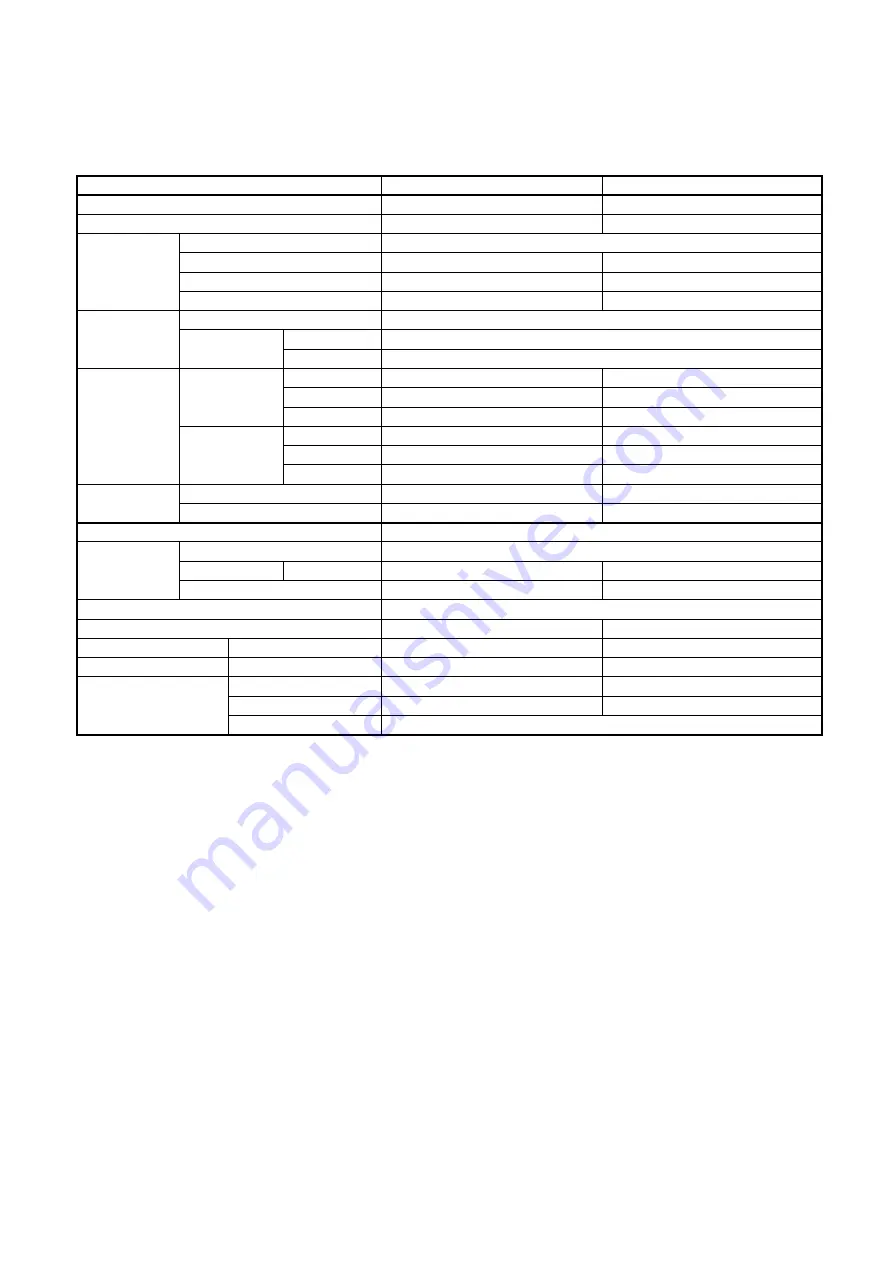
1-2. Ceiling type
Model name
Cooling Capacity
(kW)
Heating Capacity
(kW)
Power supply
220-240V~50Hz. & 208-230V~60Hz
(A)
(
kW
)
(A)
Zinc hot dipping steel plate
Model name
-
Panel Color
-
Height
(mm)
Width
(mm)
Depth
(mm)
Height
(mm)
Width
(mm)
Depth
(mm)
Main unit
(kg)
Ceiling panel
(kg)
Heat exchanger
Finned tube
Fan
Centrifugal (Multi Balde)
Standard air flow
H/M/L
(m
3
/hr)
Motor
(W)
Air filte
Standard filter attached (Long life filter)
Controller
-
-
Sound pressure level
H/M/L
(dBA)
Sound power level
H/M/L
(dBA)
Gas side
(mm)
Liquid
(mm)
Drain port
(mm)
VP25
MMC-UP0151HP-E(TR)
MMC-UP0181HP-E(TR)
4.50
5.60
5.00
6.30
Power consumption
0.033
0.38
Running current
0.37
Starting current
0.55
0.034
Appearance
Main unit
0.57
Electrical
characteristics
Ceiling panel
690
690
235
235
Ceiling panel
-
-
950
950
Main unit
-
-
Total weight
24
24
-
-
Outer diamension
Fan unit
840/690/540
960/720/540
-
-
94
94
51/49/43
52/49/43
36/34/28
37/35/28
Connecting pipe
12.7
12.7
6.4
6.4
- 19 -
Summary of Contents for MMC-UP0151HP-E
Page 41: ...2 2 Ceiling type MMC UP0151HP E TR MMC UP0181HP E TR 41 ...
Page 42: ...MMC UP0241HP E TR MMC UP0271HP E TR 6 4 12 7 42 ...
Page 43: ...MMC UP0361HP E TR MMC UP0481HP E TR MMC UP0561HP E TR 43 ...
Page 58: ...3 WIRING DIAGRAMS 3 1 4 way cassette type MMU UP HP E TR 58 ...
Page 59: ...3 2 Ceiling type MMC UP HP E TR 59 ...
Page 60: ...3 3 Concealed Duct Standard type MMD UP BHP E TR 60 ...
Page 61: ...3 4 Concealed Duct High Static Pressure type MMD UP HP E TR 61 ...
Page 62: ...Concealed Duct High Static Pressure type MMD UP HP E TR 62 ...
Page 63: ...3 5 Concealed Duct High Static Pressure fresh air intake type MMD UP HFP E TR 63 ...
Page 65: ...3 7 High wall type MMK UP HP E TR 65 ...
Page 249: ...MMU UP0361HP E TR MMU UP0481HP E TR MMU UP0561HP E TR 268 267 213 214 249 ...
Page 252: ...12 2 Ceiling type MMC UP0151HP E TR MMC UP0181HP E TR 025 024 252 ...
Page 254: ...MMC UP0241HP E TR MMC UP0271HP E TR 029 028 254 ...
Page 256: ...MMC UP0361HP E TR MMC UP0481HP E TR MMC UP0561HP E TR 051 028 027 256 ...
Page 261: ...MMD UP0151BHP E TR MMD UP0181BHP E TR 240 239 238 233 235 261 ...
Page 263: ...MMD UP0241BHP E TR MMD UP0271BHP E TR MMD UP0301BHP E TR 240 239 238 233 235 263 ...
Page 265: ...MMD UP0361BHP E TR MMD UP0481BHP E TR MMD UP0561BHP E TR 240 239 238 233 235 265 ...