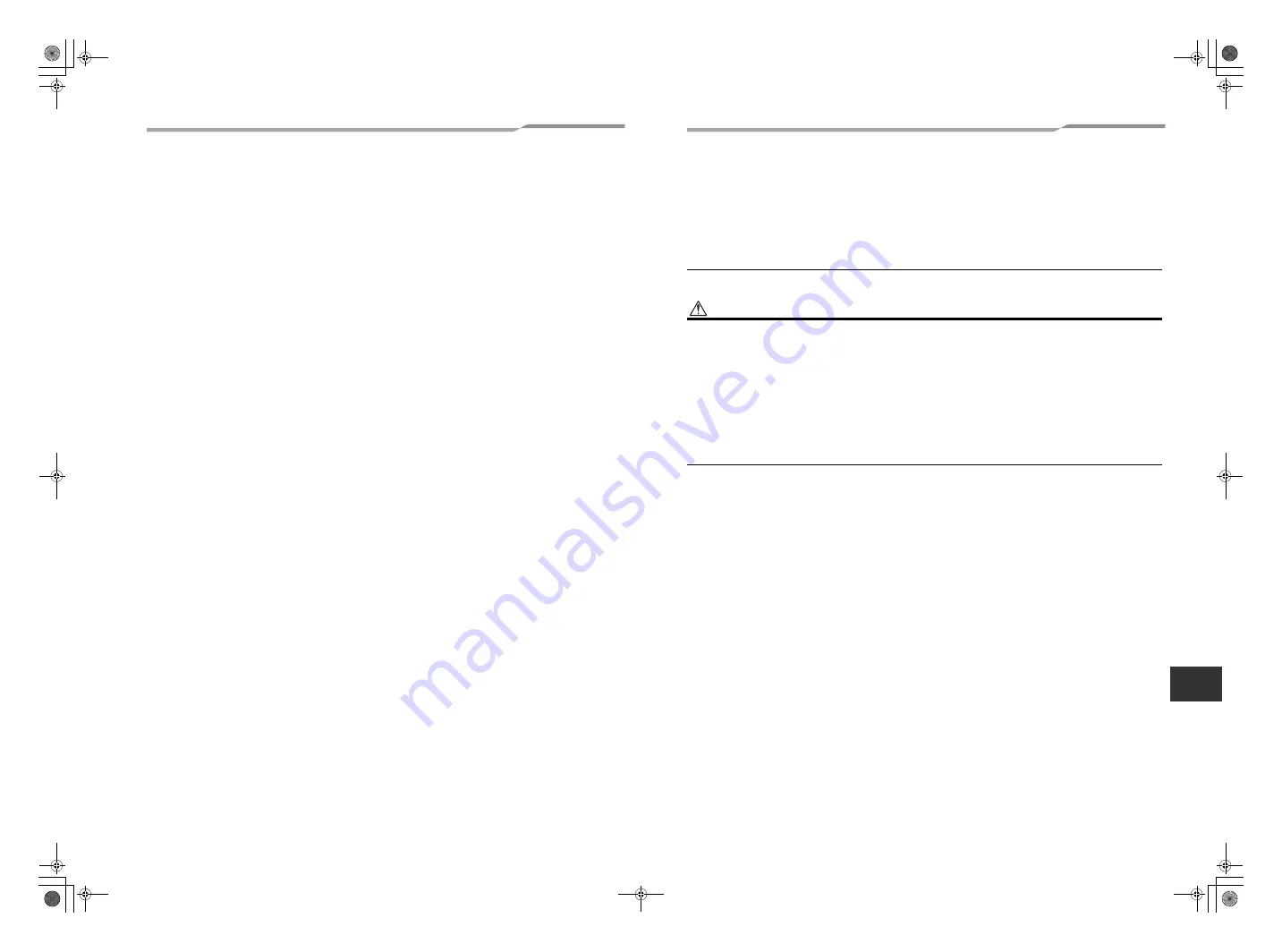
– 2 –
Outdoor Unit
Installation Manual
EN
Outdoor Unit
Installation Manual
Refrigerant piping
• Install the refrigerant pipe securely during the installation work before operating the air conditioner. If the compressor is
operated with the valve open and without refrigerant pipe, the compressor sucks air and the refrigeration cycles is over
pressurized, which may cause a injury.
• Tighten the flare nut with a torque wrench in the specified manner. Excessive tighten of the flare nut may cause a crack in
the flare nut after a long period, which may result in refrigerant leakage.
• Ventilate the air if the refrigerant gas leaks during installation. If the leaked refrigerant gas comes into contact with fire, toxic
gas may be produced.
• After the installation work, confirm that refrigerant gas does not leak. If refrigerant gas leaks into the room and flows near a
fire source, such as a cooking range, noxious gas may be generated.
• When the air conditioner has been installed or relocated, follow the instructions in the Installation Manual and purge the air
completely so that no gases other than the refrigerant will be mixed in the refrigerating cycle. Failure to purge the air
completely may cause the air conditioner to malfunction.
• Nitrogen gas must be used for the airtight test.
• The charge hose must be connected in such a way that it is not slack.
• If refrigerant gas has leaked during the installation work, ventilate the room immediately. If the leaked refrigerant gas comes
in contact with fire, noxious gas may be generated.
Electrical wiring
• Only a qualified installer(*1) or qualified service person(*1) is allowed to carry out the electrical work of the air conditioner.
Under no circumstances must this work be done by an unqualified individual since failure to carry out the work properly may
result in electric shocks and / or electrical leaks.
