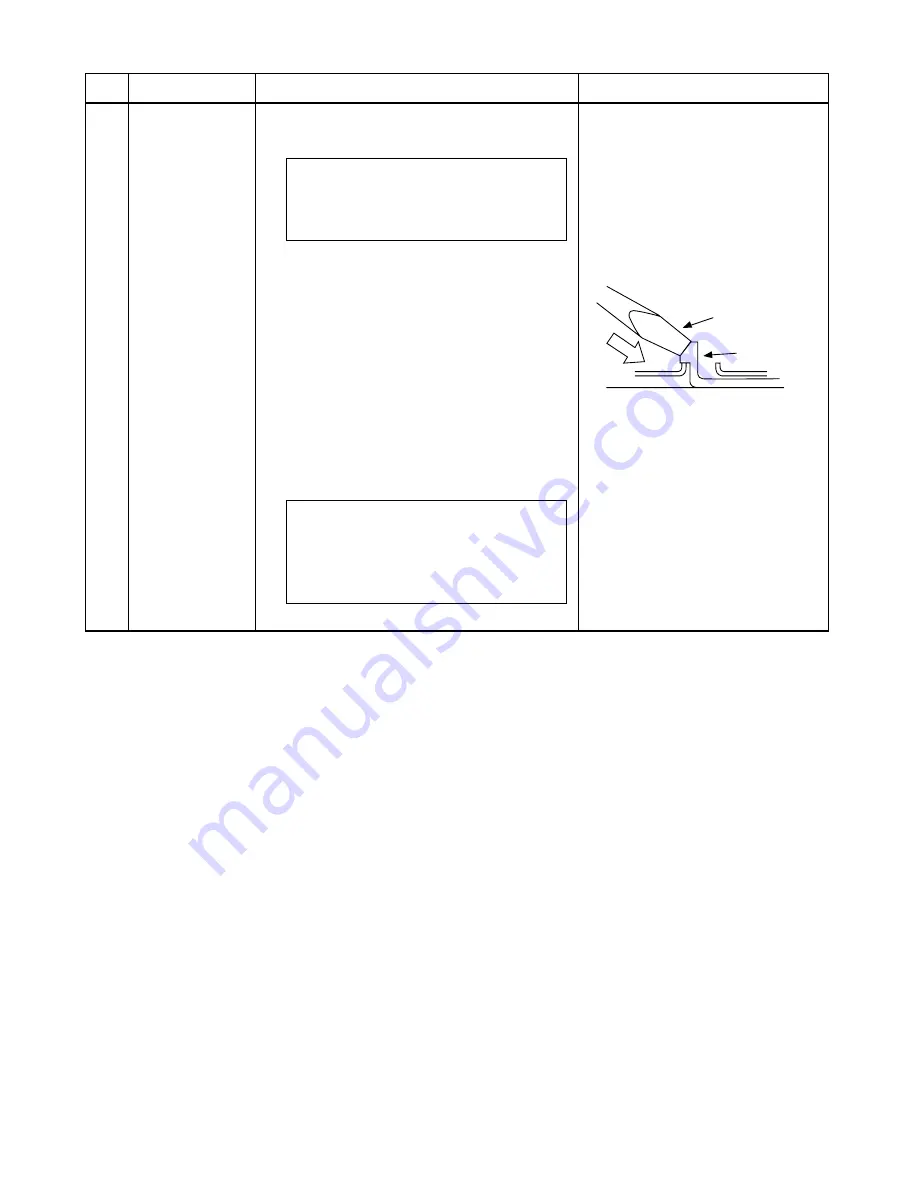
FILE NO. SVM-05026
– 70 –
No.
Part name
Procedures
Remarks
1. Detachment
1) Perform work of item 1 of
1
and 1 of
2
.
Requirement:
Perform the work on a corrugated
cardboard, cloth, etc. to prevent
scratches to the product.
2) Remove the front cabinet, and place it
down so that the fan guard side faces
downwards.
3) Remove the hooking claws by pushing a
minus screwdriver according to the arrow
mark in the right figure, and remove the
fan guard.
2. Attachment
1) Insert the claws of the fan guard in the
hole of the front cabinet. Push the hooking
claws (12 positions) by your hand and fix
the claws.
Requirement:
This completes all the attaching
work. Check that all the hooking
claws are fixed to the specified
positions.
9
Fan guard
Minus screwdriver
Hooking claw