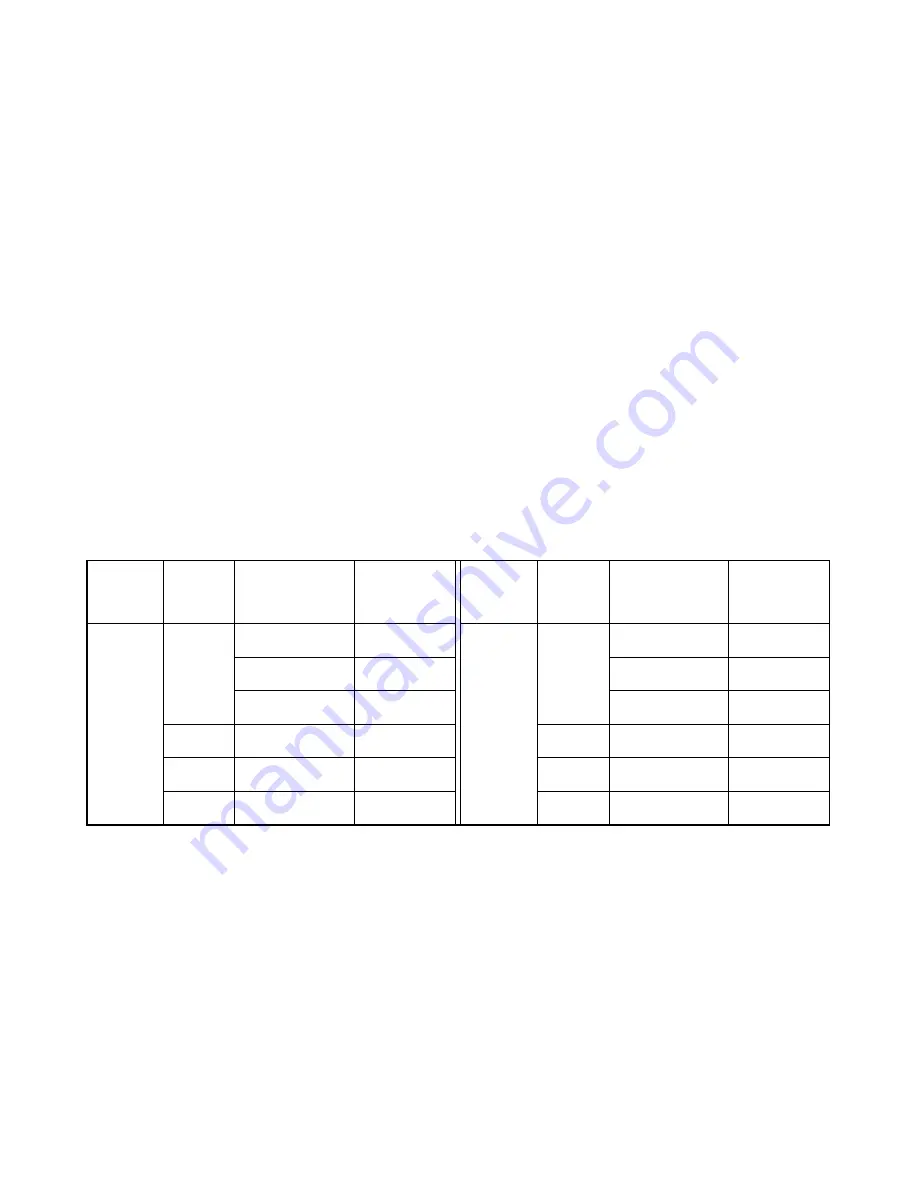
– 51 –
8-1-3. Power Factor Improvement Control
Power factor improvement control is performed
mainly aiming to reduce the current on much power
consumption of cooling/heating operation. Control-
ling starts from the time when input power has
reached at a certain point. To be concrete, IGBT of
the power factor improvement circuit is used, and the
power factor is improved by keeping IGBT on for an
arbitrary period to widen electro-angle of the input
current.
(4) Contents of operation command signal (Serial
signal) from outdoor unit controller to indoor unit
controller
The following signals are sent from the outdoor
unit controller.
• The current operation mode
• The current compressor revolution
• Outdoor temperature
• Existence of protective circuit operation
For transferring of these signals, the indoor unit
controller monitors the contents of signals, and
judges existence of trouble occurrence.
Contents of judgment are described below.
• Whether distinction of the current operation
status meets to the operation command
signal
• Whether protective circuit operates
When no signal is received from the outdoor
unit controller, it is assumed as a trouble.
8-1-2. Current Release Control
The outdoor main circuit control section (Inverter
assembly) detects the input current to the outdoor
unit. If the current value with compressor motor
speed instructed from indoor side exceeds the
specified value, the outdoor main circuit control
section controls compressor motor speed by reduc-
ing motor speed so that value becomes closest to
the command within the limited value.
Table 8-1-1 Compressor revolution range
Operation
mode
COOL
Combination
of indoor units
M10
M13
M16
○*
○*
○*
*
:
In case that any multiple indoor units are combined.
Compressor
revolution
(rps)
20 to 28
20 to 43
20 to 53
20 to 66
31 to 69
31 to 69
8-1-1. Capacity Control
The cooling capacity is varied by changing compres-
sor motor speed. The inverter changes compressor
motor speed by changing AC 220–240V power to
DC once, and controls capacity by changing supply
power status to the compressor with transis-tor
module (includes 6 transistors). The outline of the
control is as follows : The revolution position and
revolution speed of the motor are detected by
detecting winding electromotive force of the com
pressor motor under operation, and the revolution
speed is changed so that the motor drives based
upon revolution speed of the operation command by
changing timing (current transfer timing) to ex
change inverter output voltage and supply power
winding.
Detection of the revolution position for controlling is
performed 12 times per 1 revolution of compressor.
The range of supply power frequency to the com
pressor differs according to the operation status
(COOL, DRY).
No. of
operating
unit
1 unit
2 units
3 units
4 units
Operation
mode
HEAT
No. of
operating
unit
1 unit
2 units
3 units
4 units
Combination
of indoor units
M10
M13
M16
○*
○*
○*
Compressor
revolution
(rps)
15 to 52
15 to 63
15 to 67
15 to 90
17 to 90
22 to 90