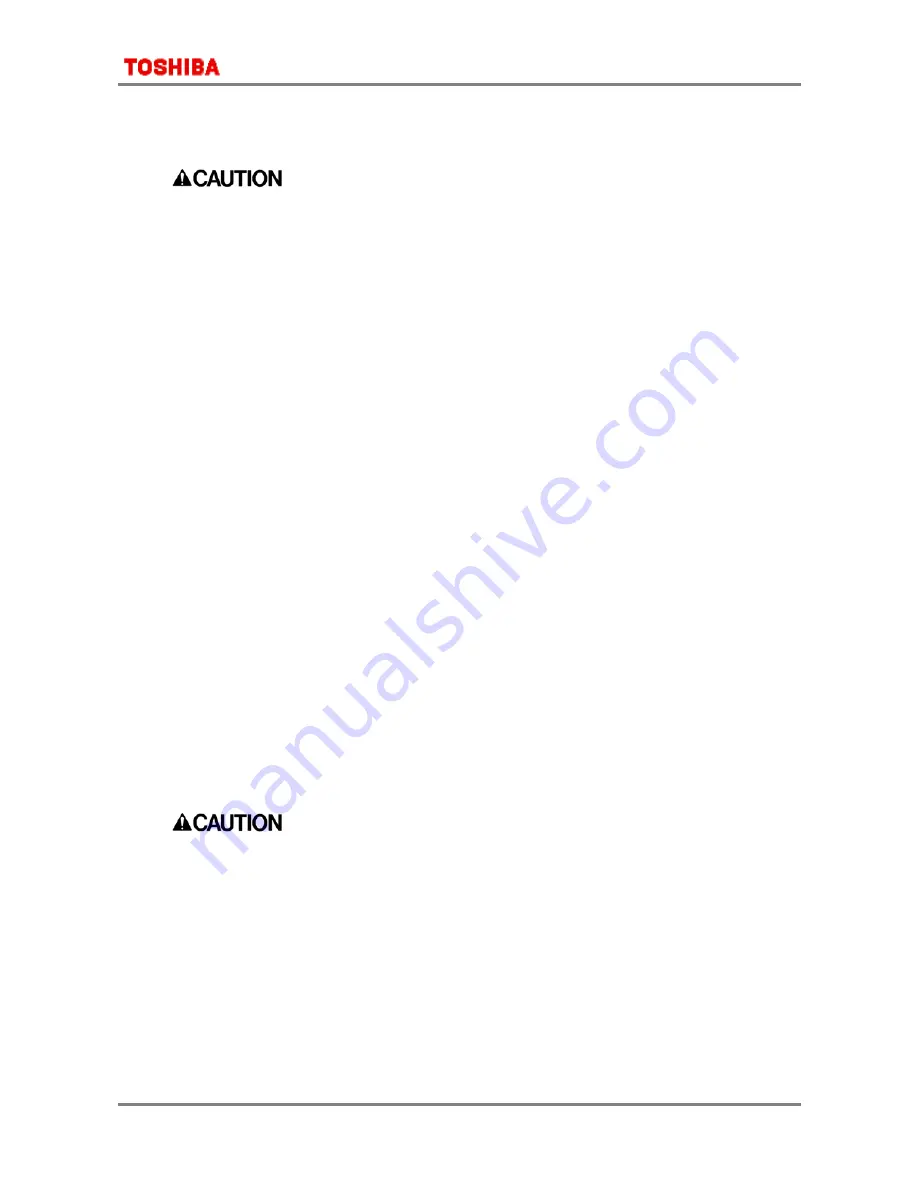
3 General Safety Precautions and Usage Considerations
3-11
3.4.2 Inspection
Sequence
c
Do not insert devices in the wrong orientation. Make sure that the positive and
negative electrodes of the power supply are correctly connected. Otherwise, the rated
maximum current or maximum power dissipation may be exceeded and the device
may break down or undergo performance degradation, causing it to catch fire or
explode, resulting in injury to the user.
d
When conducting any kind of evaluation, inspection or testing using AC power with a
peak voltage of 42.4 V or DC power exceeding 60 V, be sure to connect the electrodes
or probes of the testing equipment to the device under test before powering it on.
