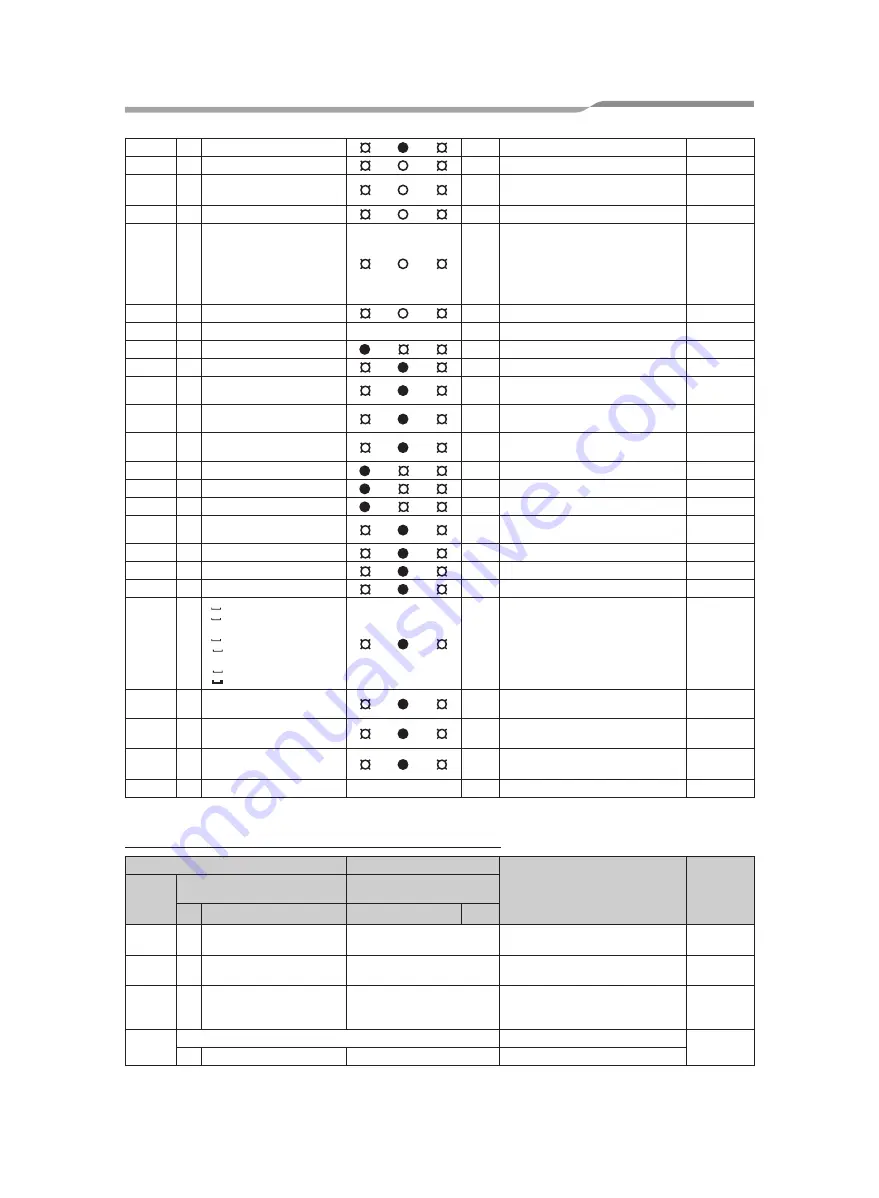
Installation Manual
Error detected by TCC-LINK central control device
TCC-LINK: TOSHIBA Carrier Communication Link.
L09
—
—
SIM
Indoor capacity unset
Indoor
L10
L10
—
SIM
Outdoor capacity unset
I/F
L20
—
—
SIM
Duplicated central control addresses
AI-NET,
Indoor
L28
L28
—
SIM
Over No. of connected outdoor units
I/F
L29
L29
01: IPDU1 error
02: IPDU2 error
03: IPDU3 error
04: Fan IPDU error
05: IPDU1 + Fan IPDU error
06: IPDU2 + Fan IPDU error
07: All IPDU error
SIM
No. of IPDU error
I/F
L30
L30 Detected indoor address
SIM
Indoor outside interlock
Indoor
—
L31
—
—
Extended I/C error
I/F
P01
—
—
ALT Indoor fan motor error
Indoor
P03
P03
—
ALT Discharge temp. TD1 error
I/F
P04
P04 01: Comp. 1 side
02: Comp. 2 side
ALT High-pressure SW system operation
IPDU
P05
P05 01: Phase-missing detection
02: Phase error
ALT Phase-missing detection /Phase error
I/F
P07
P07 01: Comp. 1 side
02: Comp. 2 side
ALT Heat sink overheat error
IPDU, I/F
P10
P10 Detected indoor address
ALT Indoor overflow error
Indoor
P12
—
—
ALT Indoor fan motor error
Indoor
P13
P13
—
ALT Outdoor liquid back detection error
I/F
P15
P15 01: TS condition
02: TD condition
ALT Gas leak detection
I/F
P17
P17
—
ALT Discharge temp. TD2 error
I/F
P19
P19 Detected outdoor unit number
ALT 4-way valve inverse error
I/F
P20
P20
—
ALT High-pressure protective operation
I/F
P22
P22
0
: IGBT short
1
: Fan motor position
detective circuit error
3
: Fan motor trouble
C
: TH sensor temp. error
(Heat sink overheat)
D
: TH sensor error
E
: Vdc output error
ALT Outdoor fan IPDU error
IPDU
P26
P26 01: Comp. 1 side
02: Comp. 2 side
ALT G-TR short protection error
IPDU
P29
P29 01: Comp. 1 side
02: Comp. 2 side
ALT
Comp position detective circuit system
error
IPDU
P31
P31
—
ALT
Other indoor unit error
(Group terminal unit error)
Indoor
—
—
—
By alarm device ALT
Error in indoor group
AI-NET
Check code
Wireless remote controller
Check code name
Judging
device
Central
control
device
indication
Outdoor 7-segment display
Sensor block display of
receiving unit
Auxiliary code
OPERATION TIMER PRE.DEF. Flash
C05
—
—
—
Sending error in TCC-LINK central
control device
TCC-LINK
C06
—
—
—
Receiving error in TCC-LINK central
control device
TCC-LINK
C12
—
—
—
Batch alarm of general-purpose
equipment control interface
General-
purpose
equipment I/F
P30
Differs according to error contents of unit with occurrence of alarm Group control branching unit error
TCC-LINK
—
—
(L20 is displayed.)
Duplicated central control addresses
1111058602_EN.indd 35
11/24/16 11:41 AM
1111058602_EN.indd 36
11/24/16 11:41 AM
FILE NO. SVM-17045
- 102 -