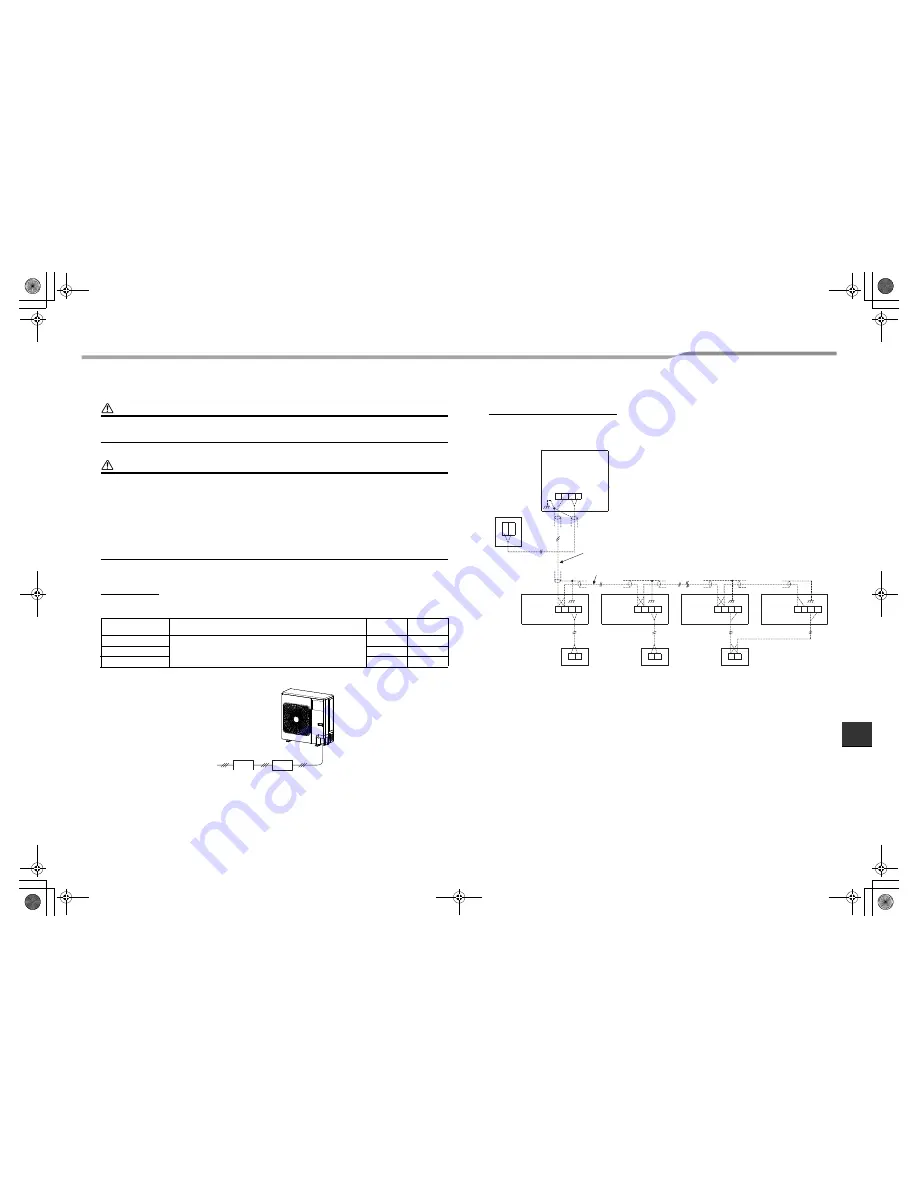
Installation Manual
– 16 –
EN
6
Electric Wiring
WARNING
The appliance shall be installed in accordance with national wiring regulations.
Capacity shortages of the power circuit or an incomplete installation may cause an electric shock or fire.
CAUTION
• Perform wiring of power supply complying with the rules and regulations of the local electric company.
• Do not connect 220 V power to the terminal blocks for control cables (U1, U2, U3, U4); otherwise, the unit may
break down.
• Be sure that electric wiring does not come into contact with high-temperature parts of piping; otherwise, the coating
of cables may melt and cause an accident.
• After connecting wires to the terminal block, take off the traps and fix the wires with cord clamps.
• Do not conduct power to indoor units until vacuuming of the refrigerant pipes has finished.
• For the wiring of power to indoor units and that between indoor and outdoor units, follow the instructions in the
installation manual of each indoor unit.
Power wiring selection
Standard model
MCA: Maximum Circuit Amps
MOCP: Maximum Overcurrent Protection (Amps)
Model
Power Supply
Nominal Voltage, Phase and frequency
MCA
(A)
MOCP
(A)
MCY-
MAP0401
*
220–240 V ~ 50 Hz
27.0
32.0
MCY-MAP0501*
2
8
.0
32
.0
Circuit breaker
(Earth leakage breaker)
Main switch
(Fuse)
Specifications for communication wiring
Design of communication wiring
Summary of communication wiring
Communication wiring and central control wiring use 2-core non-polarity wires.
Use 2-core shield wires to prevent noise trouble.
In this case, for the system grounding, close (connect) the end of shield wires, and isolate the end of terminal.
Use 2-core non-polarity wire for remote controller. (A, B terminals)
Use 2-core non-polarity wire for wiring of group control. (A, B terminals)
U1 U2 U3 U4
U1 U2
U3 U4
U1 U2 A B
2
U
B
A
U1
U2
U1
A
2
U
B
U1
A B
B
A
B
A
B
A
Outdoor unit
Central controller
Communication wiring between indoor and outdoor units
(Shield wire)
Communication wiring between indoor units (Shield wire)
Indoor unit
Indoor unit
Indoor unit
Indoor unit
Remote controller
Remote controller
Remote controller
(Group control)
EN-31
EN-32
2FAN_IM_DB04905901-00.book Page 16 Friday, October 24, 2014 3:19 PM
MCY-MAP0601*
28.0
32
.0
220–2
3
0 V ~
6
0 Hz
Summary of Contents for MCY-MAP0401TP Series
Page 32: ......