Connecting the electrodes or probes of testing equipment to a device while it is
powered on may result in electric shock, causing injury.
(1) Apply voltage to the test jig only after inserting the device securely into it. When applying or removing
power, observe the relevant precautions, if any.
(2) Make sure that the voltage applied to the device is off before removing the device from the test jig.
Otherwise, the device may undergo performance degradation or be destroyed.
(3) Make sure that no surge voltages from the measuring equipment are applied to the device.
(4) The chips housed in tape carrier packages (TCPs) are bare chips and are therefore exposed. During
inspection take care not to crack the chip or cause any flaws in it.
Electrical contact may also cause a chip to become faulty. Therefore make sure that nothing comes into
electrical contact with the chip.
3.5 Mounting
There are essentially two main types of semiconductor device package: lead insertion and surface mount. During
mounting on printed circuit boards, devices can become contaminated by flux or damaged by thermal stress
from the soldering process. With surface-mount devices in particular, the most significant problem is thermal
stress from solder reflow, when the entire package is subjected to heat. This section describes a recommended
temperature profile for each mounting method, as well as general precautions which you should take when
mounting devices on printed circuit boards. Note, however, that even for devices with the same package type,
the appropriate mounting method varies according to the size of the chip and the size and shape of the lead
frame. Therefore, please consult the relevant technical datasheet and databook.
3.5.1 Lead
forming
c
Always wear protective glasses when cutting the leads of a device with clippers or a
similar tool. If you do not, small bits of metal flying off the cut ends may damage
your eyes.
d
Do not touch the tips of device leads. Because some types of device have leads with
pointed tips, you may prick your finger.
Semiconductor devices must undergo a process in which the leads are cut and formed before the devices can be
mounted on a printed circuit board. If undue stress is applied to the interior of a device during this process,
mechanical breakdown or performance degradation can result. This is attributable primarily to differences
between the stress on the device’s external leads and the stress on the internal leads. If the relative difference is
great enough, the device’s internal leads, adhesive properties or sealant can be damaged. Observe these
precautions during the lead-forming process (this does not apply to surface-mount devices):
(1) Lead insertion hole intervals on the printed circuit board should match the lead pitch of the device
precisely.
Summary of Contents for TX49 TMPR4937
Page 1: ...64 Bit TX System RISC TX49 Family TMPR4937 Rev 2 0 ...
Page 4: ......
Page 13: ...Table of Contents ix TMPR4937 Revision History 1 ...
Page 14: ...Table of Contents x ...
Page 15: ...Handling Precautions ...
Page 16: ......
Page 18: ...1 Using Toshiba Semiconductors Safely 1 2 ...
Page 40: ...3 General Safety Precautions and Usage Considerations 3 18 ...
Page 42: ...4 Precautions and Usage Considerations 4 2 ...
Page 43: ...TMPR4937 2005 3 Rev 2 0 ...
Page 44: ......
Page 52: ...Chapter 1 Overview and Features 1 6 ...
Page 156: ...Chapter 7 External Bus Controller 7 56 ...
Page 491: ...Chapter 16 Removed 16 1 16 Removed ...
Page 492: ...Chapter 16 Removed 16 2 ...
Page 493: ...Chapter 17 Removed 17 1 17 Removed ...
Page 494: ...Chapter 17 Removed 17 2 ...
Page 495: ...Chapter 18 Removed 18 1 18 Removed ...
Page 496: ...Chapter 18 Removed 18 2 ...
Page 497: ...Chapter 19 Removed 19 1 19 Removed ...
Page 498: ...Chapter 19 Removed 19 2 ...
Page 506: ...Chapter 20 Extended EJTAG Interface 20 8 ...
Page 530: ...Chapter 22 Pinout and Package Information 22 10 ...
Page 542: ...Chapter 24 Parts Number when Ordering 24 2 ...