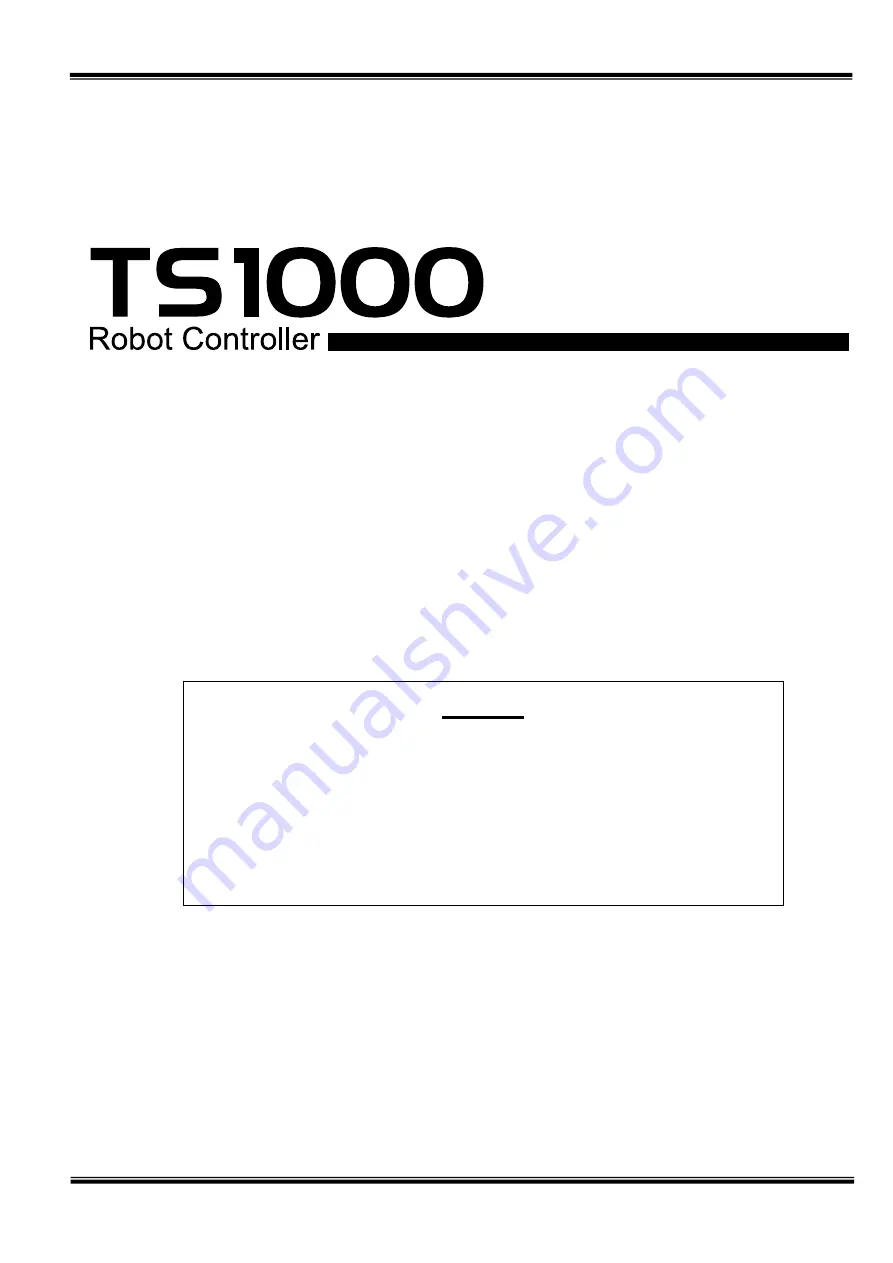
STE 71282-2
STARTUP MANUAL
Notice
• Make sure that this instruction manual is delivered to the
final user of Toshiba Machine's industrial robot.
• Before operating the industrial robot, read through and
completely understand this manual.
• After reading through this manual, keep it nearby for future
reference.
TOSHIBA MACHINE CO., LTD.
TOKYO, JAPAN