• When connecting the electrical wires, repairing the electrical parts or undertaking other electrical jobs, wear gloves to
provide protection for electricians and from heat, insulating shoes and clothing to provide protection from electric shocks.
Failure to wear this protective gear may result in electric shocks.
• When executing address setting, test run, or troubleshooting through the checking window on the electrical control box, put
on insulated heat-proof gloves, insulated shoes and other clothing to provide protection from electric shock. Otherwise you
may receive an electric shock.
• Use wiring that meets the specifications in the Installation Manual and the stipulations in the local regulations and laws. Use
of wiring which does not meet the specifications may give rise to electric shocks, electrical leakage, smoking and / or a fire.
• Check that the product is properly earthed. (grounding work)
Incomplete earthing may cause electric shock.
• Do not connect the earth line to a gas pipe, water pipe, lightning conductor, or a telephone earth line.
• After completing the repair or relocation work, check that the ground wires are connected properly.
• Install a circuit breaker that meets the specifications in the installation manual and the stipulations in the local regulations
and laws.
• Install the circuit breaker where it can be easily accessed by the agent.
• When installing the circuit breaker outdoors, install one which is designed to be used outdoors.
• Under no circumstances must the power cable be extended. Connection trouble in the places where the cable is extended
may give rise to smoking and / or a fire.
• Electrical wiring work shall be conducted according to law and regulation in the community and installation manual.
Failure to do so may result in electrocution or short circuit.
• Do not supply power from the power terminal block equipped on the outdoor unit to another outdoor unit. Capacity overflow
may occur on the terminal block and may result in fire.
• When carrying out electric connection, use the wire specified in the Installation Manual and connect and fix the wires
securely to prevent them applying external force to the terminals. Improper connection or fixing may result in fire.
Test run
• Before operating the air conditioner after having completed the work, check that the electrical control box cover of the indoor
unit and service panel of the outdoor unit are closed, and set the circuit breaker to the ON position. You may receive an
electric shock if the power is turned on without first conducting these checks.
• When you have noticed that some kind of trouble (such as when an error display has appeared, there is a smell of burning,
abnormal sounds are heard, the air conditioner fails to cool or heat or water is leaking) has occurred in the air conditioner,
do not touch the air conditioner yourself but set the circuit breaker to the OFF position, and contact a qualified service
person. Take steps to ensure that the power will not be turned on (by marking “out of service” near the circuit breaker, for
instance) until qualified service person arrives. Continuing to use the air conditioner in the trouble status may cause
mechanical problems to escalate or result in electric shocks or other failure.
• After the work has finished, be sure to use an insulation tester set (500 V Megger) to check the resistance is 2 M
or more
between the charge section and the non-charge metal section (Earth section). If the resistance value is low, a disaster such
as a leak or electric shock is caused at user’s side.
• Upon completion of the installation work, check for refrigerant leaks and check the insulation resistance and water drainage.
Then conduct a test run to check that the air conditioner is operating properly.
Explanations given to user
• Upon completion of the installation work, tell the user where the circuit breaker is located. If the user does not know where
the circuit breaker is, he or she will not be able to turn it off in the event that trouble has occurred in the air conditioner.
• If you have discovered that the fan grille is damaged, do not approach the outdoor unit but set the circuit breaker to the OFF
position, and contact a qualified service person(*1) to have the repairs done. Do not set the circuit breaker to the ON position
until the repairs are completed.
• After the installation work, follow the Owner’s Manual to explain to the customer how to use and maintain the unit.
Relocation
• Only a qualified installer(*1) or qualified service person(*1) is allowed to relocate the air conditioner. It is dangerous for the
air conditioner to be relocated by an unqualified individual since a fire, electric shocks, injury, water leakage, noise and / or
vibration may result.
• When carrying out the pump-down work shut down the compressor before disconnecting the refrigerant pipe. Disconnecting
the refrigerant pipe with the service valve left open and the compressor still operating will cause air or other gas to be sucked
in, raising the pressure inside the refrigeration cycle to an abnormally high level, and possibly resulting in rupture, injury or
other trouble.
• Never recover the refrigerant into the outdoor unit. Be sure to use a refrigerant recovery machine to recover the refrigerant
when moving or repairing. It is impossible to recover the refrigerant into the outdoor unit. Refrigerant recovery into the
outdoor unit may result in serious accidents such as explosion of the unit, injury or other accidents.
(*1) Refer to the “Definition of Qualified Installer or Qualified Service Person.”
CAUTION
New refrigerant air conditioner installation
•
This air conditioner adopts the new HFC refrigerant (R410A) which does not destroy ozone layer.
• The characteristics of R410A refrigerant are; easy to absorb water, oxidizing membrane or oil, and its pressure is approx.
1.6 times higher than that of refrigerant R22. Accompanied with the new refrigerant, refrigerating oil has also been changed.
Therefore, during installation work, be sure that water, dust, former refrigerant, or refrigerating oil does not enter the
refrigerating cycle.
• To prevent charging an incorrect refrigerant and refrigerating oil, the sizes of connecting sections of charging port of the
main unit and installation tools are changed from those for the conventional refrigerant.
• Accordingly the exclusive tools are required for the new refrigerant (R410A).
• For connecting pipes, use new and clean piping designed for R410A, and please care so that water or dust does not enter.
To disconnect the appliance from main power supply.
• This appliance must be connected to the main power supply by means of a switch with a contact separation of at least 3 mm.
The installation fuse (all type can be used) must be used for the power supply line of this conditioner.
3-EN
4-EN
+00EH99883601_00Ta.book Page 2 Thursday, September 8, 2011 4:34 PM